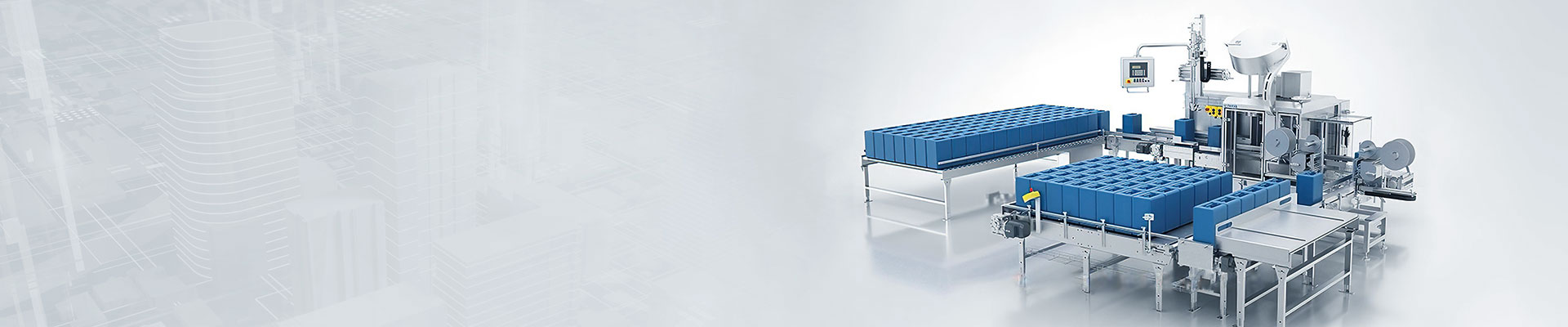
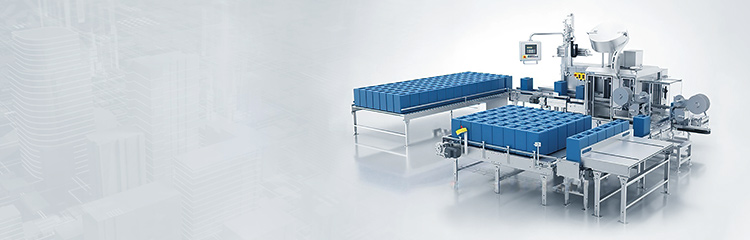
Paint filling machine using PLC programming control touch screen operation control, A/D chip and anti-vibration technology, filling a variety of operational processes interlocking control. Fast and slow two-stage or fast, or slow, slower three-stage filling method, the target amount of free setting. Selection of high-precision, reasonable range weighing module and filling actuator, start/stop control of feeding, through the weighing instrument TR700 transmission into the PLC for filling control.

The basic structure of the automatic Filling machine consists of five parts: cleaning session, filling session, capping session, packaging session and testing session. Cleaning link is through the recycling back to the bottle for cleaning, first of all first to empty bottles into the special cleaning fluid, bottle cleaning, disinfection, and then through the bottle pouring machine will be cleaned out of the liquid, and then cleaned empty bottles through the conveyor belt to the filling link. Filling link is PLC control solenoid valve will air pressure conduction to control the air pressure valve to bottle filling, when the liquid level reaches the standard height of the air pressure valve to stop filling, filling port will be filled after the bottle down, and then by the conveyor belt will be sent to the next processing link. Capping link fixed frame will put the bottle cap to the bottle mouth so that the thread of the cap and the bottle mouth thread overlap, through the conveyor belt to measure the wall of the friction chain will rotate the bottle, the cap will be screwed tightly, to realize the sealing of the cap.
The packaging link consists of two shafts that hold the wrapping paper in place. When the bottle is brought to the packaging position, the wrapping tape is glued at one end to the side wall of the bottle. Then the bottle is rotated so that the wrapping paper is wrapped around the bottle for a week after the wrapping paper is cut off the other end of the wrapping paper is fixed and bonded to the bonding place, the packaging process is over. Finally, the processed products through the detection of the light sensor detection of bad, including bottle external damage, cap encapsulation bad, bad packaging, filling level bad, etc., and finally the robot will be unqualified products moved to the designated area, qualified products for the box to the end of the entire process control requirements.
Weighing and filling machine needs to be designed for manual and automatic two modes of operation. Manual mode is used for the maintenance and debugging of equipment and counting statistics reset, automatic mode allows the normal operation of the production line to start.
Basic parameters:
Maximum weighing capacity: 1200kg
Minimum Sensitivity: 0.2kg
Filling error: ±0.2-0.5kg
0Filling speed: 200L about 150-180 barrels/hour
Control mode: 2-speed control
Filling method: Insertion, liquid level up
Gun head line: Teflon gun head, valve + Teflon hose
Structure material: host SUS304 stainless steel, conveying palletizing carbon steel anticorrosion paint.
Weighing platform size: 1200×1200mm (304 stainless steel power raceway)
Empty barrel raceway: 1200mm × 2500mm (304 stainless steel power raceway) with another 1200mm slope without power roller
Heavy drum raceway: 1200mm×2500mm (304 stainless steel power raceway, 2 sets)
Separate barrel device: suitable for 200-1000L barrels, carbon steel anticorrosive paint structure, 304 stainless steel raceway.
Palletizing equipment: pan-transfer type, suitable for pallets 1200×1200×140mm, including supplying pallets, palletizing, and lower pallet conveying.
Pipe pressure: 0.2-0.6MPa (related to material properties).
Material interface: DN40 flange connector 4, according to the user to provide interface standards
Air Connection: User supplied 12mm air hose connector for quick coupling connection
Power supply: AC220/50Hz (user-supplied to one side of the machine)
Using air source: 0.4-0.8Mpa (provided by the user to the side of the machine)
Use temperature: -10℃-50℃
Basic conditions: horizontal solid concrete floor, concrete thickness should be more than 10 cm.
optional models: standard, explosion-proof filling scale