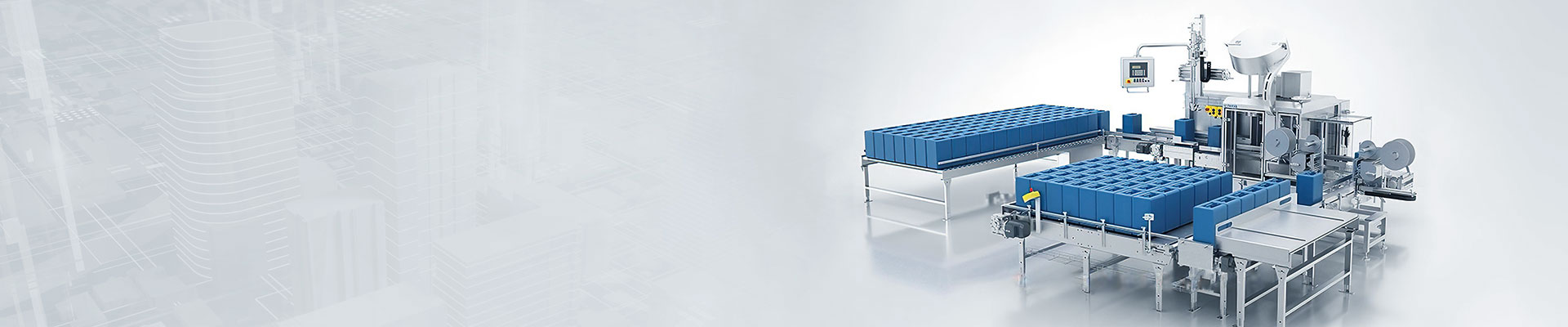
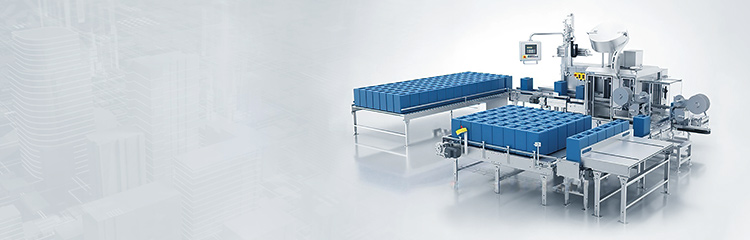
The automatic control system is composed of several weighing and feeding units. The weighing and mixing machine is equipped with a set of controller, and then the controller is connected to the computer. The pneumatic ash removal system is composed of a mutual monitoring mechanism of computer and controller and a variety of alarm mechanisms, and the method of transporting ash in the pipeline by means of pressure equipment (positive pressure or negative pressure).

The weighing control system is composed of several weighing and feeding units. The weighing mixer is equipped with a set of controller, and then the controller is connected to the computer. The pneumatic ash removal system is composed of a mutual monitoring mechanism of computer and controller and a variety of alarm mechanisms, and the method of transporting ash in the pipeline by means of pressure equipment (positive pressure or negative pressure). The whole conveying system has a very simple system, which only needs to compress the air source, the feeding device, the transportation pipeline, the receiver with the role of separating the gas and the material, and automatically controls the material transmission volume to monitor the input and output of the factory. The main components are level meter and pneumatic actuator, electric air lock, material sending equipment, dry ash concentration equipment, dust collection equipment, air source equipment, air drying device, ash removal pipeline, warehouse bottom equipment, etc. To realize the automatic control and supervision of raw material feeding, weighing and metering, vacuum feeding, dispersion and mixing processes, the dispersion time and cylinder number can be selected and adjusted on the computer according to the production requirements, and the opening and closing of the motor equipment and the opening and closing of the feed valve in the process are controlled by the computer.
In order to achieve accurate control of the dosing process and achieve the purpose of increasing production, improving quality, reducing consumption and stable operation, the automatic feeding system must carry out comprehensive control of the reactor operating parameters, which include structural parameters, current, voltage, power, raw material composition, cooling state, electrode parameters, operation mode and other variables. The ash removal system is a ash removal conveying system of a bunker. During the normal operation of the reactor, fly ash is deposited in the ash hopper, and three bin pumps are planned to be installed under the ash hopper, and then transported to the ash warehouse through a ash transport pipeline. The initial state of the bin pump each valve is closed. During the feeding process, the balance valve is opened first so that air can be discharged from the bin pump, while the discharge valve in the pipe is closed to prevent air from being drawn into the ash hopper. After the feed valve is opened in the balance valve, the material falls into the bin pump under the natural action of gravity. When the bin pump shows that the material in the pump is full (the level meter is covered) or reaches the set time, the feed valve and the balance valve are closed, and a short time delay is required in this process, that is, the time for the valve to close. After the feed valve and balance valve are closed, the intake valve will be opened to feed air to the bin pump and pressurize. When the pressure reaches the set time or value, the discharge valve will be opened and the compressed gas will be transported into the ash warehouse through the pipeline. After the material to the ash warehouse, the delivery of the bin pump is completed, the pressure in the pipeline is reduced to a specific lower limit, the intake valve is closed, and after a period of time delay, the remaining pressure in the pump is discharged, the discharge valve is closed, and you are ready to wait for the next cycle.