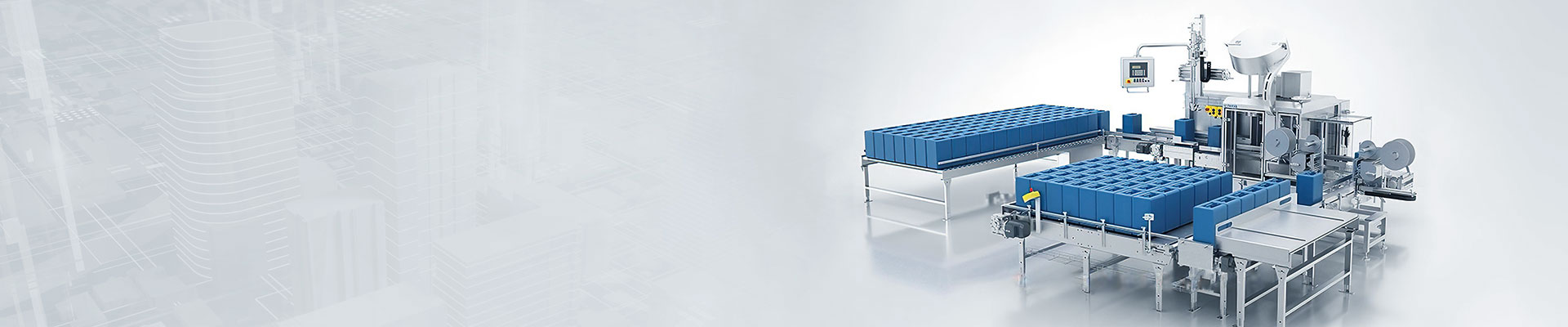
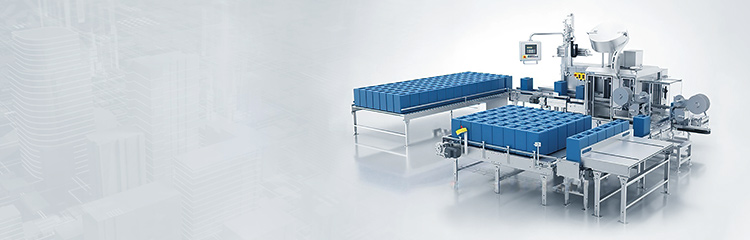
The automatic dosing machine loads all the powdered raw materials into the powder bin through the bag opening machine, and then transfers the powder bin to the daily volume silo to meet the powder required for daily production. Daily volume silo has upper and lower limit control, when the powder level drops to the lower limit, the system will give timely replenishment, when the material level reaches the upper limit to stop replenishing powder. The same is true of raw oil. Each bin or tank is equipped with a weighing sensor, which automatically starts to dosing according to the formula transmitted from the upper computer.

The automatic dosing machine loads all the powdered raw materials into the powder bin through the bag opening machine, and then transfers the powder bin to the daily volume silo to meet the powder required for daily production. Daily volume silo has upper and lower limit control, when the powder level drops to the lower limit, the system will give timely replenishment, when the material level reaches the upper limit to stop replenishing powder. The same is true of raw oil. Each bin or tank is equipped with a weighing sensor, which automatically starts to dosing according to the formula transmitted from the upper computer. After the powder is prepared, it is transported to the mixing tank by the conveying device. After the oil is prepared, it is also sent to the mixing tank. The oil and powder are pre-mixed in the mixing tank by a high speed mixer and then transferred to the buffer tank. The material of buffer tank is prepared for the grinding machine. After the pre-mix is ground by the primary and fine grinding machine, it is transported to the adjusting tank. The material in the adjusting tank is the base material. After the base material is tested, the amount of oil required for adjustment is calculated manually.
The automation system of industrial batching machine adopts hierarchical and distributed system structure, which is mainly composed of upper industrial computer, signal acquisition card, field detection weighing instrument and weighing sensor, communication network and so on. The industrial batching machine is responsible for the monitoring, operation control and report printing and management of the whole system. The signal acquisition card is responsible for monitoring the signal acquisition of equipment and process parameters. The weighing instrument and the weighing module are primary components used to detect the operating parameters of the process, which are converted into standard signals by the transmitter and sent to the signal acquisition card for real-time and dynamic display on the host computer. The Batching system uses industrial computer + configuration software + data acquisition board to realize automatic batching production line to meet the needs of some small and medium-sized manufacturers. The on-site data is collected by the weighing module, processed by the data acquisition board and sent to the industrial computer. Through the analysis of the collected data by the industrial computer, the automatic batching process is completed, and the upper computer monitoring system software is developed with the configuration software "Kingview" to realize the real-time monitoring and management of the production line, alarm setting, trend curve, data report management and printing functions.