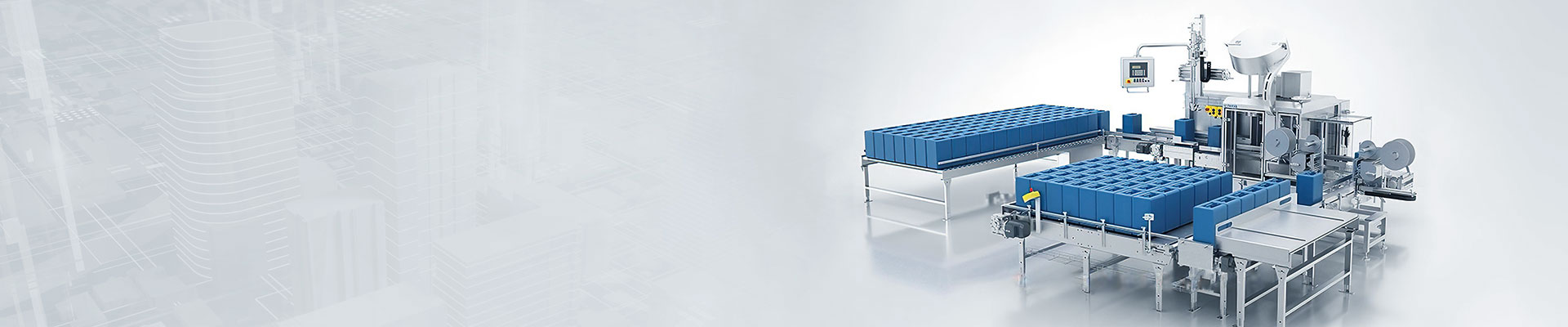
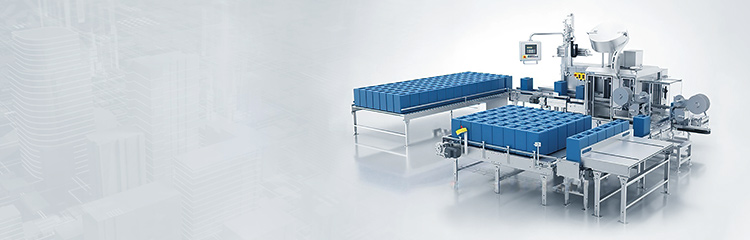
Intelligent batching system usually refers to a system in which a reaction kettle is used as a weighing container, and a variety of raw materials are added and mixed in turn during the stirring process according to preset procedures and weight values. A batching system that groups a variety of materials according to the similarity of weighing values, adds them into different weighing containers for measurement, and then mixes them together. Its characteristics are: fast weighing speed, high measuring accuracy and moderate investment.

The Batching system is a process in which two or more materials are automatically and quantitatively added into the mixing batching tank according to a certain weight ratio, and are automatically discharged after being mixed to meet the predetermined requirements. Widely used in chemical industry, medicine, feed, building materials, metallurgy and other industries to control the mixing process of ingredients.
The COMputer with stable performance is used to complete data acquisition and communication processing, which is convenient to improve processing accuracy and reduce cost, and the data is output and managed through the com communication interface of the computer itself; Mitsubishi F900 touch screen is selected to replace the conventional weighing display as the man-machine interface, which makes the interface programming between PLC and weighing display easier and enhances the display function.
There are several reaction kettles in the feeding system to control the weight of multiple ingredients. Each reaction tank is composed of 3 or 4 Weighing modules. Each weighing module is connected in parallel or in series by 4 or 6 signal wires to the signal wire junction box of weighing module, and then connected to the weighing display. The signal of weighing module is 2MV/V, and the signal with high or low sensitivity is transmitted. It must be recognized by the weighing terminal and converted into an analog signal, which is sent to the analog signal acquisition module of PLC.
The main hardware of the whole feeding system consists of two computers, a high-performance microcomputer controller, a man-machine interface, a high-speed and high-precision weighing unit and internationally renowned low-voltage electrical appliances. Combined with professional control software independently developed, chemical automation control is realized, with high measurement accuracy and low manufacturing cost.
Volume: 100L∼100000L (series specification);
Inner tank: the inner surface is polished by mirror (roughness Ra<0.4µm);
Head form: conical head, elliptical head or dish head, and the inner surface is polished by mirror (roughness Ra<0.4µm);
Jacket forms: full jacket, semi-circular coil jacket and honeycomb jacket;
Thermal insulation material: filled with pearl wool, rock wool or polyurethane;
Surface treatment method of the outer shell: mirror polishing or matte finish of 2B primary color or matte finish of 2B;
Stirring device: center (eccentric) stirring or side stirring at the top; Blade forms: frame type, anchor type, propulsion type, blade type, turbine type, etc. 8. Mixing speed: 10120 r/min (constant speed) or stepless speed regulation and frequency conversion speed regulation;
Form of level gauge: glass tube level gauge, static pressure sensing level gauge, ultrasonic level gauge and RF capacitive level gauge;
Leg form: triangular pyramid form, round tube type;
Tank configuration: quick-opening manhole, sight glass, thermometer (liquid crystal digital display or dial pointer), sampling port, air respirator, CIP cleaner, feed liquid inlet and outlet, standby port, pH meter port, heat medium inlet and outlet, refrigerant inlet and outlet, etc.
Material: inner tank SUS304 or SUS316L; The jacket and outer protective shell are SUS304; 13. The welding points of process openings such as inlet and outlet nozzles, mirrors, manholes and the inner tank body adopt flanging process arc transition, which is smooth, easy to clean and has no dead angle, and beautiful appearance; And the outer shell can be designed as required.