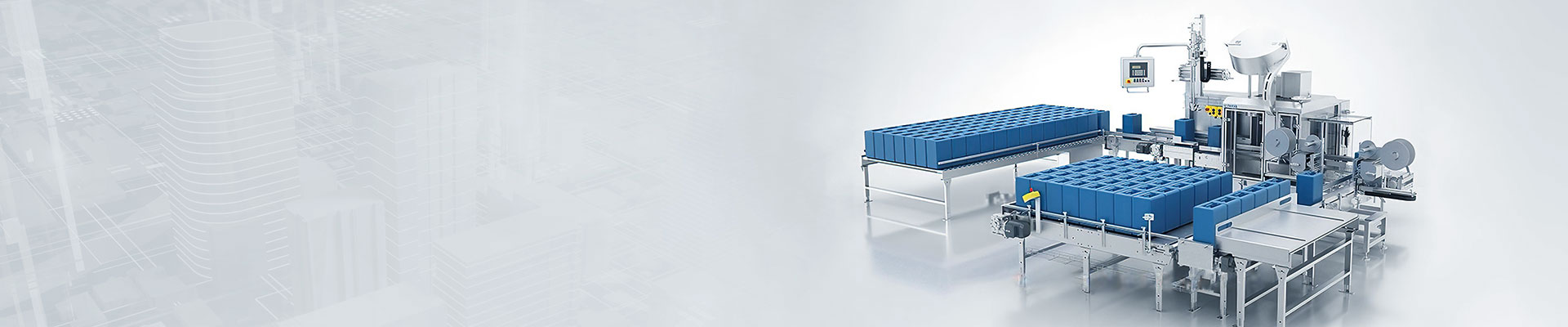
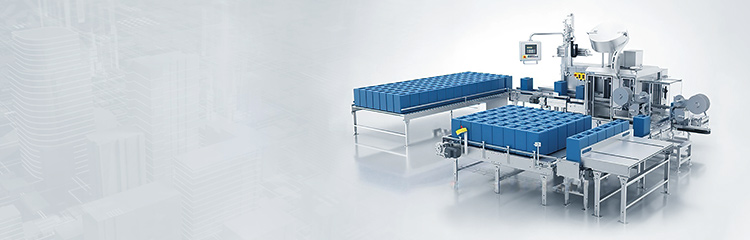
Gasoline filling machine is mainly composed of weighing platform, support column, ball screw, filling pipe, filling gun, pot pressure, moving filter, ventilation device, electrical control box, stepping motor and so on. The weighing instrument support column supports the entire filling mechanism, including the frame of the ball screw, stepper motor, filling pipe, etc. The stepping motor drives the ball screw to drive the filling pipe and the filling gun up and down, and the material is pressed into the packaging drum through the movable filter, the filling pipe and the filling gun.

Liquid Filling machine is mainly composed of weighing platform, supporting column, ball screw, filling pipe, filling gun, pot pressure, moving filter, ventilation device, electrical control box, stepping motor and so on. The weighing instrument support column supports the whole filling mechanism, including the rack of ball screw, stepping motor, filling pipe and so on. The stepping motor drives the ball screw to drive the filling pipe and filling gun to raise and lower. When filling, the material is pressed into the packing iron drum through the movable filter, filling pipe and filling gun. Before filling, the gun is usually lowered to a position closer to the bottom of the barrel, so that the gun nozzle is always above the average liquid level of the material during the whole filling process, which can effectively ensure that the material can be completely filled into the packaging barrel and keep the density of the material in different positions in the packaging barrel consistent. After filling, the gun should be lifted automatically and slowly with the increase of filling weight, and the gun is lifted by the ball screw driven by the stepping system.
Automatic filling machine adopts programmable logic controller, comprehensive monitoring of the operating conditions of the relevant equipment to improve the safety operation coefficient, and the collection and processing of various types of data with the server for data exchange in order to realize the sharing of data. Monitoring management is through the computer technology network technology database management system and software technology, filling data and monitoring information centralized processing, so that its daily work, such as sending and receiving, transfer and other operations programmed, standardized, institutionalized every step of the operation of the law can be relied upon to have the basis for the elimination of management loopholes.
Daily data reporting, review and summarize timely and accurate filling information. With alarm display, alarm management and event query, printing: real-time data collection, archiving, management and trend graph display; production statistics report generation and printing, the realization of the filling before the site contact and operation mode (linkage / single-action) to choose the function: the realization of filling over the kind of automatic switching and sequential start-stop equipment: including the realization of the manual control of the local control and remote control of the switching each other; alarm screen display; printing alarms, reports, events; real-time alarm / event information printing function: event logging (operator operator records process parameters or equipment status and control mode query). Alarm screen display; print alarms, reports, events; real-time alarm/event information printing function: event logging (operator operation records process parameters or equipment status and control mode change alarm generation, confirmation, etc.) with a variety of alarm monitoring, such as: liquid level high/low limit and other alarms with the configuration of parameter modification of the automatic recording and all types of alarms automatically record the function of the system to improve the traceability of the system and enhance the preventive capabilities of the system : monitoring system hardware troubleshooting and status monitoring function, historical data collection and automatic archiving and storage function: with a variety of categories of data query function.
Technical specifications:
Measurement accuracy: 0.2 grade.
Graduated value: 0.01kg (kilogram).
Maximum weighing capacity: 300kg (kilograms).
Sensor type: resistance strain gauge type force sensor.
Output mode: relay output
Operating conditions: AC220V±15%, 50HZ±4
Ambient temperature: 0~50oC
Relative humidity: 10-85%RH