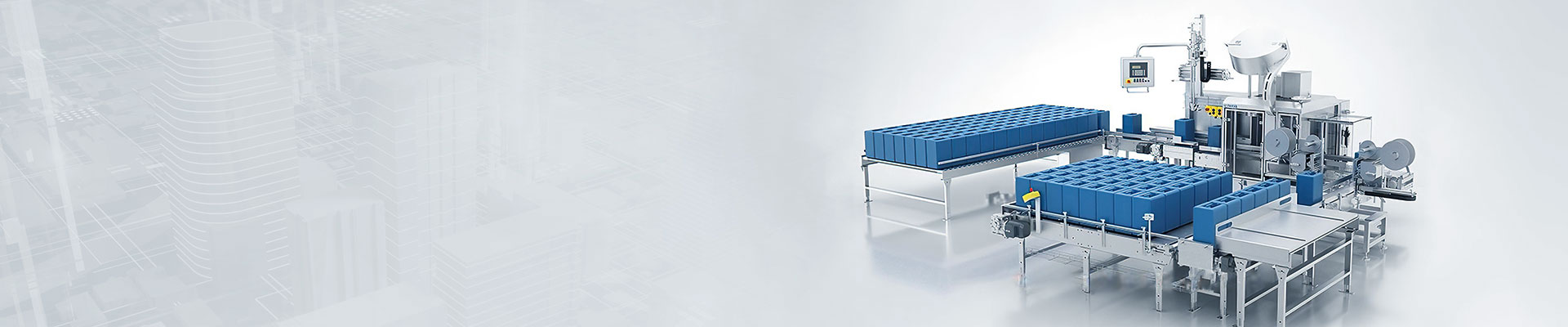
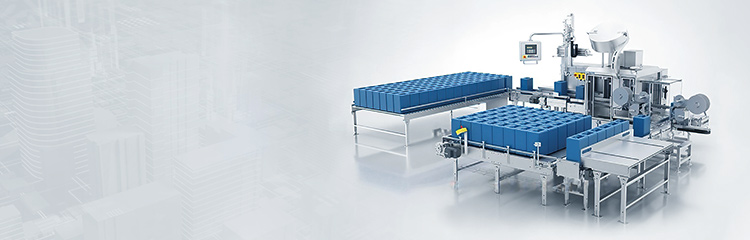
The belt scale is used for quantitative feeding of bulk materials. During the feeding process, the belt is continuously fed. The feeder transports the materials from the user's feed bin or other feeding equipment and conducts weight detection through the weighing bridge. The measured weight signal and the speed signal are sent to the integrator for differential processing and display the instantaneous flow rate in tons per hour for comparison, and according to the output of the corresponding signal value (PID signal), the speed of the motor is changed by the frequency converter to change the feed amount, so that it is certain with the set value, so as to complete the control of the constant feed flow.

Belt scale converts the measured weight parameters into analog voltage or analog current by analog weighing module, and transmits them together with the instantaneous speed detected by the velocity sensor to the digital transmitter. After the conversion of the digital transmitter, the output digital signal is sent to the intelligent weighing controller of the belt scale, and the instantaneous flow and accumulated weight of the material are displayed by microcomputer conversion based on the integration principle. The measurement signal is transmitted to the control system through the current isolation module to complete the dynamic process of remote display and production flow control. The electronic control system is composed of main control console, variable frequency cabinet, PLC host, testing device and driving device. The main control console adopts advanced technology and reliable performance programmable controller equipped with weighing module position sensing and other testing devices, driving drum, cleaner, etc. The driving component adopts high-performance vector control inverter to control the motor. Complete various functions such as stacking, blanking, soft start, soft stop and speed regulation during the operation of the belt conveyor. Equipped with the status display, each belt is installed under a weighing sensor, when the coal on a belt exceeds the limit value, the corresponding pressure switch is closed to provide PLC signals for stacking through program analysis, and display the overload state. The position switch is installed on the left and right side of the belt, and once the belt runs off, the position switch will be triggered to close, and the correction device of the driving drum will be automatically corrected by PLC analysis. Install a certain height of coal level detection device on the ground, as long as the coal falls to this height, the height position switch is closed, and the PLC drives the cleaner to clean up.
System control can start and stop independently, with pressure overload and alarm function, power frequency conversion switching function, belt deviation processing function, abnormal can automatically trip to power frequency function and automatic blanking cleaning function. The main circuit of the belt electromechanical control system has two independent 10kV power supply lines, which are divided into two transformer channels through the bus bar, and the 1# transformer is 10kV/380V type, which supplies power to the frequency converter, and each frequency converter has the power frequency/frequency conversion switching function (such as frequency converter 1). KM11 K12 control frequency conversion work KM13 switch to power frequency operation), and then connected to the motor respectively for control, 2# transformer 10kV/380V type, through low-voltage distribution to the PLC cabinet power supply, or process control power supply.
Main technical parameters:
System accuracy: +/-0.125%
Weighing range: 1~8000t/h
Belt width: 500~2400mm
Belt speed: 0~4m/s
Belt conveyor inclination: ≤6 degrees (special materials ≤10 degrees)
Pull type electronic strain gauge load cell:
◆ Shell: "S" type seal protection
◆ Nonlinear: <0.03%FS
◆ Non-repeatability: <0.01%FS
◆ Creep: <0.02%FS
◆ Zero output: ±1%
◆ Under the maximum flow rate, the displacement of the pressure point of the sensor elastomer is not more than 0.2mm
◆ Temperature sensitivity: Interval: 0.0008%FS/oF zero: 0.0015%FS/oF
◆ Lag error: 0.02%
◆ Sensitivity error: ± 0.1%
◆ Overload capacity: 150% of sensor capacity
Speed sensor:
◆ The speed sensor is installed on the tail roller, the speed roller or the speed roller, and the speed roller/roller is installed on the upper surface of the return belt, eliminating the influence caused by the belt slip. The speed sensor is a digital brushless pulse generator. When the belt is running, the speed sensor emits a series of speed pulses, each pulse represents a unit length of the belt travel, and the pulse frequency is proportional to the speed of the belt.
◆ The shell material is cast aluminum, which can be adapted to the open-air working environment.
◆ AC pulse generator does not need to adjust or replace the brush.
ZKB-60 weighing instrument
◆ Readiness: better than 0.05%
◆ Full digital operation, panel operation, key input, simple and convenient
◆ With automatic zero setting, automatic interval, fault diagnosis, power failure to maintain data and other functions
◆ With unique electronic calibration, chain calibration, hanging calibration and physical calibration and other calibration methods
◆ Optional remote counting function, with optional multi-point display
◆ Heavy display output: eight digits with decimal point, minimum display 0.01t
◆ Flow display output: four with decimal points, the unit is ton/hour, or kg/hour
◆ Analog output: 4-20mA or 0-20mA current output proportional to flow
◆ Communication interface: optional RS-485 or RS-232 serial port