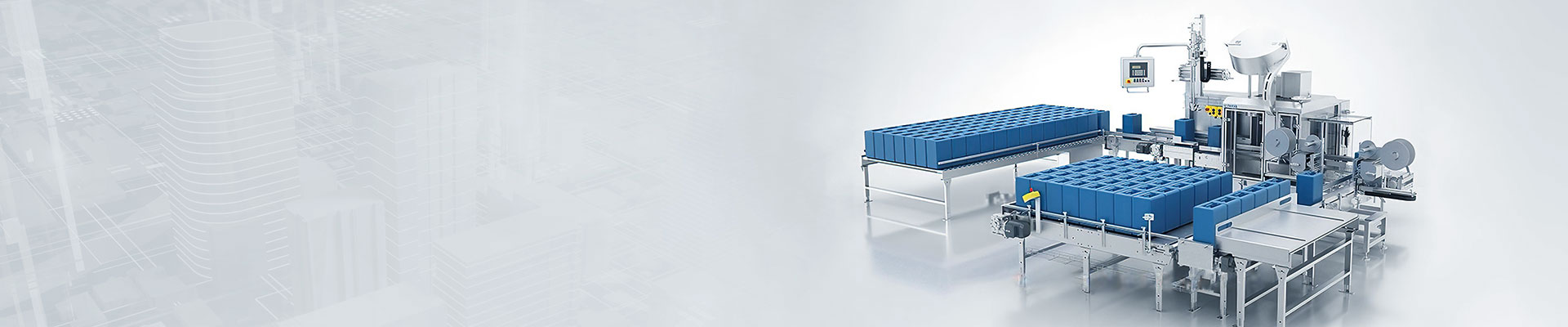
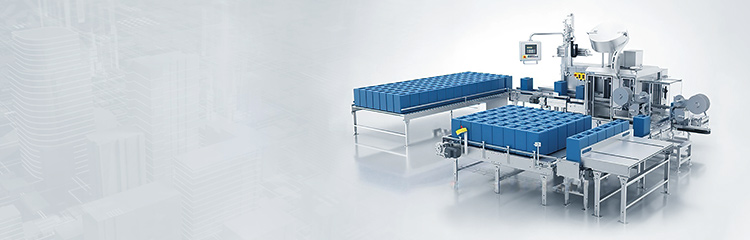
The automatic filling machine consists of a two-level computer control network composed of programmable controller and electronic scale, which is connected to the weighing instrument, control computer, PLC, inverter and other equipment with high intelligence and fast processing speed through the field bus. PLC is mainly responsible for the automatic filling machine fault detection, display and alarm, and at the same time to the inverter output signal, inverter to complete the adjustment point electronic scale speed role.

The automatic Filling machine consists of a two-level computer control network composed of programmable controller and Electronic scale, which is connected to the weighing instrument, control computer, PLC, inverter and other equipment with high intelligence and fast processing speed through the field bus. The PLC mainly undertakes the fault detection, display and alarm of the filling machine, and outputs the signal to the inverter at the same time, and the inverter completes the role of adjusting the speed of the electronic scale at the point. The electronic scale weighs the instantaneous flow rate, and the upper computer gives the set flow rate. There is some deviation between the two in real-time measurement. Automatic filling machine adopts the most widely used PID regulation in industrial control for actual flow control, according to the flow deviation, the use of proportion, integral, differential calculation of the control amount, Filling system through the frequency converter to adjust the speed of electronic scale, adjust the quantity, so that it is equal to the set value, complete the automatic filling process.
Automatic filling machine adopts three-stage speed feeding mode, raw materials are fed in turn, a frequency converter is used to control the rotor pump, and PLC controls the frequency converter through different combinations of the output switching quantity to achieve fast feeding, slow feeding and fine feeding. Fast feeding at the beginning of weighing and slow feeding when the given value of fast feeding prediction is reached; When the given value of slow feed prediction is reached, the fine feed starts; Stop feeding when the total feed weight reaches "target weight - pipe weight - allowable error", and the pipe weight is the material weight remaining in the pipe that will continue to flow into the weighing tank after the motor stops rotating. The percentage of the target weight is selected as the optimal value in the actual test, and the target weight and allowable error are set by the touch screen.