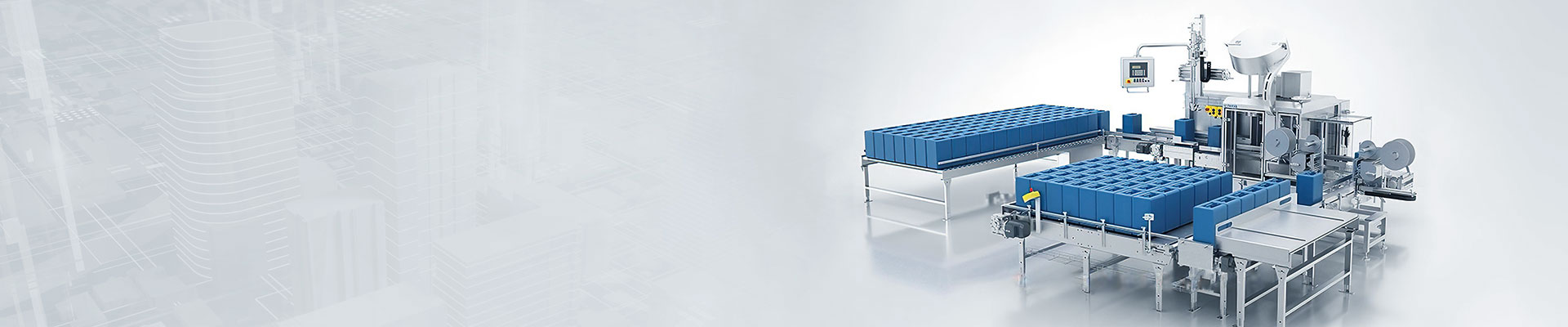
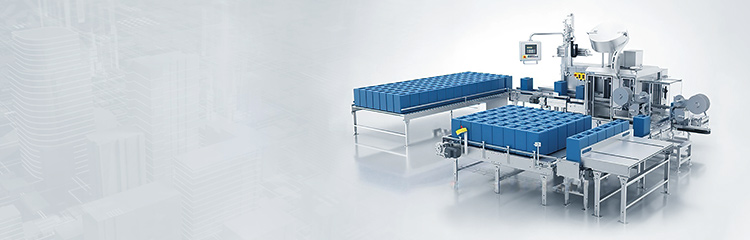
After the filling barrel is filled by the pneumatic piston valve in the weighing system, the weighing module will detect the filling target value in the weighing line after the filling is completed, and the information will be quickly transmitted to the terminal computer.

The weighing and Filling machine completes the collection of the target value in the filling, and transmits the pressure value to the next set in the form of A signal. A/D conversion circuit is mainly responsible for converting the signal transmitted from the upper level into a signal that can be effectively processed by the computer. The man-machine exchange circuit is mainly responsible for parameter setting and monitoring the operation status of the control system. And eliminate the interference between the actuator of the system and the hardware circuit; The output signal amplifier circuit is mainly responsible for the appropriate amplification of the output signal in the system, so as to facilitate the actuator to carry out the next step.
The automatic filling machine is realized by the stepper motor to control the movement of the filling valve of the grating. The vibration of the progressive motor adopts the mode of broadband pulse modulation. The direction signal (DIR) and the pulse signal (CLK) are respectively the level triggered to control the winding direction of the stepper motor and control the moving direction of the stepper motor. The pulse signal must be at least 10us in advance in the sequence. The pulse signal is triggered by the falling edge. The pulse signal controls the rotation of the stepper motor around the machine, and each pulse corresponds to an Angle of rotation of the machine, which is equivalent to controlling the corresponding distance of the stepper motor to control the moving track of the filling gun valve for filling control.