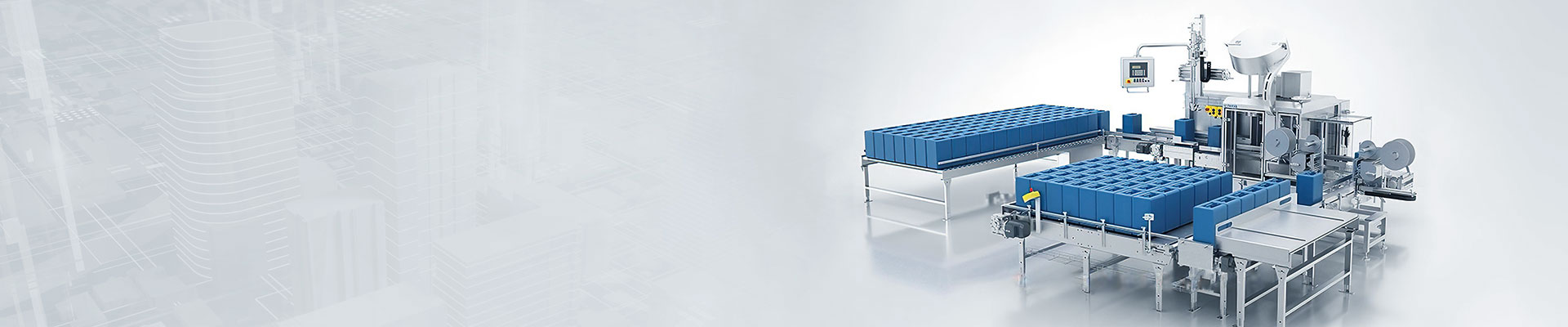
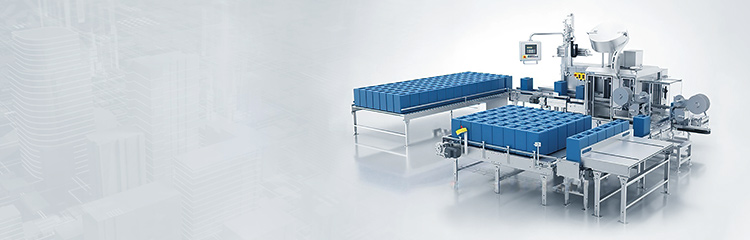
The feeding system is mainly composed of storage bin, coarse feeding mechanism, fine feeding mechanism, weighing cylinder, weighing sensor, filling mechanism, PLC control system and pneumatic system. When the feeder is working, the coarse and fine feeding mechanism is fed at the same time. According to the output signal of the weighing module, the PLC control system controls it respectively according to the set value of the weighing. When the weighing module reaches a certain value, the coarse feeding mechanism stops feeding, and the fine feeding mechanism continues to feed until the system set value is reached.

Automatic Feeding machine control system is mainly used in the feeding system of hopper dryer, the use of weighing instrument as the central processor, the use of automatic control technology to achieve the function, when the air pump of the feeding machine rotates, the air pump produces negative pressure to form a vacuum airflow, the material is sucked by the suction nozzle, the formation of gas flow, through the suction tube to the feeding machine bin. The filter completely separates the material from the air. When the material is filled with the bin, the controller automatically cuts off the power, the vacuum Feeder stops working, and the bin door automatically opens, and the material falls into the hopper of the equipment. At the same time, compressed air automatically cleans the filter through a pulsed backblow valve. When the time is asked or the material level sensor sends a feeding signal, the feeding machine will be automatically started. The high vacuum produced by the vacuum air pump, the vacuum powder feeder of the air pump is to use the high vacuum generated by the rotation of the air pump to achieve the conveying of materials. So that the material to be transported to eliminate the stratification phenomenon, to ensure the uniformity of the composition of the mixed material, is spinning machinery, tablet press, capsule Filling machine, dry granulator, packaging machine, crusher, vibrating screen and other mechanical automatic feeding equipment of choice. According to the needs of the feeding process, the feeding machine control system sets the parameter values of the conveying, discharging, full and empty materials of the two production lines, and can also load the previous process parameter values of the system. The basic control requirements of the feeding machine are: Use a motor to control two production lines, to be able to detect the full state, and show the conveying, discharging, full time, time error 0.1S, with anti-interference ability.
The feeding system is a complete set of automatic equipment which realizes dynamic weighing and batching control through electrical control management and visual man-machine software configuration. The electrical control part of the system adopts Siemens PLC, which is programmed according to the production requirements. The software adopts the human configuration, according to the process requirements, through the monitoring system and PLC program to load the material to the weighing hopper weight, flow control, so as to achieve accurate measurement and batching. It is mainly composed of storage bin, coarse feeding mechanism, fine feeding mechanism, weighing cylinder, weighing sensor, filling mechanism, PLC control system and pneumatic system. When the feeder is working, the coarse and fine feeding mechanism is fed at the same time. According to the output signal of the weighing module, the PLC control system controls it respectively according to the set value of the weighing. When the weighing module reaches a certain value, the coarse feeding mechanism stops feeding, and the feeding mechanism continues to feed until it reaches the set value of the system. The filling mechanism turns over the weighing cylinder and pours the material into the receiving cup at the qualified station to complete a qualified weighing process. If the feeding mechanism is out of order, the feeding mechanism will automatically pour the weighing material into the unqualified station receiving cup, and the system will give a prompt message. When the material level in the storage bin is reduced to a certain amount, the alarm will issue an audible and visual alarm to prompt the operator to load the material to ensure the continuous work of the automatic Loading machine.