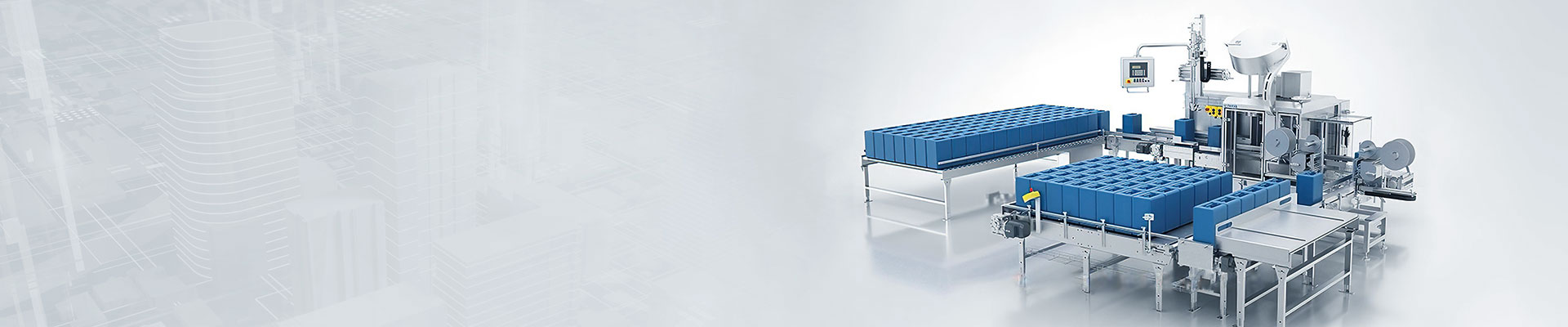
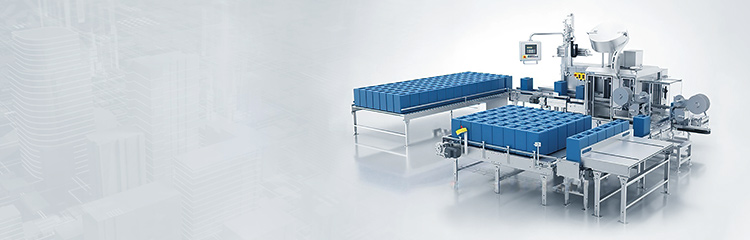
When the barrel reaches the filling position, the liquid filling machine senses the filling barrel near the switch, transmits the induction signal to the PLC, the PLC controls the conveying motor to stop, the lifting cylinder begins to rise under the control of the PLC, and drives the roller arm structure to rise to the maximum position of the cylinder stroke, the lifting cylinder stops rising, and the synchronous motor starts to drive the roller arm to move. The filling barrel can be rotated under the drive of the roller arm.

The working principle of the weighing Filling machine is to use the characteristics of high measurement accuracy of the Electronic scale, the weighing sensor and the weighing control instrument are connected with the data line, and the pressure signal of the electronic scale is continuously transmitted to the control instrument during the measurement process, and the control instrument controls the pump and closes the pneumatic valve when the preset quantitative weight is reached. Under the guidance of the centring device, the feeding port of the filling valve is tightly pressed to form a seal, which is automatically injected into the bottle along the bottle wall and replaced back into the liquid storage cylinder through the return pipe. When the object rises to a certain height and the return pipe mouth is closed, the material reaches the specified weight and automatically stops the downstream object. Then the liquid valve and the gas valve are closed, and the pressure gas at the bottleneck is discharged to prevent the gas object from gushing when the glass bottle is falling, so that the entire filling process is completed.
When the barrel reaches the filling position, the Liquid filling machine senses the filling barrel near the switch, transmits the induction signal to the PLC, the PLC controls the conveying motor to stop, the lifting cylinder begins to rise under the control of the PLC, and drives the roller arm structure to rise to the maximum position of the cylinder stroke, the lifting cylinder stops rising, and the synchronous motor starts to drive the roller arm to move. The filling barrel can be rotated under the drive of the roller arm. The photoelectric sensor above the barrel mouth and the filling head are on the rotating trajectory circle of the barrel mouth, and the filling barrel rotates to the right below the photoelectric sensor. When the photoelectric sensor senses the edge of the filling barrel mouth, the signal is transmitted to the PLC, and the PLC will stop the synchronous motor movement according to the signal of the photoelectric sensor. When the barrel mouth is detected, the cap suction device rotates to the top of the filling barrel mouth under the drive of the cylinder, draws the lid of the filling barrel, and returns to the original position after the cap suction action is completed. When the barrel cover is absorbed, the quantitative filling process begins. The PLC controls the rodless cylinder to drive the filling gun into the filling barrel for liquid filling. The weighing module can sense the change of weight in the filling barrel to realize the quantitative filling of liquid. After the liquid filling is completed, the instrument will transmit the filling end signal to the PLC, and the PLC will finish the quantitative filling process according to this signal. The PLC control rodless cylinder drives the filling gun to the initial position, and the cap suction device rotates to just above the position of the mouth of the filling barrel and places the cap on the mouth of the filling barrel. The conveying motor starts and transfers the filled filling drum to the designated position.