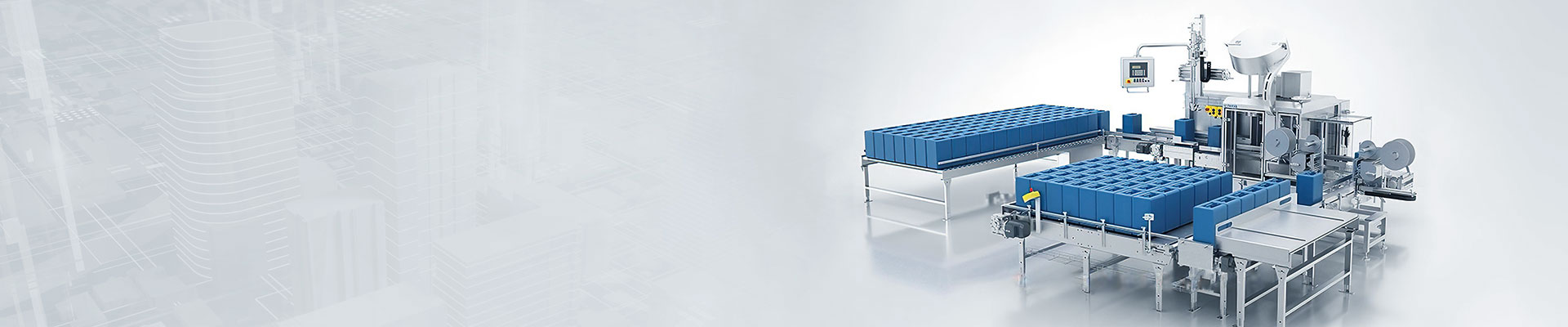
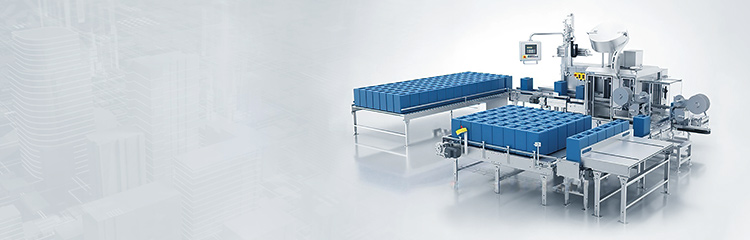
The automatic filling machine is based on Kingview software, the monitoring interface of the filling production line, the PLC system is provided to realize the connection with the field control, and the complete human-machine dialogue state is realized. The PLC control system and the operation station can be communicated and set quickly through the RS-422/485 interface, and the basic control unit of the PLC can be used to operate the start and stop.

Automatic Filling machine for liquid material automatic weighing and filling equipment, will come from the front of the material, according to the set weight automatically into the empty bucket; Can be used in a variety of trade approved drums or containers, and the system can be used in wet, dangerous or other adverse environments. It is mainly composed of spray gun device, system control box, electronic platform scale, mechanical structure, conveying raceway, etc., compact and reasonable structure, stable and reliable work, easy installation and operation, and can be adjusted according to various sites and production capacity to meet user requirements; The system has a high degree of automation, which can avoid material overflow and prevent the environmental pollution of the material itself to the greatest extent, so as to effectively protect the operator.
The automatic filling machine adopts Siemens PLCS7-300 system, DELL industrial computer WINXP operating system, and uses a programmable controller to design process control such as filling scanning and filling management. On the basis of relevant database information service, the monitoring interface of filling production line is installed based on Kingview software. The PLC system provided by Kingview is used to realize the connection with the field control. The filling machine adopts the intelligent multi-function panel, the man-machine operation interface is simple and suitable, the configuration is suitable, the modification is convenient, and the complete man-machine dialogue is realized. The PLC control system and the operation station can be quickly communicated and set through the RS-422/485 interface, and the PLC can be started and stopped by using its own basic control unit.