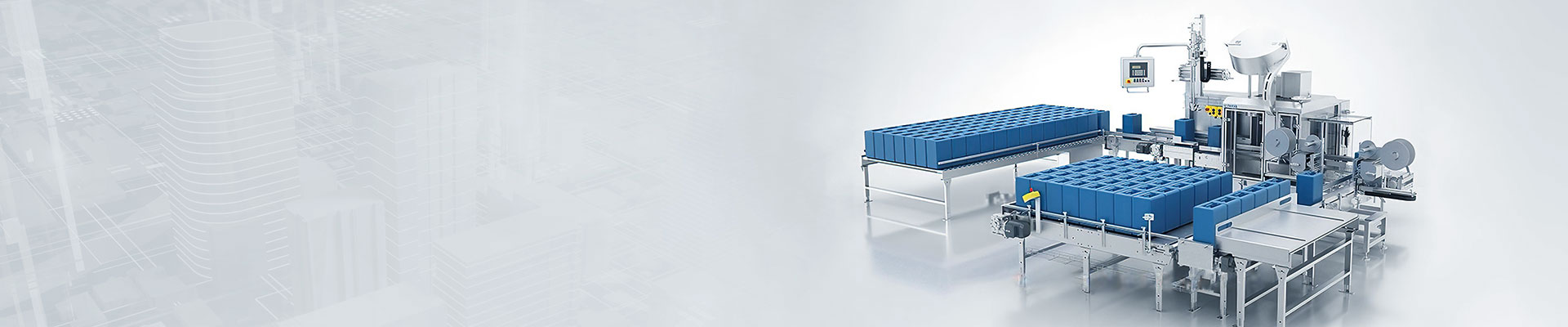
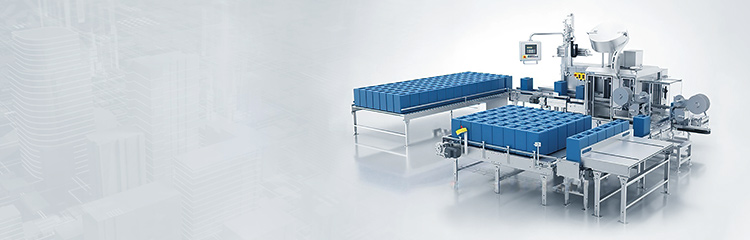
Measuring and feeding system adopts advanced control algorithm and new generation of single crystal chip microprocessor, which is more powerful, with faster operation speed and stronger anti-interference ability, automatic calibration compensation and vibration prevention function to ensure the best dosing accuracy. It can be automatically calibrated every time it is turned on to ensure accurate precision. Users can directly access the PLC system, terminal control system to realize multi-range control and automation control. The system digitizes the weak weight signal output from the weighing module to obtain high precision weighing data. Rich digital filtering technology is set up in the software, as well as emergency software to prevent interference with the system out of control.

The dosing system is through the combination of weighing module, weighing instrument and control system. To achieve the weighing and measuring work of the reaction tank body, so as to control the system. Weighing and control system mainly consists of multiple Weighing modules, multi-way junction boxes (including amplifiers), weighing instruments, and output multi-range control signals. The system can be applied to all kinds of box weighing, canned liquid, solid weighing and dry powder mixer, mortar batching mixer, liquid batching tank, etc.. Users can directly access the PLC system, terminal control system to realize multi-range control and automation control.
The design of the feeding system adopts HMI+PLC system, which integrates multiple sensors and actuators into a powerful weighing and Batching system, which can be applied to various chemical operation units requiring precise control, measurement and quantitative dosage. All equipment of the weighing unit is centrally installed on a steel base, and the whole set of equipment includes weighing and metering system, heating and holding system, liquid Feeding machine and automatic control system. The Weighing system consists of weighing module, weighing table, level adjuster and accessories. The dosing pump consists of dosing pump, safety valve, back pressure valve, pulse damper, pressure gauge, ball valve, pipe mixer, pipeline and accessories.
The automatic control system consists of industrial PH meter, contactor and control circuit, which is responsible for the operation of each electric equipment. The control mode is PLC+HMI full automatic control, the signals collected from the sensors are transmitted to PLC by the meter transmitter, and after the operation of PLC program, the dosing system is automatically controlled and the related parameters are displayed on the HMI interface.
The upper drum storage tank is installed with high and low level switches to detect and control the high and low levels of the tank respectively. When the high level is reached, the inlet motorized ball valve 1 closes the inlet action; when the low level is reached, a warning is issued and heating is stopped. The lower barrel storage tank adopts low liquid level switch and weighing module to control the liquid level automatically, when the weighing module detects the lower limit of the set value, it automatically opens the electric ball valve in the middle, and discharges the preheated medium from the upper barrel to the lower barrel; when the weighing module detects the upper limit of the set value, it closes the electric ball valve; in addition, the lower barrel is also fitted with a low liquid level float switch, when the lower barrel is finished conveying the liquid to the low level, the system closes When the liquid in the lower drum is delivered to the low level, the system shuts down the heating, stops the metering pump and sends out an alarm.