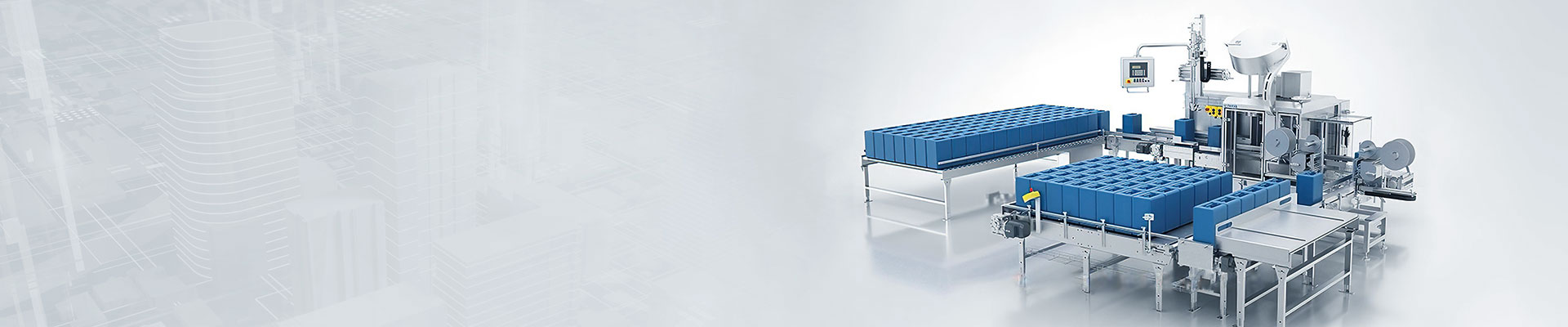
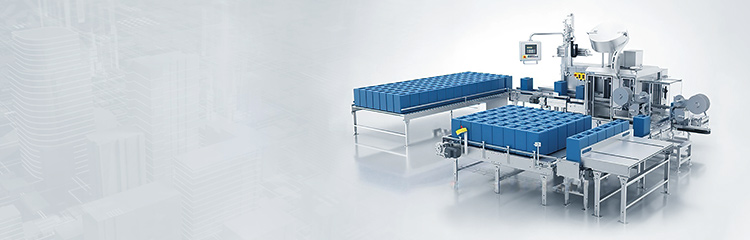
Weighing module Taking a typical chemical reaction kettle as an example, three pressure weighing modules installed at the bottom of the reaction kettle transmit the weight signal of the kettle body to the junction box. Each weighing module signal is connected in parallel in the junction box, and the angle difference can be adjusted according to the load of each weighing module, and the collected weight signal is sent to the weighing end or weight transmitter. The weighing terminal or weight transmitter processes the weight signal into corresponding weight data.

The weighing module is a conversion device used to convert weight signals or pressure signals into electrical signals, using a metal resistance strain gauge to form a measurement bridge circuit, made by utilizing the principle that metal resistance wires elongate and become thinner under tension and increase in resistance, i.e., the effect of the metal resistance changing in response to the strain applied (strain is a change in size).
The principle of construction of the metering module metal resistor has the property of impeding the flow of current, that is, it has resistance (Ω), and its resistance value varies according to the type of metal. The same kind of metal wire, generally the more slender, the greater its resistance value. When the metal resistance wire by external forces and stretch, its resistance value will be in a certain range of increase or decrease. Therefore, the metal wire (or film) tightly attached to the object under test, and this kind of wire or film is very thin or very thin, paste and very perfect, then when the object under test by external forces and stretch, the metal electric anode wire (film) will also be proportional to the expansion and contraction of the value of its Yang will also change accordingly.
The analog signal of the weighing module is converted into digital signal by the high-speed A/D converter module, and then the high-speed A/D transmits the digital signal to the PLC through RS485 communication, and the PLC processes the data and controls the valves, motors and other on-site equipments. The PLC processes the data and controls the field equipment such as valves and motors. The other expansion port is connected to the touch screen HMD, which can display the system process flow, view all parameters, monitor the real-time operation of the system, view the historical trend, and access the formula to call the formula and other functions.
Technical characteristics
Range: 5Klb~250Klb
Technical indicators
Rated load:5/10/20/30/40/50/60/75/100/150/200/250 Klb
Accuracy:C3
Certification:OIML R60 C3 ,OIML R60 C4
Maximum calibration index:max3000n
Minimum calibration value E:max/5000 v min
Combined error:≤±0.030(%FS)
Creep:≤±0.024(%FS/30min)
Temperature effect on output sensitivity:≤±0.017 (%FS/10℃)
Temperature effect on zero output:≤±0.023(%FS/10℃)
Output sensitivity:3.0±0.008(mv/v)
Input Impedance:700±7(Ω)
Output Impedance:703±4(Ω)
Output Impedance:703±4(Ω)
Zero Output:1.0(%FS)
Temperature compensation range:-10~+40(℃)
Allowable operating temperature range:-35~+65(℃)
Recommended excitation voltage:5~12(DC)(V)
Maximum excitation voltage:18(DC)(V)
Safety overload range:120(%FS)
Limit overload range:150(%FS)