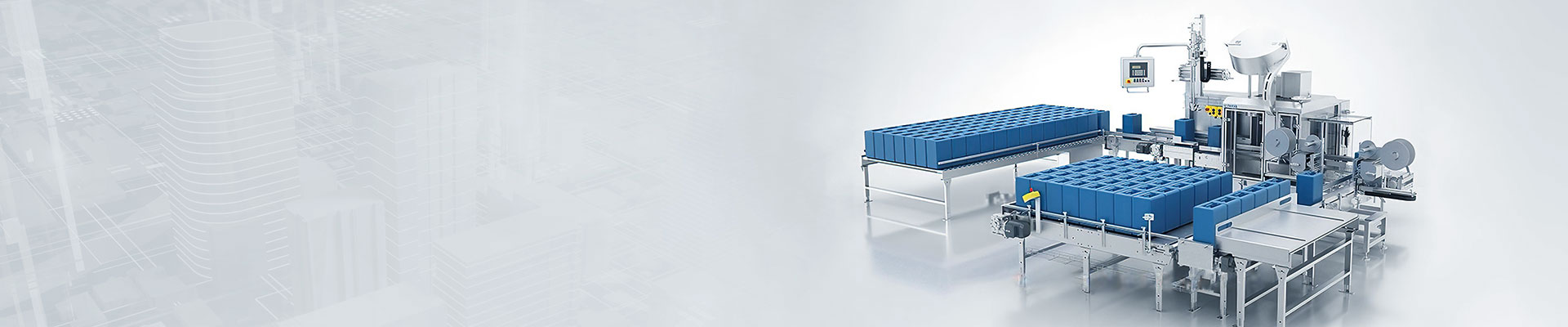
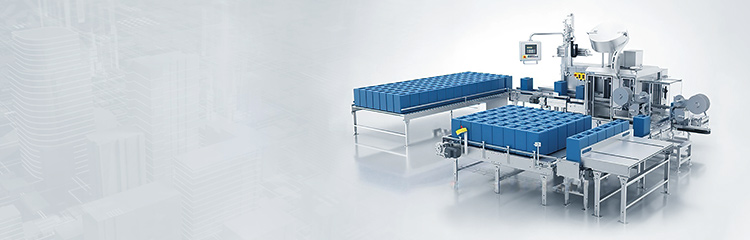
The feeding system adopts automatic control to realize the automatic control and supervision of raw material feeding, weighing and metering, vacuum feeding, dispersion and mixing processes. The dispersion time and cylinder number can be selected and adjusted on the computer according to the production requirements. The opening and closing of the motor equipment and the opening and closing of the feed valve in the process are controlled by the computer.

The main task of the raw material Feeder is to mix and feed, and on the premise of ensuring the production of material and formula accuracy and system reliability, the use of a larger set of self-developed batching machine in the raw material warehouse, concentrated for all the extruder preparation of the required raw materials. This allows all extruders to share a set of batching machines to reduce system cost and improve equipment utilization, while also eliminating raw material handling. The positive pressure thin phase pneumatic conveying method is used to blow the prepared raw material through the conveying pipe to the hopper of the extruder.
The feeder is mainly composed of two Roots blower units, a total feed pipe and a number of branch feed pipes, two pneumatic branch reversing valves (hereinafter referred to as branch valves) and a number of cyclone separators. One of the two fans is a backup fan, and each Roots blower unit includes a Roots blower, a typhoon electromechanical machine and a fan control cabinet, whose task is to generate compressed air flow required for pneumatic conveying. The fan outlet is connected to one end of the mixing chamber, and the total material delivery pipe is connected to the other end of the mixing chamber. The feeding system and part of the fan unit and the total feeding pipe can be installed in the raw material warehouse. The total feed pipe from the raw material warehouse is connected with an independent branch valve, which can form two branch feed pipes respectively to two workshops. Similarly, n+1 branch feed pipes can be formed with n branch valves, and these branch pipes are equipped with 1 branch valve at the location (hopper) of each extruder in the workshop. When selected to feed to a extrusion machine, the relevant branch valve is played in the corresponding direction, so that the material can only lead to the extrusion machine and can not go to other locations, so that the fan will mix the air mixture in the mixing chamber through the various links of the feeding channel to blow to the corresponding cyclone separator, after separation, the material reaches the corresponding extrusion machine hopper.