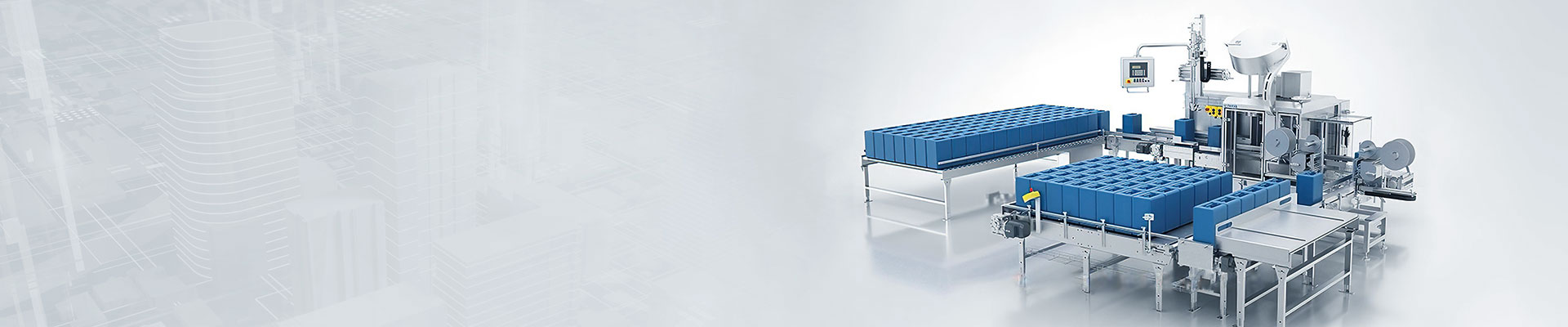
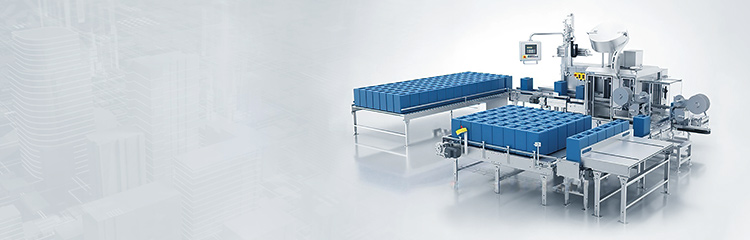
Automatic batching machine is a complete set of automatic equipment for dynamic weighing and batching control through electrical control management and visual man-machine software configuration. The electrical control part of the system adopts Siemens PLC, which is programmed according to the production requirements. The software adopts the human configuration, according to the process requirements, through the monitoring system and PLC program to load the material to the weighing hopper weight, flow control, so as to achieve accurate measurement and batching.

Weighing automatic batching machine can quickly and accurately complete the quasi-dynamic metering of powder materials, and can simultaneously carry out real-time quality inspection of a variety of powders. It adopts multi-tasking operating system and communication capability, and utilizes a single-screw extruder, with a main motor of DC 75kW, which is driven by a digital DC speed control system. Extruded amount is by the equipment master processor on the communication port to RS422 and E590 DC drive system communication, adjusting the DC motor speed (i.e., the speed of the extruder screw) to adjust the speed of each material on the charging position of any one or several charging position in several batches after the charge, according to the instructions to enter the next material charging process; each charging process can be carried out between the automatic cycle or at any time there is an operator instruction to carry out the Single material batch charging or modify the cycle charging order. If a device fails during normal operation, the PLC can automatically stop the device before the source of material, cut off the source of material, and at the same time will be the device after the equipment delayed operation for a period of time, to ensure that there is no blockage of material in the feeding process. Feeding process time can be automatically or manually modified at any time through the host computer to set the parameters.
Material from the silo into the Feeder, the material weighing signal into the weighing funnel, weighing signal processed by the controller to control the vibration feeder to a certain speed of feeding material, when the measurement of the material reaches the set value, feeding stops; confirmed by the detection of the charging bin in the specified charging position, and to confirm that there is no material in the bin, according to the operator's instructions or the automatic program metering charging open, the material enters the charging silo; when the measured material all enters the charging bin, and the material is not blocked, the material can be automatically or manually modified at any time through the host computer set parameters. Material all into the feeding bin, and confirm the measurement of the material to the bin door closed, according to the operator instructions or automatic procedures to add the next batch of material, the same start according to the operator instructions or automatic procedures to start the feeding bin of the walking motor to complete the lifting process, the feeding bin to reach the specified location, the bin stops, the bin door opens, feeding, material poured into the bin; when all the material in the feeding bin poured into the bin, the bin return to the position, the valve Close, the feeding bin returns to the specified bin, start the next batch of feeding. After processing by PLC, the position (displacement) signal is used for dosage position detection, stroke correction and control (the stroke switch is given priority in the automatic Dosage system).
Design features:
1)Adopting continuous dynamic metering for quantitative measurement of solid and liquid powder materials, which can be controlled by fast and slow casting, not only to improve the precision, but also to ensure the production efficiency.
2)Centralized control by operator console, configuration software development, can quickly respond to changes in customer demand, friendly man-machine interface, the operator can monitor the working status of the production line in the control room, improve efficiency and the speed of dealing with abnormal situations;
3)The centralized installation of weighing instruments makes the communication with monitoring software and PLC more convenient, safe and reliable;
4)production, management software is powerful, can complete a variety of production formula management, process control, abnormal alarm and production data collection, storage, report analysis, printing;
5)Upgrade and expansion is convenient, the user needs to expand the existing system, only the system's newly installed sensor leads, valve control line into the control room, and increase the corresponding function module on the software interface, simple and fast.
6)with warehouse pressure, liquid level detection, in the raw material warehouse can be installed liquid level meter, pressure sensor, centralized control center on the liquid level, pressure and other real-time monitoring to avoid accidents.