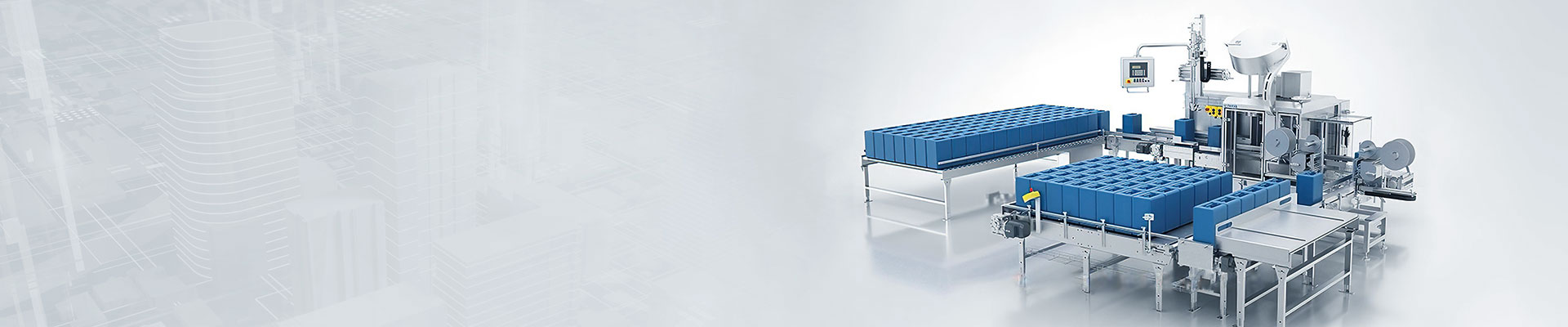
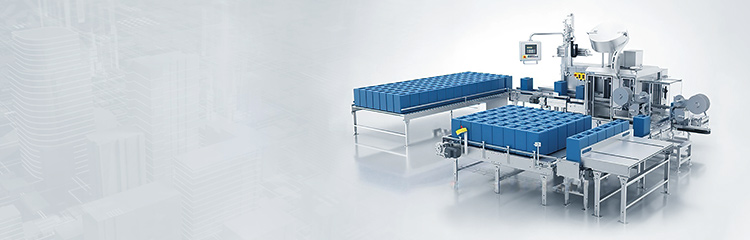
The main electrical control part of the filling machine is a Siemens S7300 series PLCCPU317-2PN/DP. The filling valve control part is a control system module EX484. Siemens PLC is responsible for the safety functions, speed control, high level buffer tank level control, return cycle heating, CIP in-situ cleaning, height adjustment, signal exchange, etc. The control system is composed of Siemens PLC buses. Siemens PLC control system consists of two buses, Profibus and ASI bus. The filling machine is responsible for filling valve metering cylinder level control, tank filling level control, filling valve pneumatic control, filling angle time control and so on. The filling valve control is composed of two buses: Powerlink bus and CANbus bus.

Automatic Filling machine operation mode is set to automatic operation, open the switch to select "automatic", the drive motor runs, drive conveyor belt running, when the weighing module detects that the bottle reaches the specified position in a state of stop, the conveyor belt stops running or the stop switch is activated, the conveyor belt stops running. When the bottle is filled with liquid, the system automatically starts the motor, which is driven again until it reaches another stop state and then stops again, and this action is carried out cyclically.
Positioning switch is set on the Filling system, when the bottle reaches the specified position, the conveyor belt operation is suspended, the weighing and filling machine then starts to carry out the filling work, and the filling is completed within 5S. If any abnormality or error occurs during this period, the system will send out an alarm signal in sound and light mode.
There are two load cells and adders set up to detect the state of the bottles, and at the same time, the number of filled and empty bottles are recorded separately, counting from the start of the system operation, generally 1 million bottles for a range. Filling system reset and data zeroing are done manually to prevent data loss or system misoperation caused by automatic zeroing.
Technical Parameters
Weight range: 10~20kg
Material interface: DN40 material
Inlet pressure: <0.6MPa
Filling speed: 6~8 buckets (20L)/minute (through diameter 1.5", material flow rate to ensure that 20L/min)
Filling accuracy: 0.2 level gun structure, contact with the material part of the material material for the 316, 316L stainless steel, the rest of the material for the 304 stainless steel, carbon steel and so on.
Gas source: Pressure 0.5±0.1Mp, consumption 10m3/h, quick connector 8㎜ gas pipe
Power supply: 220(-15%~+10%) VAC, 50Hz