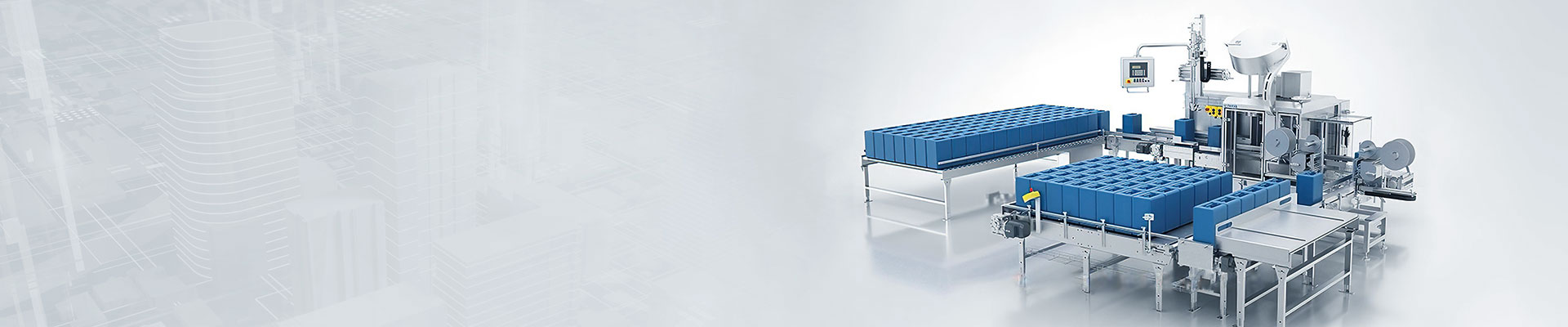
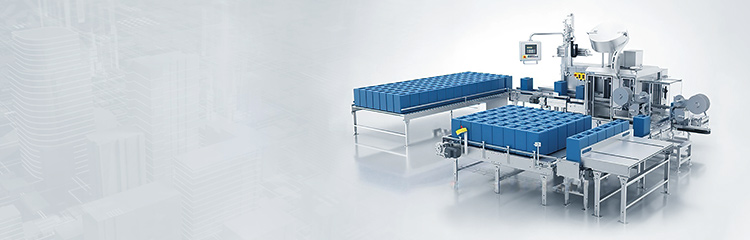
By compensating the junction box (adjusting the output parameters of each weighing sensor to balance the output of each weighing sensor and eliminate the load bias error of the electronic scale), the crane scale system sends the signal of 1~18mV to the batching controller and displays its weight data on the spot, and transfers the weight signal to the wireless data collection station in the form of 4~20mA. When lifting scrap steel and molten iron, the weight data can be accurately measured on the skytrain and sent to the receiving system composed of a wireless central receiving station and a scrap water weight monitoring computer through wireless transmission.

In steelmaking production, the loading of scrap steel and molten iron is to lift the scrap tank and molten iron furnace cylinder through the crane hook, and pour the scrap steel and molten iron into the steelmaking furnace through the coordination of the auxiliary hook. Due to the harsh working environment, weighing needs to be completed in the air, so the weight collection and weight data transmission of scrap steel and hot metal once became a problem. After careful study, multiple pressure Weighing modules are used to take out the weight signal, and the signal of 1~18mV is sent to the proportioning controller and the weight data is displayed locally by compensating the junction box (adjusting the output parameters of each weighing sensor to balance the output of each weighing sensor and eliminate the load bias error of the Electronic scale). At the same time, the weight signal is transmitted to the wireless data acquisition station in the form of 4~20mA. In this way, when lifting scrap steel and molten iron, the weight data can be accurately measured on the sky car and sent to the receiving system composed of a wireless central receiving station and a scrap water weight monitoring computer through wireless transmission.
The maximum communication radius of this system is 1.5~2 km, and the frequency is 2.4GHz. The collection method is wireless call answering type, that is, one central station can recycle multiple stations. After receiving the call command of the ground central station on the same day, the sampling station of the vehicle immediately sends the collected weighing signal to the ground central station. The central station processes the received signal to the computer. Data display, storage, backup printing, database establishment and other work are completed by the collection program.
Electrical control instructions Electrical control instructions computer and electrical PLC constitute an independent two-level monitoring system, the reason why this part is independent is mainly to take into account that some electrical operations are emergency handling operations in emergency situations, directly related to the safety of the system, independent design can ensure the reliability of the system.
① Dual hot standby instrument monitoring control part
Use two mutual hot standby network servers, the host through the connected network, monitor the work of the instrument PLC, the slave machine always maintain the monitoring state, monitor the work of the host, once the host is found abnormal, the slave machine will replace the host in a short time, real-time monitoring and save historical data, once the host restarts, and the slave machine detects the presence of the host. The lost historical data is automatically copied to the host, and the slave is monitored again. In this way, even if an accident occurs, the system can keep a relatively complete database. Dual-system hot backup prevents data loss caused by various factors such as onsite and hardware, improves system reliability, and facilitates system maintenance.
② Monitoring screen technology
The monitoring computer is the network server of the instrument part, on the one hand, it directly reads the analog values of the system from the instrument PLC through the communication adapter (MPI card), on the other hand, it also reads the weight of scrap steel and molten iron from the scrap and molten iron weight monitoring computer through the network. In this way, the bulk material monitoring computer, gas recovery monitoring computer and workshop production scheduling computer on the NT network share all parts of the data from this server in real time, and display it in their respective monitoring screens; Process sub-diagram monitoring computer also real-time display of oxygen, nitrogen, cooling water pressure and flow, real-time display of cooling water, population temperature and molten steel temperature, the operator can through the industrial keyboard in this computer (with the instrument PLC communication, through the PLC AO module to the valve opening set value transmitted to the regulating instrument, The adjusting instrument compares the setting value with the feedback value of the valve opening, adjusts the opening of the valve) to adjust the nitrogen and oxygen valve opening, and then adjusts the pressure and flow of nitrogen and oxygen.
③ Temperature measurement of molten steel
The temperature of molten steel is a very important index for furnace shutdown, which needs to be monitored in the computer system of the control room. After the temperature signal of molten steel is extracted from the furnace by the thermocouple probe, it is directly displayed on the display screen of the digital tube of molten steel temperature on the spot, and the output of 4~20mA is generated and transmitted to the analog quantity input module of the instrument PLC, and then the process sub-diagram monitoring computer reads the temperature of molten steel from the instrument PLC through the communication adapter and displays it.
④ Bulk material measurement For the weighing of bulk materials, the weight signal is taken out through the four pressure weighing modules at the corners of the silo, and sent to the batching controller (removing the weight of the silo itself) after compensation by the compensation junction box. At the same time, the transmission output of 4~20mA is sent to the AI module of the instrument PLC, and the weight value is read out by the process sub-diagram monitoring computer. This data is shared through the NT bulk monitoring computer, so that the weight value of the bulk in each bin is displayed in real time.