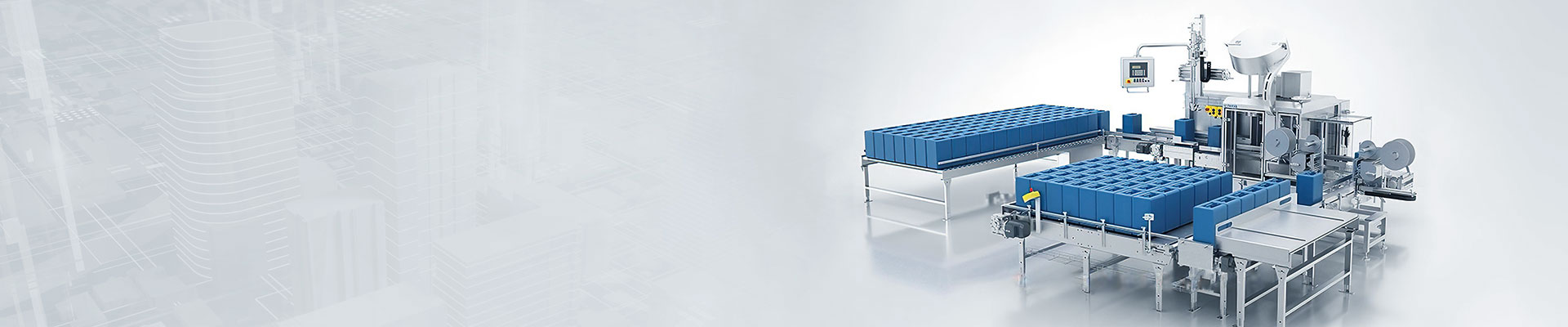
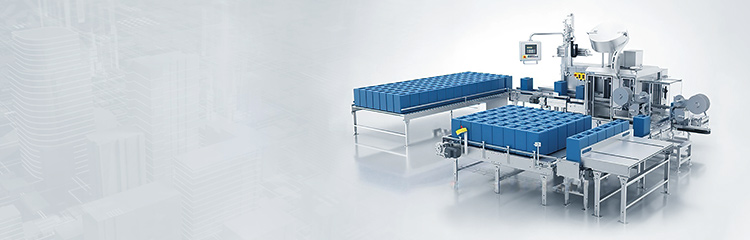
The screw weighing system can be divided into instruments and touch screen control, the material supply uses the feed screw, the screw uses the inverter to drive through the frequency conversion motor, according to the current weight and target weight to control the motor running speed and start and stop. When the weight reaches the allowable error of the target weight, the screw stops feeding. The target weight for weighing can be a task call from the host computer via Profibus-DP or a direct input weight from the touch screen.

The feeding system can be divided into instruments and touch screen control, and is fed by a number of silos. It is used for professional production of weighing and batching equipment for continuous conveying, metering and automatic batching of powder and granular materials. It is composed of hopper measuring scale, feed screw conveyor, discharge screw, computer control system, small material (trace) delivery device, etc. The spiral Weighing system transmits the raw materials to the measuring scale in the set order by the conveyor screw of the raw material warehouse. Each raw material is transported in turn according to the weight set in the automatic control system. After the weight of the material reaches, the weighing instrument directly controls the start and stop of the material spiral, and then starts the conveying spiral of the second material. This sequential transmission, to a large extent to ensure the accuracy of measurement. After the weight of the raw material is measured, all the raw materials are transported to the bucket elevator by the discharge spiral of the measurement, and the bucket elevator is started at the same time, and the raw materials are sent to the waiting mixing bin located above the main engine.
The material supply in the weighing system uses the feed screw, which uses the frequency converter to drive through the variable frequency motor, and controls the running speed and start and stop of the motor according to the current weight and target weight. When the weight reaches the allowable error of the target weight, the screw stops feeding. The target weight for weighing can be a task call from the host computer via Profibus-DP or a direct input weight from the touch screen.
The hardware configuration of the weighing system needs to accept the weighing data from 4 stations on the premise of completing the control function, needs to communicate with the touch screen, needs to communicate with the host computer PLC, and needs to control the frequency converter for multi-stage speed. According to the basic use of Siemens series controller in the production line, it is decided to use S7_300 series PLC. Communication methods include MPI, Profibus-DP and Ethernet. Considering various factors, we decide to use S7-300-2DP, X1 is MPI communication interface to communicate with touch screen, X2 bit DP interface to communicate with host computer Profibus-DP. The analog channel of the CPU can accept the weighing information from the weighing module.