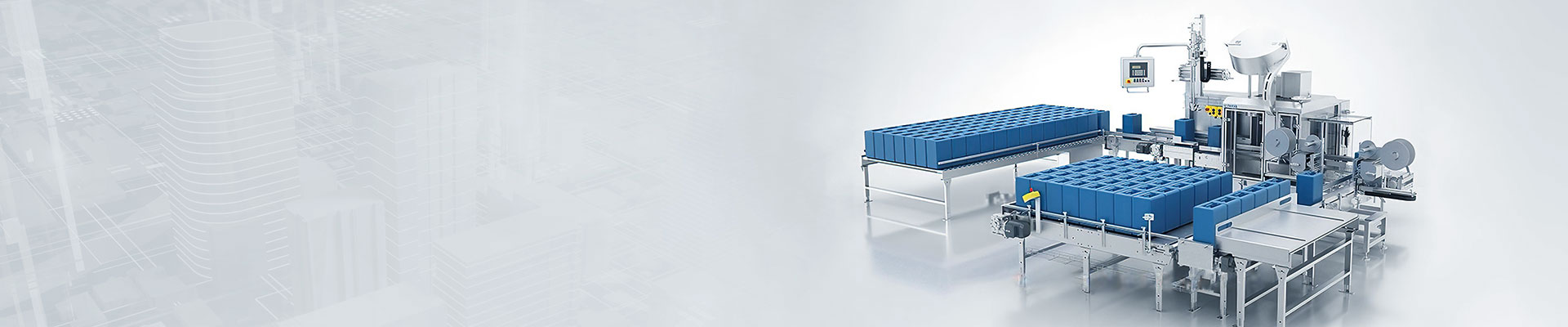
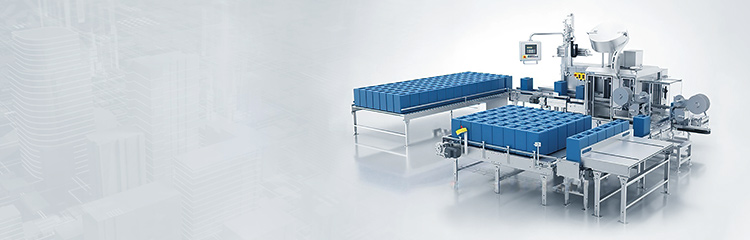
The methanol filling machine reads the data stored in the chip through the interface of the weighing module, processes the data of the weighing module through the serial port, and is responsible for receiving the polling signal sent by the server to the base station to give the response information. If the communication frame is the data frame sent by the server to the base station, the data sent by the weighing module is directly sent to the serial port sending buffer. The received data is checked and simply analyzed and sent to the serial port receiving area to ensure the stability of the signal.

Weighing and Filling machine adopts Electronic scale to perform the function of deducting weight automatically and clearing the weight on the weighing table to zero, 30 groups of formulas are stored in the electronic scale, which is convenient for the replacement of products, and the two-stage automatic filling of large and small materials ensures the degree of certainty.
Automatic identification of the tare value of empty drums, over range refusal to fill, avoiding human error. Automatic correction of liquid drop, tracking target value, alarm for overfilling. Align the barrel mouth and press the start button to fill. Display the completion of filling, cumulative weight and number of times, can be connected to an external printer. Manually put the barrel pound table, the use of insertion filling, to avoid causing the material flying shallow on the barrel, affecting the external packaging.
The Filling system will automatically perform the weight deduction function to zero out the weight on the weighing platform. After the filling is completed, manually push the barrel out of the weighing platform. In case of emergency, press the emergency stop button to cancel the filling.
Technical Parameters
Maximum weighing capacity: 1200kg
Minimum sensing capacity: see kg
Filling range: 1-3kg
Filling error: ±0.01-0.03kg (depending on flow rate and pulse force)
Power supply: AC220/50Hz
Using gas source: 0.8Mpa
Use temperature: -10℃-50℃