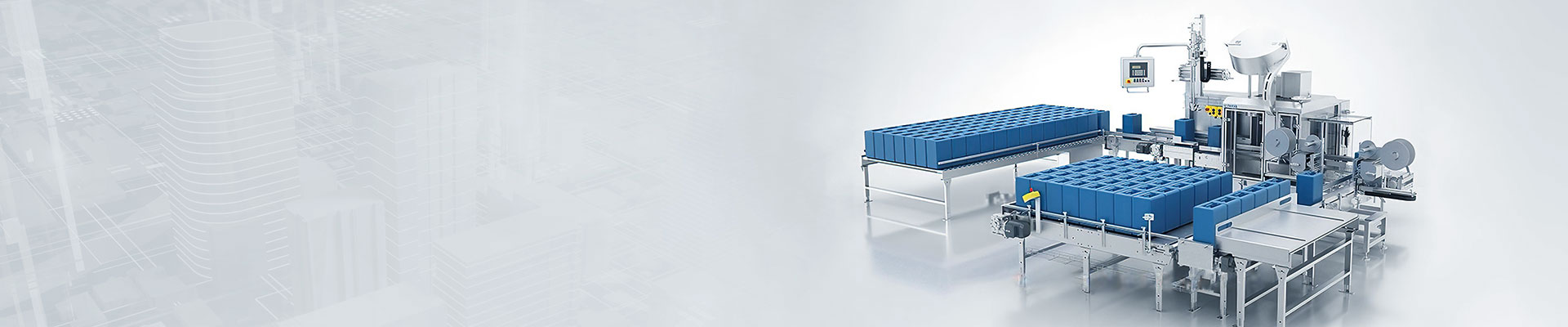
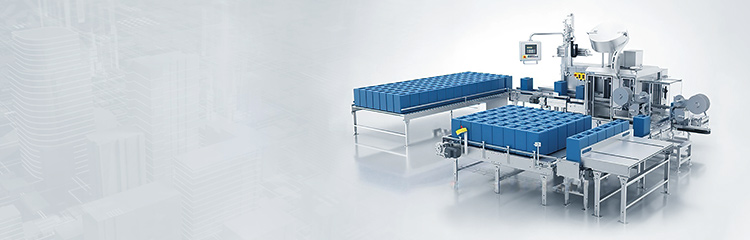

喂料系统即将两种或两种以上的物料按一定重量配比自动定量加入到混合配料罐内,经过混合达到预定要求后自动出料的过程。整个系统无需主控制台,只需称重模块、接线盒、称重控制仪表、PLC接线柜、触摸屏,主要硬件由两台计算机、高性能的微称重控制器、人机界面、高速高精度的称重单元和国际著名低压电器组成。实现了对原料的自动称量,并完成称量误差的自动补偿。实现了反应釜各阀门的顺序自动开关,配料自动设定以及其他相关辅助设备的自动控制,实现了对反应釜上料系统的数据采集、数据显示与数据控制。
反应釜采用无料钟串罐式,分为受料斗、料罐、气密箱等组成部分。在上料过程中,先投进受料斗里,随后放人料罐中,在这个过程中,由于料斗不能和大气相通,通过控制反应釜放散阀、均压阀、上密阀、柱塞阀、下密阀的顺序开关来实现料斗的正常下料,通过控制、来实现料斗配料,检测设备采用温度探尺与雷达探尺相配合。
各种原料由螺旋运到反应釜,送人受料斗中,受料斗最多可装4罐料,料罐放散完毕后打开上密阀和柱塞阀向料罐装料,装料完成后料罐进行均压。料斗准备接受下一批釜料就进行配料,首先打开下密阀并将料流调节阀打开至设定开度,料罐中的釜料通过料流调节阀流到旋转的配料溜槽上。在配料期间,通过称重模块探测料流,该装置可发出料罐清空信号。一旦料罐清空,关闭料流调节阀和下密封阀,打开放散阀进行放散,准备下一次装料。
一批料中,允许设定两个不同的配料位置,当探尺达到规定的料线位置后,自动提升到位,发出配料信号,下密封阀打开,配料溜槽进行启动。旋转到设定速度并且到达配料位置,开启料流调节阀,按照批重及规定的配料程序,调节料流调节阀开度和溜槽倾角,使每圈料流均匀、重量相等和首尾相接地向罐喉任意配料。为了减少料头料尾不均匀现象,每批配料完后,配料角度自动调整60°,当排料程序发出后,称量斗闸门开,料排出。当称量值为控制值(初始时为设定值的95%)的5%时,发出料空信号并关闭闸门,当闸门关好并称空好后,振动筛或给料机开始启动。称量值到控制值(经补正)时,振动筛或给料机停机,进行满称量。若达110%控制值(经补正)时发出声光报警信号。振动筛或给料机启动5s后,还未发出斗“满”信号,就会发出上卡料报警信号。