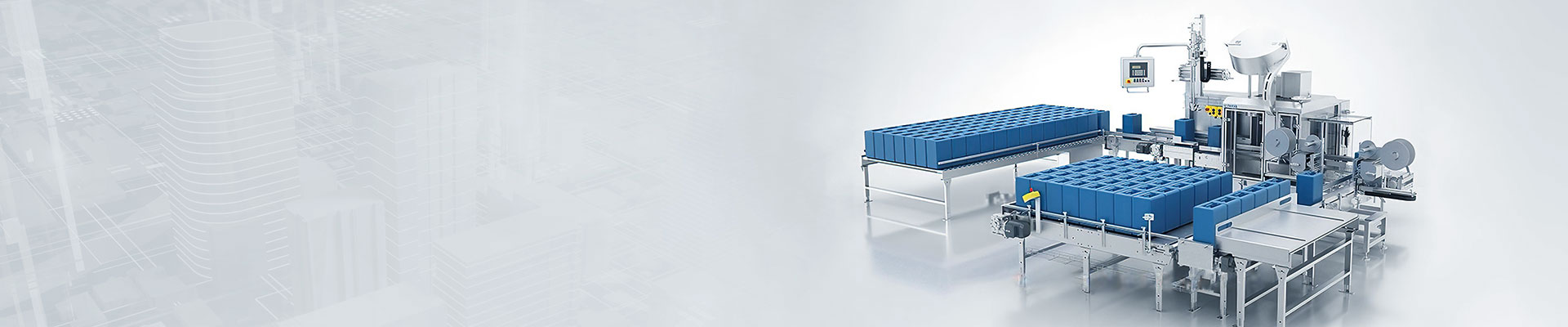
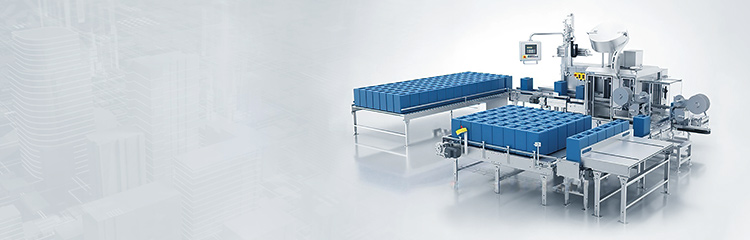
When the weighing and loading system feeds and weighs, due to the influence of the dropout, when the feeding is stopped, there is still a part of the material falling into the hopper scale in the air in a free-fall manner. In order to ensure the dosage accuracy, it is necessary to design a control algorithm for the termination of the feeding advance, to control the termination of the feeding advance, in order to minimize the impact of the fall on the dosage accuracy, so that the actual dosage value is kept within the error range. The algorithm takes advantage of the fact that the dosage production process is characterized by repeated weighing, and the results of the current weighing are used to correct the termination feed advance for the next dosage. After a limited number of trial dosages, it is possible to keep the static weighing value of the dosed material within the margin of error.

Weighing and Loading machine consists of two parts: hardware and software. Hardware part is mainly composed of mixing tank body, mixing tank cover, agitator, load-bearing weighing module, weighing instrument, transmission device, shaft sealing device and other programmable controllers, the upper industrial control computer system, etc.; according to the actual situation of the process, the two raw materials in the two raw materials before the delivery of the computer matching, according to the operator set the ratio of the two raw materials (i.e., the percentage) on the touch screen, the computer will automatically calculate the operating According to the proportion (i.e. percentage) of the two kinds of raw materials set by the operator on the touch screen, the computer will automatically calculate the running speed, and then according to the weight signals sensed by the two kinds of Electronic scales, the computer will analyze the calculation at any time and control the adjusting speed so as to achieve the set proportion.
Key features and benefits:
1) With automatic dosage control function and hand feeding control function for various solid materials in the formula.
2) With liquid scale weighing and adding liquid control function.
3) With flow meter adding liquid control function.
4) Timing control function for dry mixing, wet mixing and discharging of the mixer.
5) The system establishes a set of advanced security mechanisms and user rights management system, and assisted by the database security mechanism to ensure the security of the software system information.
6) Adopt hybrid computer system design, stronger fault tolerance and high reliability.
7) Equipped with perfect special dosage software, the system is stable and highly intelligent.
8) Optional function: with formula import function.
9) Optional function: support production data upload.
Improve the dosage production information management system:
1) Recipe management: input, storage, modification and deletion of recipes.
2) Production management: order placement, execution and raw material demand statistics.
3) Raw material management: the addition and deletion of raw materials.
4) Alarm management: alarm record, view and delete.
5) System parameters: mixing time, spotting time, closing time, drop compensation and hundreds of parameters such as silo, weighing hopper, mixer, small hopper, liquid spraying, etc. are set, modified and stored artificially.
6) Production data: you can add, delete and view the original production data.
7) report statistics: provide a variety of forms of various types of production reports, can meet the query requirements of different departments, all forms are provided in Excel file format to download.
8) User management: authority management for system users; data backup and recovery functions