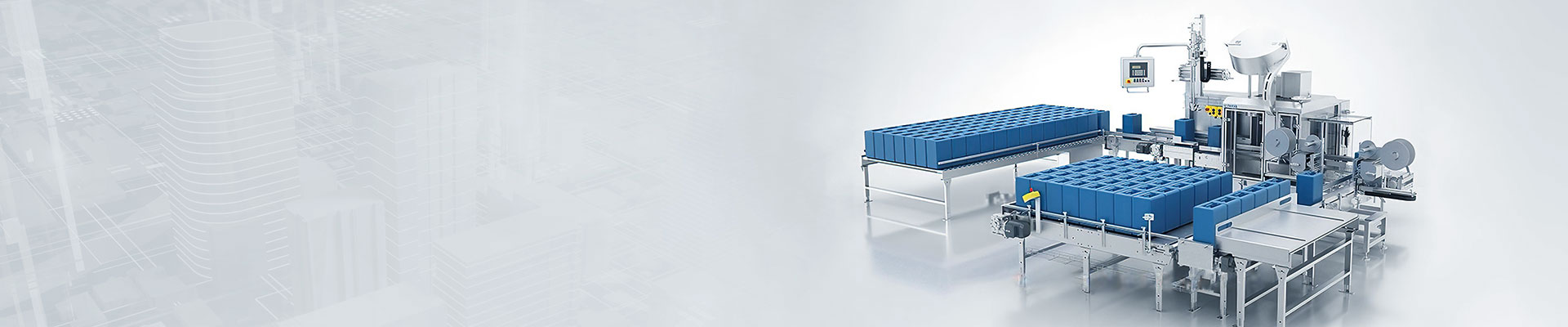
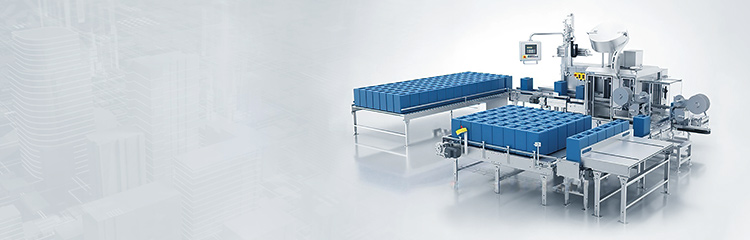

称重配料系统采用变频器对给料进行两档调速控制,从而实现4种物料的快配、慢配和点配控制功能,保证了变频给料的精度和速度。启动预先设置的计量进料程序后,称量并存储称量反应釜皮重,然后依次控制各种配料如溶剂、助剂、液体等进入称量反应釜,其中干物料用振动盘计量进料,粉末料由螺旋进料器计量进料,液体料则由液压阀计量进料,糊状物由泵进料。每一种配料都先后使用粗料和细料两种进料方式,以保证称量精度达到98%~99%。物料重量由安装在支撑架上悬置称量反应釜的3个称重仪表转变为电信号,经A/D转换读入计算机进行重量计算,去除皮重后与设定值比较,其结果作为控制物料切换或粗、细进料转换的依据。完成称量的混合物通过活门排放至可加热的反应罐、搅拌,再用泵打入溶解器,进入溶解制液工序。
上料系统由称重模块、称重变送器、西门子S7-200PLC、转子泵、变频器、落料限位开关、接近开关和上位工控机(IPC)等部件构成上位工控机(IPC)通过PC/PPI通信电缆与PLC连接,实时交换数据,完成现场参数的显示、记录、监控和报警功能,支撑在称重斗上的称量模块将代表重量的电信号经过称重变送器后转换成4~20mA的标准信号,再由PLC的A/D模块采集。此信号将作为振动给料机定量给料和统计实际累积重量的依据。
供料系统设定为两种控制方式,即手动控制和自动控制,自动控制方式又包括单步和连续方式。手动操作主要在系统调试、维修时或者PLC发生故障时使用。自动控制方式是配料系统的正常工作方式,在进行自动操作时,根据生产要求,在上位机通过键盘输入4种物料的配比,由上位机计算出各种物料的快配目标值和标准设定值,当1号物料快配料目标值小于标准设定值时,PLC发出高速指令,使1#给料工作在高频状态,1号物料快速落入称重斗,以提高进料效率,同时在上位机上实时显示1#物料的净重,当物料达到设定的快配料目标值时,变频器切换到较小的输送频率,慢速输送给料;当称重值小于1号料的标准设定值时(如差值在允差范围外),PLC将自动启动点动修正,1号料继续配料,以保证配料精度;如差值在允差范围内,PLC将输出停止信号,输送给料停止运转,1#输送给料结束。同时进入2#输送给料。2号到4号料的配料过程和1号料的配料过程雷同,直到4种物料配完后,完成一个批次的配料周期。