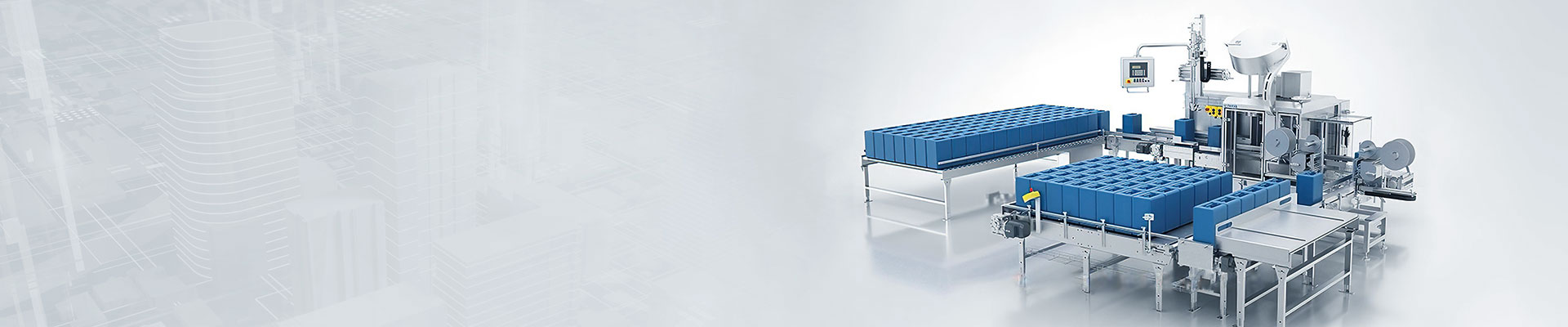
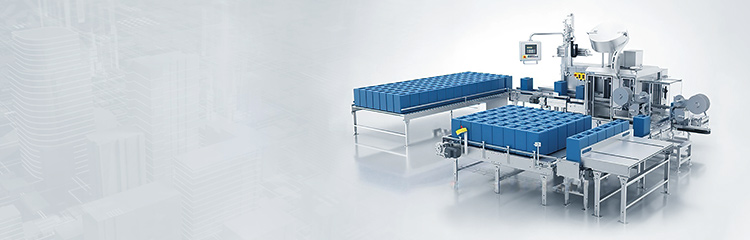
The liquid filling machine is mainly used to collect the set value of the filling amount and process the pulse signal of the weighing module. The touch screen driving relay drives the frequency converter to control the motor and the centrifugal pump to transport materials. The weight is obtained through the weighing module to control the actual discharged liquid amount, and the motor operation is controlled according to the difference between the actual filling amount and the set value, so as to accurately control the filling amount according to the actual needs.

The liquid Filling machine adopts two-stage large and small material adjustable filling mode, and provides a unique anti-drip device to avoid material dropping on the barrel and weighing platform, affecting the packaging and drum; Can choose two filling modes of net weight and gross weight to meet different filling needs of coatings; The target quantity is freely set, and the filling is suitable for various weight ranges. The control system is composed of PLC, touch screen, filling actuator and testing element. The computer downloads the program online through Ethernet PLC and monitors the operation of the equipment. The touch screen is used as the man-machine interface, combined with the PANTHER weighing instrument of Meteli-Toledo, through the Modbus485 communication protocol to communicate with the PLC, always display the operating status of the device, and start, stop and set various operating parameters and other operations. The filling actuator is responsible for executing the PLC instructions and executing the corresponding actions in detail. The detection element sends the status and parameters of the equipment into the PLC, which can easily achieve high-speed data communication with the relevant PLC(or C) Weighing system to meet the needs of various users for filling.
Filling system through the weight induction and input pulse frequency speed to achieve, when the pulse frequency decreases, the speed of the stepper motor will decrease; As the frequency increases, the speed increases. In order to achieve the purpose of measuring size can be adjusted to improve the measurement accuracy, the speed of the screw can be adjusted to position accurate positioning, the stepper motor is used to control the speed and revolution of the screw, which not only simplifies the mechanical structure, but also makes the control very convenient. In the case of no load, the speed and stop position of the stepper motor only depend on the frequency and number of pulses of the pulse signal, and are not affected by load changes. Through the data acquisition and processing of the on-site filling machine, animation display, alarm processing and flow control are used. Real-time curve, historical curve and report output. In order to realize the above monitoring requirements, the dynamic filling process is simulated by the filling effect and the flow attribute setting with fast flow in the monitoring interface design. The manual/automatic selection, start, stop, emergency stop and manual opening of the pump solenoid valve are realized by adding standard buttons, and the filling quality is displayed in real time by setting the display output attribute of the label. The configuration monitoring screen such as the setting of the number of filling bottles and the display of the current number of filling barrels can complete the monitoring of the operating status of the filling system.