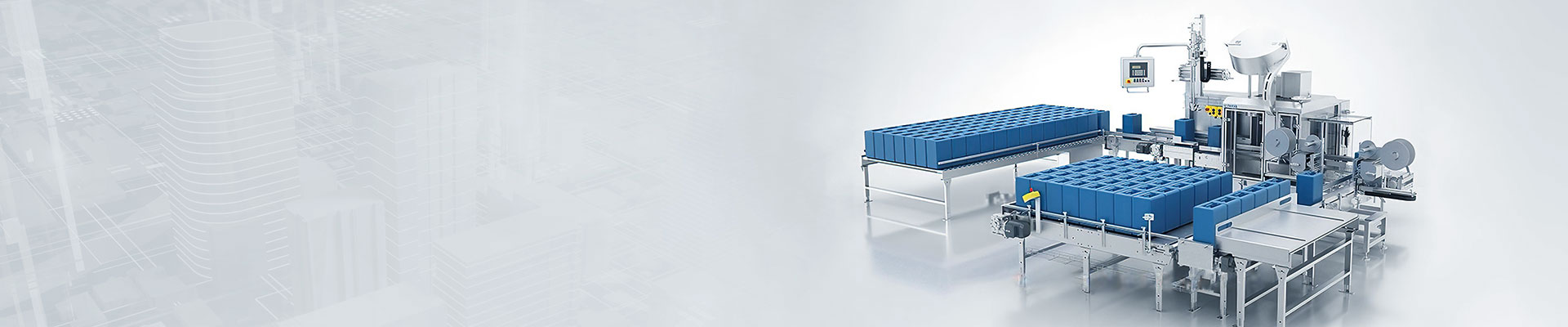
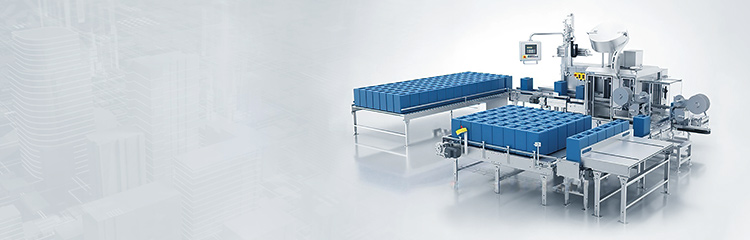
Weighing and mixing equipment to achieve the main and auxiliary batching machine two-stage control, each screw is driven by a motor; Two material level sensors; A speed sensor; A weighing sensor and a frequency converter. The switching quantity controls the running state of the motor, the input of the control end of the inverter is determined by the digital input of the PLC, and the high-frequency pulse is transferred by the inverter and transmitted to the spiral drive motor. The level sensor begins to detect whether the hopper contains material, and the speed of the motor is monitored by the speed sensor.

Automatic batching equipment is a mechatronic system integrating automatic control technology, measuring technology, weighing technology and computer management technology. It has the advantages of digital display of weight value, dynamic display of process screen, formula modification and management, fast dosage speed and high control precision. Adopting complete screen system of upper computer, it has the functions of automatic storage of dosage data, inquiry of dosage process list, statistics and printing of shift, day, month and year report.
Automatic batching machine is composed of weighing module and weighing instrument and communication cable, adopting the combination of PID regulation of measurement deviation and frequency conversion speed regulation, hardware setting, parameter setting and software design process in frequency conversion control. Multi-output each batching and conveying production line is strictly coordinated and controlled to monitor and regulate the material level and weight timely and accurately. Connecting on-site weighing instrument, controlling on-site equipment and weighing Feeder frequency converter through bus, with higher degree of intelligence and fast processing speed. In the process of batching production process, the main material and auxiliary materials will be matched according to a certain proportion to complete the measurement of the conveyed materials. It mainly undertakes real-time control of conveying and weighing process, and completes fault detection, display and alarm, and also outputs signals to the frequency converter to adjust the screw speed.
The feeding system mainly adopts SIMATICS7-/300 series PLC, and the system is realized by S7-/300 as well as the upper computer to realize the two-level control of the main and auxiliary batching machines. Each spiral is composed of a drive motor; two material level sensors; a speed sensor; a load cell and a frequency converter. The switching quantity controls the running status of the motor, and the input of the inverter control terminal is determined by the digital input of PLC, which is adjusted to high-frequency pulse by the inverter and delivered to the screw driving motor. The material level sensor starts detecting whether the hopper contains material or not, and the speed of the motor is monitored by the speed sensor.
Description of the main functions of the loading system
Manual operation and automatic control functions for dosage are realized.
An aesthetically pleasing and practical dynamic simulation of the production process that displays the real-time working status of each material as well as the target weight, actual weight and error values.
Store recipe presets and recall, modify, delete and query recipes at any time.
In the dosage process there is a material shortage automatic alarm function, can be online with the same material manually replace the tank storage number.
Features operator rights management, on-site management and networked remote services.
Adopting industrial computer as the upper computer monitoring system, WINCC monitoring configuration ensures the stability, reliability and long-term performance of the system.
The system adopts man-machine dialog, simple operation and maintenance.
Remote management can be realized and the computer in the control room can be networked with the computer in the general manager's room. The general manager can view the production situation and production reports in real time.
Adopting frequency conversion reaction tank to control the feeding, improve the dosing precision, so as to improve the quality and stability of products.