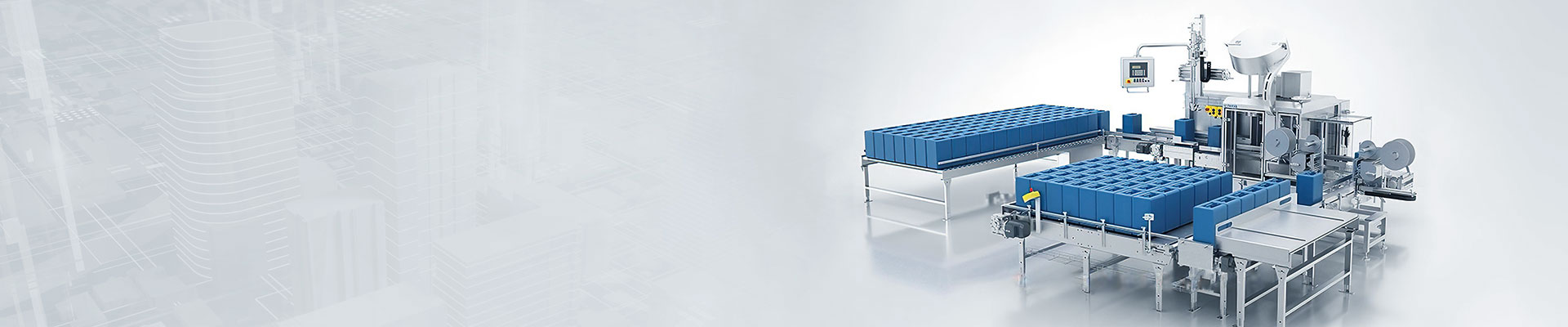
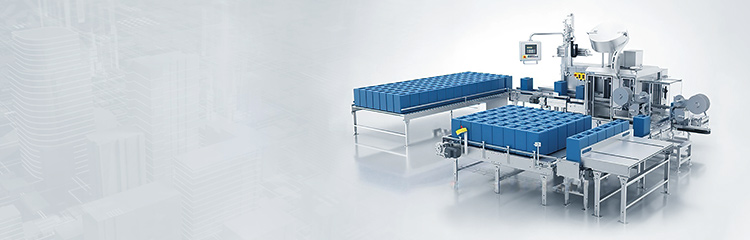
Liquid filling machine through the RS-422/485 interface can be fast communication and setup, hardware configuration and external wiring part of the expansion of analog input and output modules, its programmable controller switching inputs and switching outputs with networking and communication capabilities, you can use the PLC comes with a basic control unit to design its start and stop.

Automatic Filling machine is based on PLC and inverter as the core, through a variety of sensors and I/O data acquisition card, the filling actuator into real-time control and adjustment of the automatic control system. The objects controlled by the Filling system include the transmission motor, protective gas valve, filling valve, lower cap mechanism and gland mechanism of each production station. The data collected include the storage cylinder, on-line bottle level, protective gas pressure, liquid flow rate during filling, the speed of empty/full bottle conveying belt, the status of empty and full bottle in place, pile up, lower cap, opening and closing of the loading piston valve.
The automatic filling machine is composed of a conveyor belt and a filling liquid tank, and the conveyor belt is driven by a motor. The motor can rotate backwards and forwards. When the motor is turning forward, the transferred cans pass through four stations in turn: empty can position, filling position, full can position and terminal position.
The control panel includes two kinds of equipment, including the control panel of the lower machine and the HMI(human-machine interface) of the upper machine, which can control the automatic filling machine respectively. The lower machine uses an ordinary control panel, which requires the design of start and stop buttons, emergency stop buttons, lower (PLC)/ upper (HMI) selection switches, manual/automatic selection switches, positive and negative switch, fault reset button, counter, count reset button and various indicators. The PC man-machine interface requires the HMI device to use TP177BcolorPN/DP touch screen as the control device.
The whole system requires the lower computer to use Siemens programmable controller S7-300 for control and management, and the upper computer requires the configuration software WinccFlexible to dynamically present the site status to TP177BcolorPN/DP touch screen with graphics, tables, curves, etc., to monitor the site. Siemens MM440 series frequency converter is used to drive the conveyor motor, and the programmable controller S7-300 is required to communicate with the MM440 series frequency converter through the Profibus-DP network, and the frequency converter drives the motor.
Weighing and filling machine need to design manual and automatic two working modes. Manual mode is used for equipment debugging and full tank value reset. Automatic mode allows to start weighing machine operation. The control system should have the functions of emergency treatment, fault diagnosis and display. When the equipment fails, the control system can respond immediately, the corresponding indicator on the control panel or HMI flashes, after the fault is removed, only by pressing the fault reset button, the filling machine can run automatically.
Basic parameters:
Maximum weighing capacity: 30kg
Minimum Sensitivity: 10g
Filling error: ±10-20g (depending on the filling speed)
Filling speed: 100-150 barrels/hour (depending on the flow rate of the feed material)
Applicable containers: ≤Ф350xh500mm small mouth barrels, open mouth barrels
Explosion-proof grade: EXdiaIIBT4
Power supply: AC220/50Hz
Using gas source: 0.4-0.8Mpa
Use temperature: -10℃-40℃
Control mode: 2-speed pneumatic control
Filling method: insertion type, liquid level up
Weighing platform size: 400×400mm
Temporary storage table surface: 400×1000mm
Structure material: SUS304 stainless steel.
Head piping: SUS304 stainless steel and PTFE (316L optional)
Material interface: DN40 quick-fit pagoda connector, optional flange connector.
Air supply interface: 8mm air tube access