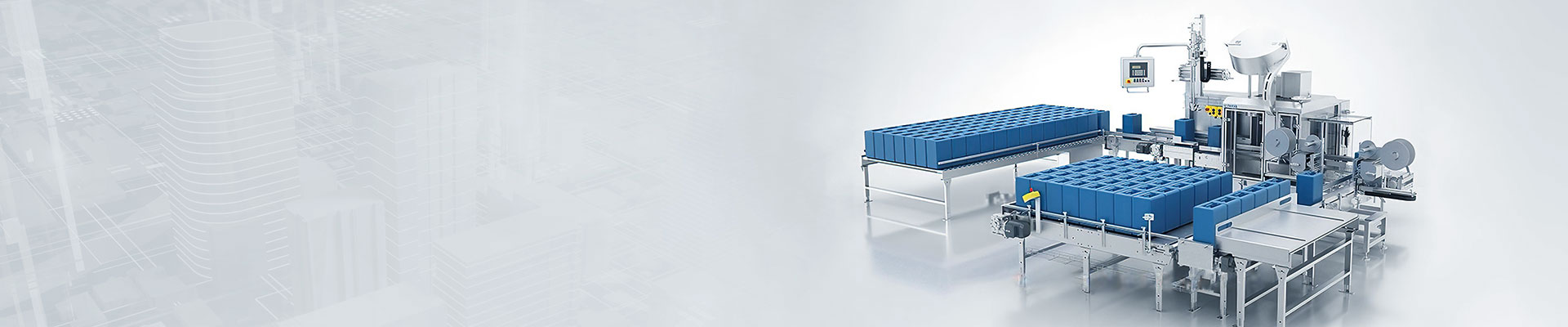
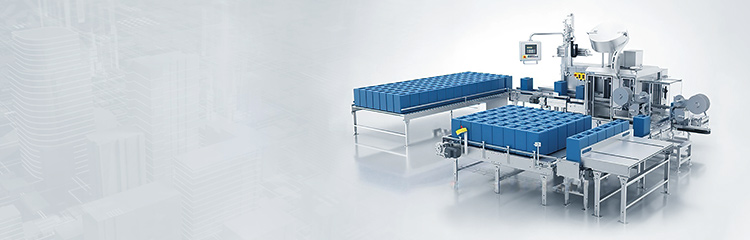
The automatic dosage system realizes the automation of weighing and dosage, the weighing and mixing of each powder is realized by the programmable controller (PLC), the upper computer is mainly used for the formula management, man-machine dialogue and the storage and printing of weighing data. Using the upper computer and weighing instrument communication program, weighing data collection, and data stored in the Access database. It facilitates the querying and tracing function of the data, which not only facilitates the supervision of the weighing process, but also restricts the operation of the workers. v

Automatic Dosage system is a very important process of Electronic scale in the production process of fine chemical enterprises, consisting of two sub-systems: pre and post dosage. Before the dosage scale in the total control microcomputer dosage control, the powder and other solid raw materials and liquid raw materials in the reactor after mixing to form a slurry. Weighing module slurry after aging, temporary storage by the high-pressure pump hit people in the silo, by the hot air drying to form the base powder. The former batching machine mainly completes the weighing and proportioning of the main material and various ingredients. After the batching machine will be formed by the former system of base powder through the spiral scale and conveyor mixer, raw material mixing, by sending people to the finished product warehouse, to achieve the measurement of the flow of conveyed materials.
Batching machine will be a variety of raw materials to be strictly in proportion to the uniform mixing, in order to ensure product quality, the raw materials in a certain proportion of uniform mixing together, used to form a new material. Take the industrial control machine as the upper host, and Siemens PLC, frequency converter and weighing instrument as the lower slave. To realize the communication management and control of each slave, the RS-232 asynchronous communication port of the industrial control machine is connected to the PLC after level conversion to form a physical channel for communication between the upper and lower units. Another RS-232 port of the host computer is connected to the communication port of the weighing instrument to form the second physical channel. The upper computer uses polling method to communicate with the slaves one by one. The upper computer transmits the result of task planning to PLC, and in the process of PLC control, the upper computer uses the upper computer connection command to monitor the operation status and data area content of the lower computer, reads the internal status of PLC and the real-time data of weighing instrument in real time, and displays them on the upper computer.
The automatic feeding system adopts DCS centralized control mode and selects Siemens S7-300 PLC to constitute the data acquisition and control system, which is modularized design and economical and practical. The human-machine interface monitoring software adopts "Configuration King", the leading configuration software in the field of industrial control in China, which has the advantages of good openness, easy maintenance and secondary development. All process control data and equipment operation status of the system can be centrally managed, recorded in real time, and printed and consulted at any time.
The dosage monitoring system consists of two computers as the human-machine interface of the whole system. One of them is the master station, which completes all the system parameters setting, process monitoring and data recording; the other one is the slave station, which takes the master station as the support, and is in charge of the data setting and process monitoring of the dosage system after the master station. The master station communicates directly with Siemens S7-300 PLC Weighing system, the automatic control weighing instrument of the front dosage scale and the rear dosage scale.