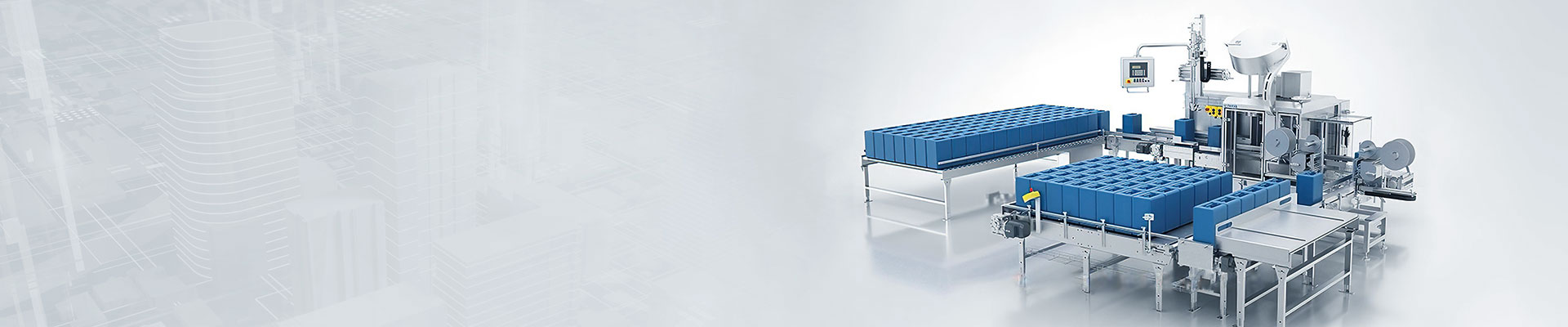
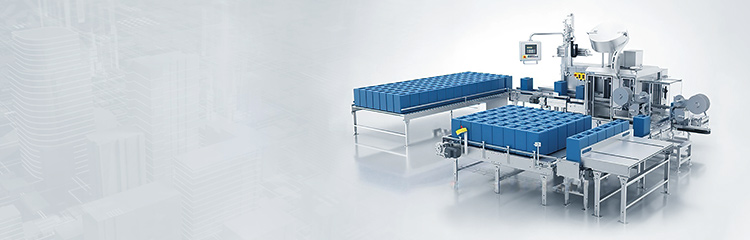
润滑油灌装机采用独立的伺服驱动控制,自动传输系统将其输入到计量工位,在此完成桶口的自动寻址后,由xy两轴步进电机带动充料系统到桶口处,再通过气动执行系统完成降充料头动作。设计应用了混合介质的传输技术以及令牌和主从的逻辑拓扑,可以同时在同一管道内控制灌装。

自动灌装机通过通信形成灌装的网络化监控,从而形成一个集管理和控制于一体的分布式自动灌装设备,所有灌装生产线严格协调生产,及时、准确地监控料位和重量。该称重系统由称重模块、称重仪表、灌装阀、滚筒组成,构成计算机控制网络,通过连接现场称量仪表、变频器等。实现以生产过程中,主料和辅料按一定比例匹配和称重过程的实时控制,完成填充系统故障检测、显示和报警,并向变频器输出信号以调节称重定量的转速,为上位机系统的中心访问提供数据。
液体灌装机是实现液态产品自动计量灌装的专用设备,用于计量和灌装所有类型的液体(流体、粘稠和糊状),并可选择有一个旋压系统。作业时只需将容器置于传输系统的输入端,其余作业程序(开盖、关盖除外)均自动化完成。可准确完成各种液态介质的自动充料和计量。
基本参数:
最大秤量:30kg
最小感量:0.01kg
灌装误差:±0.01-0.02kg
灌装速度:20L约150-180桶/小时
控制方式:2挡控制
灌装方式:插入式,液面上
枪头管路:特氟龙枪头、阀门+特氟龙软管
结构材质:主机SUS304不锈钢,输送码垛碳钢防腐漆。
秤台尺寸:400×800mm(304不锈钢动力滚道)
空桶滚道:400mm×2500mm(304不锈钢动力滚道)另附1200mm斜坡无动力滚筒
重桶滚道:400mm×2500mm(304不锈钢动力滚道,2组)
分桶装置:适用于20L桶,碳钢防腐漆结构,304不锈钢滚道。
码垛设备:平移式,适用托盘1200×1200×140mm,含供托盘、码垛、下托盘输送。
管路压力:0.2-0.6MPa(与料性有关)。
物料接口:DN40法兰接头4个,可按用户提供接口标准
气源接口:用户提供12mm气管接头,用于快速接头连接
使用电源:AC220/50Hz(用户提供至机器一侧)
使用气源:0.4-0.8Mpa(用户提供至机器一侧)
使用温度:-10℃-50℃
基础条件:助悬剂平的坚固混凝土地面,混凝土厚度应大于10cm。
可选机型:标准型、防爆型灌装