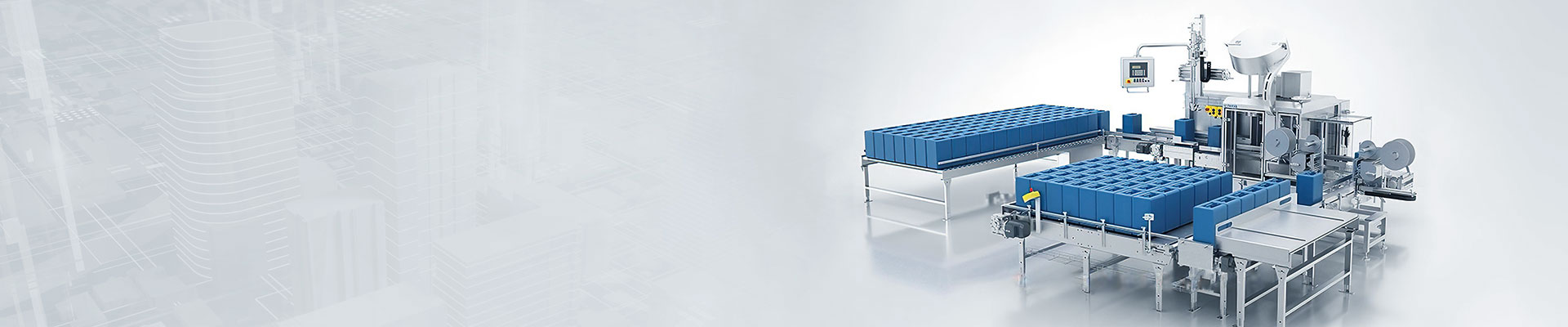
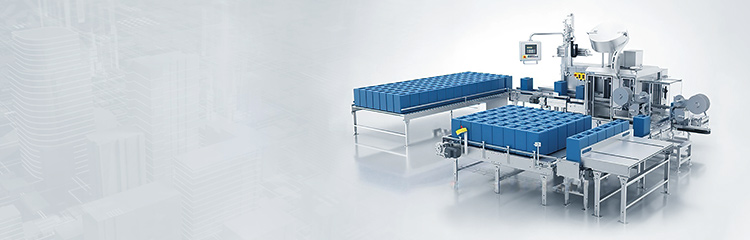
A variety of mixing groups are installed with weighing modules, which are configured together according to the proportion requirements of the formula, fed into a periodic "batch mixer" for mixing, and configured into a feed flow containing various components according to the proportion of the formula. When the feed flow into the continuous mixer, mixed into a uniform feed flow.

The production process of the Feeding machine generally includes the reception and cleaning of raw materials, crushing, batching, mixing, granulation, packaging of finished products into storage and dust removal and fire protection systems, each production link is an independent production section. Each system in the process of raw material production is relatively independent, and the automation of raw material production includes the automatic control of the entire system and the automatic control of each process and the automatic control of single equipment. Among them, PLC is responsible for controlling the operation of the field equipment and obtaining its operating status and fault information, the sensor system collects on-site information data, the computer uses network communication to obtain data for storage and management, dynamically displays the process flow, equipment operating status, production data, alarm information, and generates various production reports. Its core control component PLC, the use of modular programming ideas, separate the subsystems and relatively independent internal functions, and each function block in accordance with the raw material production system process flow through together to form a distributed control of the entire system, and through the network to achieve remote monitoring and production management command system.
The automatic Feeder is composed of PC, PLC, feeder, hopper, weighing module and actuator. The running process of the system is that the upper computer first transmits the raw material formula data to the lower computer PLC, and then it is controlled by PLC. All kinds of raw materials are distributed into the corresponding distribution bin for storage through the warehouse top conveying equipment and dispenser. When batching, the feeders send the raw materials to the hopper scales in turn. Large ratio (≥2O) of raw materials sent to the large hopper scale; Small proportions (5 ~ 20) of raw materials are sent to the small hopper scale for weighing. The weighing module detects the quantity of each material, transmits the signal to the weighing instrument, controls the feeding of the feeder, and thus controls the quantity of each material. When all the materials in the bin are weighed and blended according to the set formula requirements and the specified cumulative quality (amount of each batch) is reached, the PLC opens the material door according to the control procedure and puts the materials in the hopper scale into the mixing chamber of the mixer for mixing. When the mixer reaches the predetermined mixing time, that is, when the mixing uniformity meets the requirements, under the control of PLC, the material door is opened and discharged, the material is fed to the buffer bin, the finished product is dropped by the scraper conveyor, the product is sent to the bucket elevator and the mixing bin is stored to the next process.
According to the production process, the computer transmits the corresponding formula and production process parameters to the PLC, and the PLC controls the frequency converter to start the batching dragon according to the formula parameters and the feeding sequence, and the weighing signal is detected by the PLC. Working order of the feeder: After the weighing is completed, when there is material in the mixer, the hopper scale door is closed; When the mixer discharge door is in place, the hopper scale door opens. When the opening time of the hopper scale arrives, the residual material on the hopper scale is detected. When the residual material exceeds the limit value, the system gives an alarm, and the hopper scale door is not closed. When below the limit value, the hopper scale door closes. After the hopper scale door is closed and in place, if the scheduled production batch is not completed, the dosing continues, and the addition of premix and grease is signaled. After the premix is added and the response reset is completed, the mixer starts the mixing time. After the mixing time is reached, the mixer opens the door and releases the material according to the material level of the buffer bucket. After the opening time arrives, the mixer door automatically closes, and the next batch of material falls, and a new round of cycle begins.