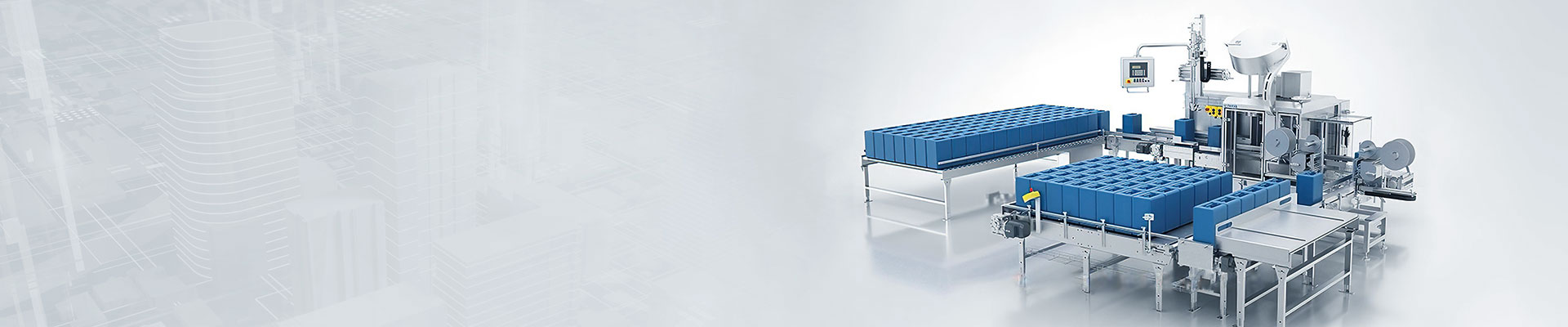
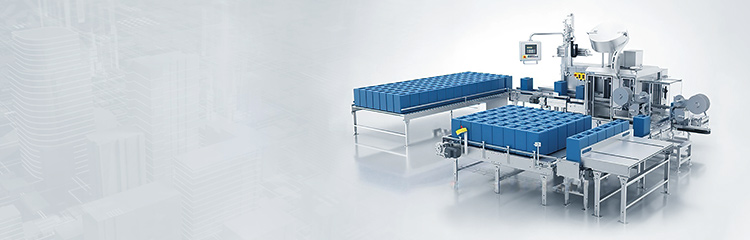
The automatic unloading system has a weighing instrument that needs communication, and uses computer for online monitoring and management, which has high requirements for weighing speed, weighing accuracy, system compatibility and scalability. It is suitable for remote I/O systems for communication between the system and external batching equipment. It is suitable for automation occasions with high time requirements. Digital signals are used to communicate between the middle layer or different layers of bus batching equipment to realize the data transmission between the weighing instrument and the PLC CPU. Each weighing instrument comes with DP communication interface, the PLC CPU is connected with the weighing instrument through the bus, and the address of each weighing instrument in the PROFIBUS-DP network is assigned in the STEP7 programming software, and the real-time weighing amount of each instrument can be read directly.

The weighing and proportioning system uses frequency converter to control the speed of feed in two levels, so as to realize the control function of fast, slow and point allocation of 4 kinds of materials, and ensure the accuracy and speed of variable frequency feed. After starting the pre-set feed metering program, weigh and store the tare weight of the weighing reactor, and then control the various ingredients such as solvents, auxilaries, liquids, etc. into the weighing reactor in turn. Dry materials are fed by vibrating disk, powder is fed by screw Feeder, liquid is fed by hydraulic valve, and paste is fed by pump. Each of the ingredients has the use of coarse material and fine material two feeding methods to ensure that the weighing accuracy reaches 98% to 99%. The weight of the material is converted into an electrical signal by three weighing instruments mounted on the support frame and suspended weighing reactor, which is read into the computer through A/D conversion for weight calculation. After the tare is removed, the result is compared with the set value, and the result is used as the basis for controlling material switching or coarse and fine feed conversion. The weighed mixture is discharged through the valve to the heated reaction tank, stirred, and then pumped into the dissolver to enter the dissolving process.
The loading system is composed of weighing module, weighing transmitter, Siemens S7-200PLC, rotor pump, frequency converter, cut-off switch, proximity switch and upper industrial control computer (IPC) and other components. The upper industrial control computer (IPC) is connected with PLC through PC/PPI communication cable to exchange data in real time. To complete the display, recording, monitoring and alarm functions of the field parameters, the weighing module supported on the weighing bucket converts the electrical signal representing the weight into 4~20mA standard signal after the weighing transmitter, and then is collected by the PLC A/D module. This signal will be used as the basis for the vibration feeder to ration the feed and count the actual accumulated weight.
The feeding system is set to two control modes, namely manual control and automatic control, and the automatic control mode includes single step and continuous mode. Manual operation is mainly used in system debugging, maintenance or when the PLC fails. The automatic control mode is the normal working mode of the Batching system. During the automatic operation, according to the production requirements, the ratio of 4 kinds of materials is input through the keyboard in the upper computer, and the upper computer calculates the fast matching target value and standard setting value of various materials. When the fast batching target value of No. 1 material is less than the standard setting value, the PLC issues high-speed instructions to make the 1# feeding work at high frequency. The No. 1 material quickly falls into the weighing bucket to improve the feeding efficiency, and the net weight of the No. 1 material is displayed on the upper computer in real time. When the material reaches the set fast batching target value, the inverter switches to the smaller conveying frequency and delivers the material at a slow speed. When the weighing value is less than the standard set value of No. 1 material (if the difference is outside the tolerance range), PLC will automatically start the point to correct, and No. 1 material will continue to batching to ensure the batching accuracy; If the difference is within the tolerance range, the PLC will output a stop signal, the feed stops running, and the 1# feed ends. Feed into 2# at the same time. The batching process for No. 2 to No. 4 materials is the same as the batching process for No. 1 materials, until the four materials are finished, the batching cycle of a batch is completed.