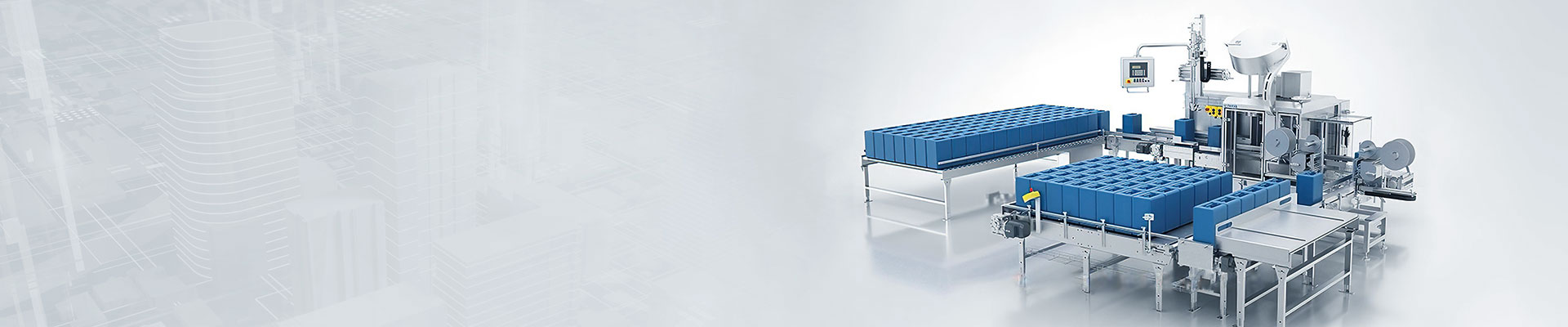
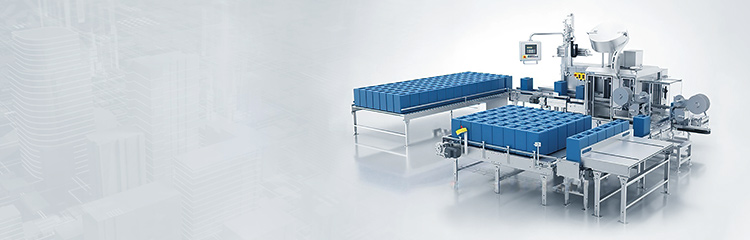
The weight filling production line mainly adopts the weight quantitative method, and realizes the liquid quantitative filling by collecting the data of the weight module. The filling quantity is measured and displayed in real time. The weighing module and weighing instrument are adopted. The intermediate relay is used as the conversion to control the solenoid valve and pump. Calculate the actual standard filling value according to the weight of each empty drum, and calculate the saved value of the converted value to ensure the accuracy of adjusting the blanking error.

The automatic Filling machine uses the characteristics of high measurement accuracy of the Electronic scale, the weighing sensor and the weighing control instrument are connected with the data line, and the pressure signal of the electronic scale is continuously transmitted to the control instrument during the measurement process, the measurement accuracy is not affected by the density, temperature, impurities, bubbles and other factors, and the liquid can also be accurately measured with mixed semi-solid. It is composed of a filling head, a weighing conveyor and a positioning device, and can be combined with bottle Sorting machine, capping machine and labeling machine to form a complete filling line, with automatic quantification, automatic filling, automatic error correction, counting, clearing and other functions.
The metering filling machine is used for data acquisition, processing and control. The touch screen of embedded MCGS configuration software can realize real-time data display, set quantitative value, fast forward amount, medium forward amount, slow forward amount and other parameters to start the system. The Filling system converts the material weight into the corresponding voltage signal through the weighing module and transmits it to the weighing instrument. The weighing instrument completes the amplification, filtering, A/D conversion and processing of the signal. The processed data is transmitted to the touch screen for real-time display, and the actuator is driven by the output control of the three-level feeding algorithm to control the closing of the valve, thus changing the feeding speed. When the mass of the material in the weighing bucket and the amount of air drop reach the quantitative value, the valve of the feeding port is closed. Weighing system should include weighing module, weighing instrument and touch screen. The weighing instrument includes single-chip microcomputer, A/D conversion module, signal conditioning circuit, input and output of switching quantity, communication circuit, etc. DI input is the input signal of starting, stopping and other switching quantity. DO output is the output signal of driving control valve closing, opening and buzzer alarm.