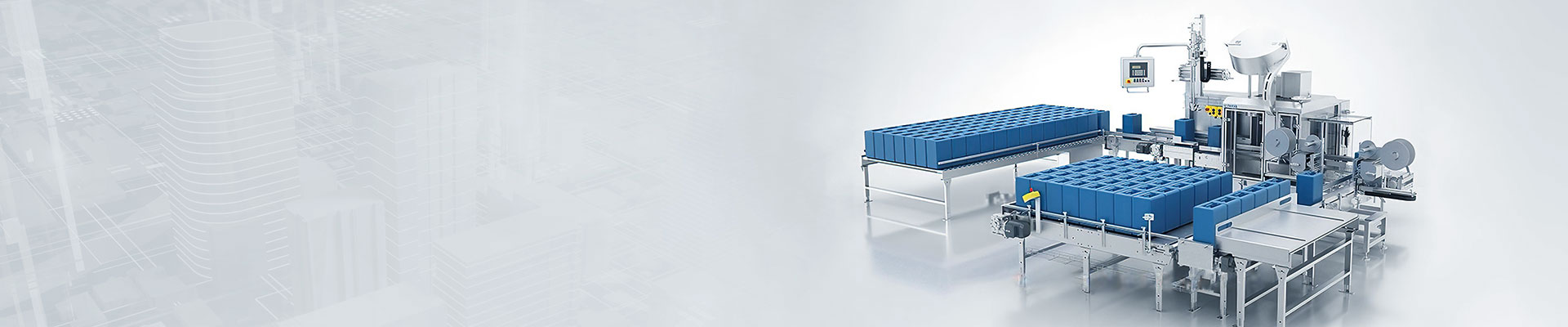
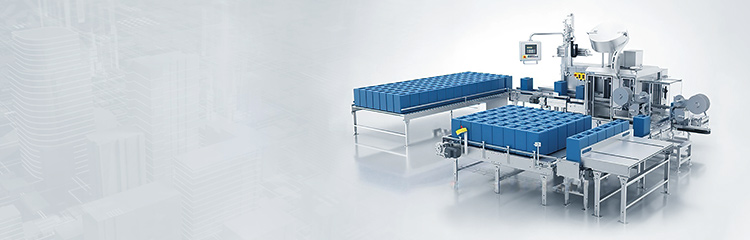
The explosion-proof filling line uses position servo control to precisely control the stroke of the piston cylinder, which also achieves the purpose of accurately controlling the filling volume. Collect the liquid viscosity, temperature and pressure, and realize the stroke compensation of the piston cylinder through a certain compensation algorithm. DSP receives the position command signal sent by the PLC, and superposes the quantitative weight given by the PLC as the total given quantity. After the quantitative signal is adjusted by the composite feedforward controller, the speed command signal is formed.

Weighing filling machine integrated application of embedded technology, smart card technology, network communication technology, industrial Ethernet technology, artificial intelligence control technology, distributed database technology and the whole network distribution control technology, to achieve the filling control and hierarchical management, the use of position servo control to precisely control the stroke of the piston cylinder, but also to achieve the purpose of accurate control of the filling volume. Collect liquid viscosity, temperature and pressure, and realize stroke compensation of piston cylinder through certain compensation algorithm. DSP receives position instruction signal sent by PLC, and superposition quantitative weight and compensatory weight given by PLC as the total quantitative set. Quantitative signal is adjusted by composite feedforward controller to form speed instruction signal. The deviation signal after comparing the speed command signal with the speed feedback signal is adjusted by the speed ring proportional integration controller to generate the current command signal. After vector transformation in the current ring, the torque current is transmitted by SPWM to control the operation of the AC servo motor. The filling process is controlled by the number of pulses generated by the rotary encoder per revolution.