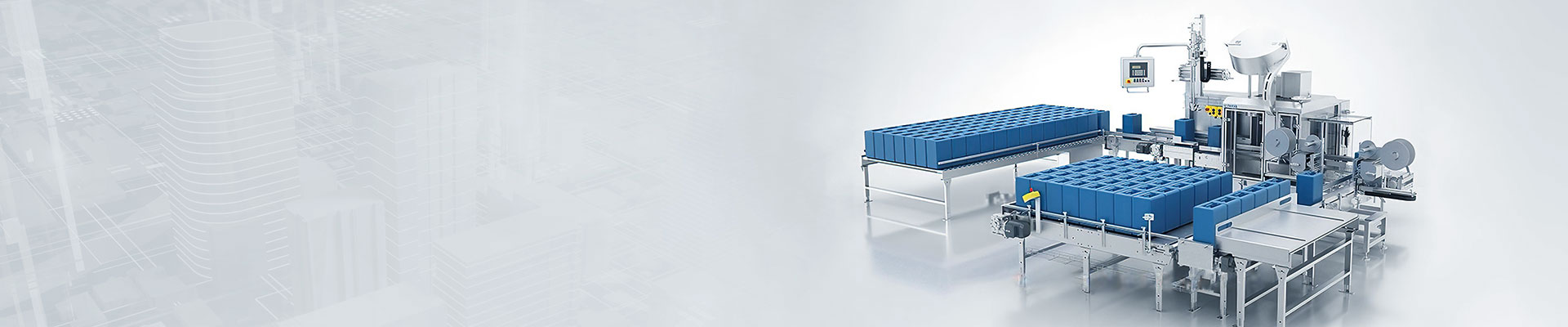
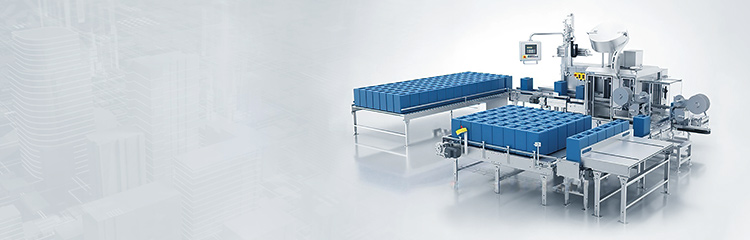
Each discharge port of the epoxy resin filling machine has a set of independent weighing control unit, which detects the filling weight through the connected weighing sensor, and completes the whole control process of opening and closing of the discharge gate, opening and stopping of the cylinder filling gun and capping. Each control unit is connected to the communication bus, but does not affect each other.

The automatic Filling machine has a set of independent weighing control unit for each discharge port, which detects the filling weight through the connected weighing sensor, and completes the whole control process such as opening and closing of the discharge gate, opening and stopping of the cylinder filling gun and capping. Each control unit is connected to the communication bus, but does not affect each other. The communication bus of the control unit of the filling machine is managed by the weighing control system unit and transmitted to the photoelectric coupling interface in real time to realize the communication between the rotating part of the filling machine and the static part of the control equipment. The position of each discharge port is detected by the photoelectric encoder installed on the vertical shaft of the filling machine. The signal is converted into a communication signal at the node of the weighing module and sent to the control unit of each discharge port in the rotating part through the weighing module, which is used to coordinate and control the automatic peeling gate and the correct position of the unloading action during the filling process. The metering module node also sends the alarm information from the weighing control unit to the master node, and from the master node to the keyboard console for display. At the same time, it also converts the output setting signal of the filling machine into an analog voltage signal, and controls the frequency converter to adjust the speed of the filling machine.
A feature of the weighing control unit is that it not only displays the filling weight in real time, but also displays the corresponding code along with the working process of each discharge port, and displays the code "P" when all the discharge ports are ready; When the filling barrel is inserted and detected by the control unit, the display becomes "b". When the discharge port is rotated to the preset automatic peeling position, the additional weight such as the filling drum itself and ash accumulation on the weighing platform is removed, the code "C" is displayed, and the weight display changes to "0". Then the discharge gate is fully opened and the discharge cylinder starts, this stage is rapid filling and the code "U" is displayed. If the filling rate is lower than the specified weight at this time, the control unit considers that the filling barrel does not fit correctly with the discharge port, stops working, and automatically loads the filling barrel. When the weight of the filling drum reaches the predetermined parameter value (75% of the rated weight of the filling drum), the discharge gate is partially opened, the filling speed of the filling drum is slowed down, and the code "L" is displayed. When the filling weight reaches the rated value, the discharge gate is completely closed, the discharge cylinder stops running, and the code "F" is displayed. The control unit stores the weighing results for subsequent filling control error correction. When the discharge port reaches the conveyor belt position, the filled drum is released and the code "n" is displayed, completing a filling process.