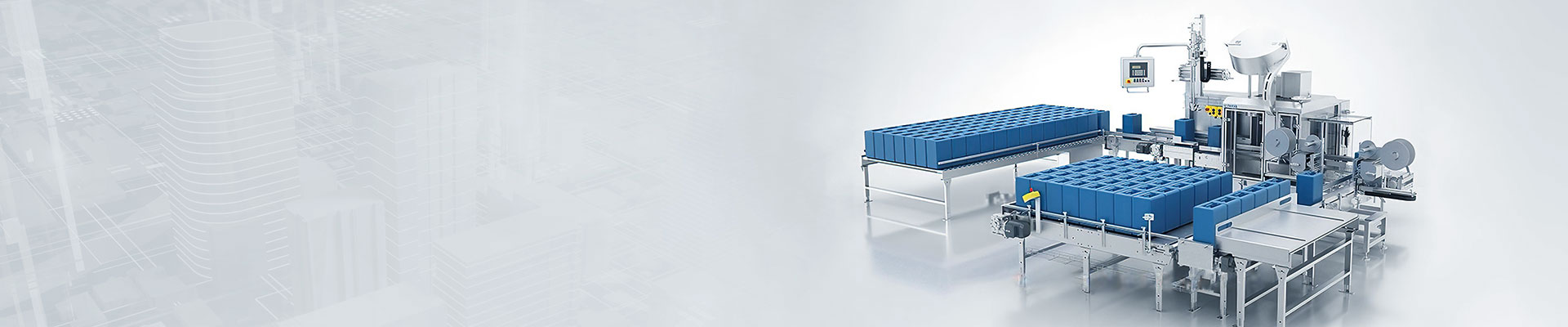
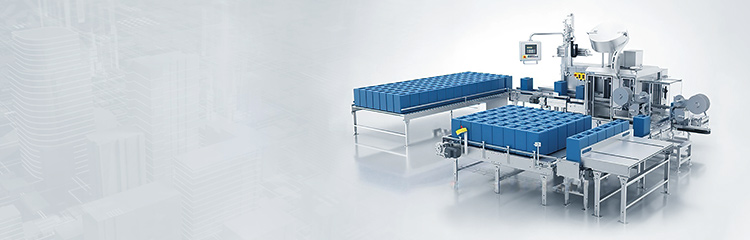
RFID weighing system is an advanced wireless weighing technology. RFID weighing system can make many management realize wireless methods, and more commercial enterprises will implement the work of coding items one after another. In order to improve the operation efficiency, we should try not to change the current logistics storage mode, so we should use pallets as carriers, and adopting pallet identification can make storage management more convenient.

RFID Weighing system uses wireless network and bar code technology, based on the basis of wireless network and RFID selection, as well as management implementation strategies, RFID integrated management system based on automatic weighing is mainly composed of order management system, automatic scheduling system, production and packaging system, warehouse management subsystem, data synchronization and system integration modules. The system uses NET as the software development platform, and the development environment is divided into two parts: PC terminal and RFID acquisition terminal (handheld), the latter of which is an intelligent mobile device, using NET simplified version framework to achieve embedded development. Weighing system adopts SQLSERVER series database platform, design database structure according to the realization objectives and functional requirements, use SQLSERVER replication mechanism to achieve distributed database, and combined with the practical experience of nonwovens production and management of RFID database management and optimization strategy.
RFID weighing systems can be broken down into: Basic information management, customer order management, production plan management, material demand management, material procurement warehousing, material production receipt and release, automatic weighing and labeling management, product inspection information management, product RFID warehousing and logistics management, product outbound RFID management, product inventory RFID management, product sales returns RFID management. The barcode coding rules adopt the international logistics general code system ODE128, and the code number is the unique identity code of this product, such as: 0120100423A0001. It means production line (01), date (20100423), shift (A), number of production pieces (0001). Among them, the frequency is defined as A morning shift, B middle shift, C night shift; The item number is self-increasing. For example, 0001 represents the first volume of the morning shift of line 01.
1 Product quality traceability and anti-counterfeiting function
The system automatically records the product's production number, production date, production line, material batch number and other links of information, to establish a perfect product file. If there is a problem with a product, only need to enter the product's unique identity RFID, the system automatically queries the product's production number, production date, inspection number, inspection date, warehousing number, warehousing date, warehousing number, warehousing number, warehousing date, shipping license plate number and the batch number of raw materials used. Since each product has its own unique identity RFID, if it is not a factory product, just scan the product RFID, the system automatically alarms "This product is not a factory product".
2 Material cost control
Through each type of product bill of materials, the product production plan is decomposed into the material plan, the raw and auxiliary material allowance can be reasonably calculated, and the raw and auxiliary material amount of each batch of products can be controlled.
3 Automatic output statistics, flexible production scheduling
When the system automatically weighs each batch, it automatically records the operator, machine number and production date, can easily count the output of employees, and can investigate the relevant responsible personnel who produce defective products. Authorized management personnel can query the sales orders, production planning orders, batches, etc. of the entire company in real time, and make reasonable scheduling of production plans according to specific circumstances.
4 Advance warning function
Order production has an early warning function, always remind the production department, how long is the delivery date of an order, prevent the occurrence of the phenomenon that has not yet been produced, and improve the company's image. The export products are also weighed to remind employees whether they exceed the theoretical weight, and the excess weight is assessed every month, which is convenient to improve the enthusiasm and seriousness of employees.
Due to the information sharing of all departments, all departments can know their work tasks in advance and make preparations in advance. For example, the warehouse department can inquire about the products to be completed, arrange the warehouse location by gram weight, color or customer in advance, and immediately move the products that have been produced into the warehouse, which will not cause disorderly storage.
5. Improve production efficiency
In the production line, workers only need to put the product on the Electronic scale, the system automatically prints the product identification RFID, and records the product production information at the same time to ensure the accuracy of the product information, no need to manually record information, improve production efficiency and enhance the company image.
6 Easy to operate, reduce errors
Warehousing operation adopts scanning RFID method to tally goods, and automatically prints out the warehouse list, and the physical object is checked again with the warehouse list when loading, to prevent the occurrence of wrong goods. In and out of the warehouse operation, inventory, transfer and other operations using RFID scanning mode, fast speed, accurate data. RFID is also used to manage defective products and raw and auxiliary materials, which can query the inventory of defective products and raw and auxiliary materials in real time.
7 Information sharing and query
From product sales orders to production materials, product weighing, warehousing and warehousing are all operated by scanning RFID, ensuring the real-time and correctness of the data. As long as the information is input in one place, other relevant departments can share it, ensuring the consistency of the data, and the management can effectively carry out online management.