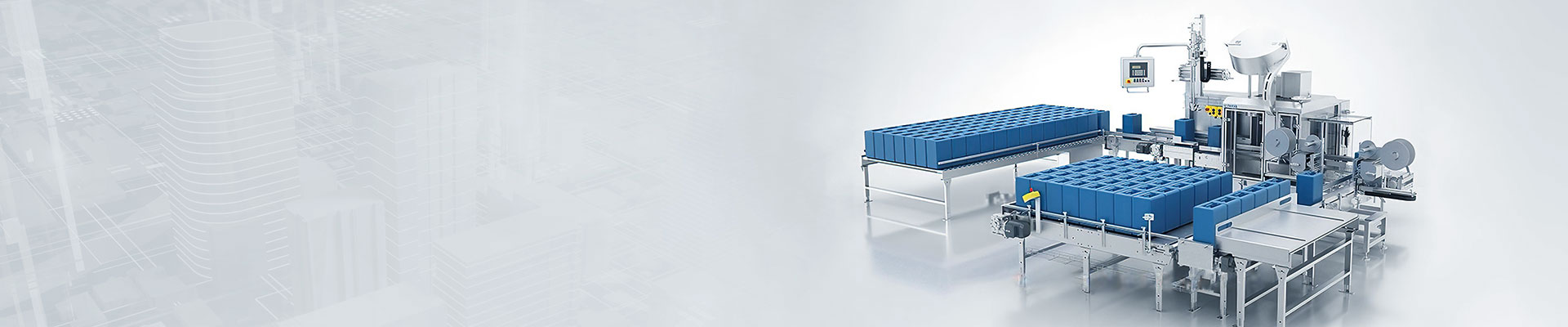
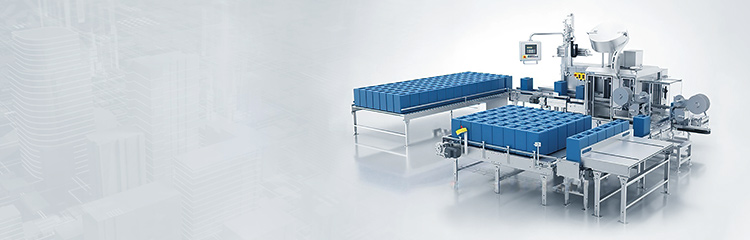
The conveyor batching line integrates your existing conveyor's weighing system for warehouses and packaging sorting terminals, and TLX Premium helps you provide batching control for revenue, optimized inventory control, cost savings and improved operational processes. At the same time, configuration control is to collect data, use high-end configuration software as the upper computer, through the upper computer to issue instructions to manage the automation equipment and process. The standard industrial computer software and hardware platform is used as integration carrier to replace the traditional system, which has the characteristics of strong adaptability and good openness.

The Feeder of the batcher feeds the hopper scale with two flows, and the weighing module converts the weight signal into an electrical signal and transmits it to the weighing instrument. Weighing control instrument measures the weight value and controls the whole weighing process to form automatic weighing control. The switch input signal in the system includes the start button, the stop button, the status of the pit door and other detection signals; The switching output includes control signals such as thick-thin feed solenoid valve and discharge solenoid valve, as well as some display and alarm output signals. The digital channel receives the weight input signal of the sensor, in which the closing of the weighing hopper door is controlled by the proximity switch, and the buffer door, weighing hopper door and pinch bag are controlled by the solenoid valve of the driving cylinder. Ideally, the large feed and the small feed together complete 95% of the rated weight value, and complete in a short time. Then the large feeding stops, and the small feeding completes the feeding amount of 5% to 10% of the rated weight value, which takes a longer time. In actual production, the weight and time parameters of these two sections should be constantly adjusted according to the specific situation to achieve the best state.
After the two weighing controllers of each batching line are set up, any Electronic scale (such as the A scale) is started. At this time, X0 and X1 automatically send A signal, and the large and small valves of A scale open. Put the last pre-charge in the large valve into the weigher. A balance fast and slow feeding screw starts feeding, when the weight of fast feeding (slow feeding at the same time) reaches the set value, the fast feeding signal X0 stops. A weighing valve is closed. The fast feeding screw stops after working for 2S, and then the fast feeding material falls on the large valve to do the next pre-feeding amount to improve the feeding speed. The small feed screw continues to feed to the actual value. At the same time the small valve feeding screw stops. A scale sends X2 discharge signal to PLC after judging that the weight is qualified. Then the photoelectric switch determines whether the bag box has bags, if not, then the alarm message is issued, the bag cylinder drives the suction cup to swing up and down, automatically grab the bag, the bag is placed on the tooth belt drive drag plate, transmitted to the positioning platform. When the bag mouth is sent between the upper and lower suction cups, the cylinder drives the suction cups to absorb the bag mouth and open, and the cylinder drives the bag to the storage hopper. PLC judged that the bag clip was closed. That is, the coat bag. The scale does not discharge material. After a delay of 3S signal to open the scale door discharge. Delay 1S to close the scale door and prepare for next loading. The electronic scale determines through the weighing sensor that the weighing bucket has been emptied and within the allowable error range, and sends X0 and X1 signals again to restart the feeding process. Otherwise stop feeding beyond the error display. The bag clip is opened after the delay time is determined by the PLC's special data memory (its size can be adjusted at will by the potentiometer on the PLC). After sewing the bag, put the bag on the belt conveyor. The B scale also works like the A scale. In this way, two scales and a PLC constitute a weighing dosing system that can work continuously in the case of manual bagging, which can improve productivity. In order to prevent the two scales from discharging at the same time, the interlock function should be added in the program.