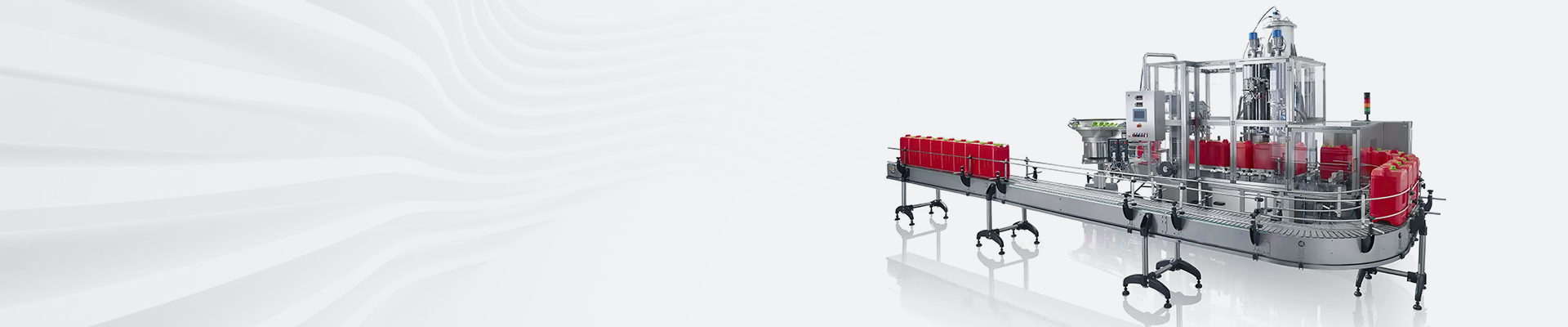
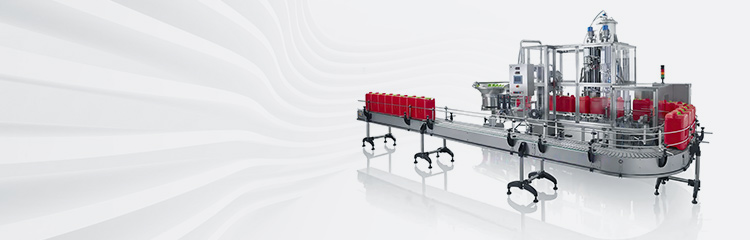

Summary:The batching system uses a vector control frequency converter with rotor magnetic field orientation to provide variable frequency speed regulation for each step of the batching process. It operates at variable speeds under the control of DCS through various pumps, and realizes automatic control through optical fiber communication.
As alumina feeding on the frequency converter puts forward high requirements, the design institute in doing the design, all without exception, choose ABB, Siemens, Schneider, AB and other imported frequency converter. A domestic 800,000 tons of alumina dosing line drive for the first time using domestic inverter, the network using automatic dosage system dual-network redundant communication control program, the field operation shows that the inverter runs stably, and successfully replaced the imported brands of inverters, and more cost-effective.
2 process and frequency converter requirements
2.1 Alumina batching process
From bauxite ore batching out qualified alumina need to go through the raw materials, dissolution, settlement, decomposition, baking ingredients and other large batching system process, according to the order of the process is organized for the raw materials, dissolution, settlement, decomposition, baking ingredients and other major workshops, in order to make full use of the mother liquor, and then set up an evaporation process workshop. Raw material workshop is used to prepare raw ore slurry whose particle size, composition ratio and other indexes meet the requirements; dissolution workshop provides high temperature and high pressure environment for raw ore slurry through multi-stage preheating casing and pressure cooker, and ensures enough dissolution time to dissolve alumina in raw ore slurry into sodium aluminate solution. The settling workshop separates the crude liquid in the slurry and the red mud consisting of attached alkali and various impurities through settling and many times of reverse washing, and the separated crude liquid is filtered by leaf filter to produce fine liquid, which is then sent to the decomposition workshop for mixing with the crystal seeds, and then enter the decomposition tanks step by step to cool down and agitate, so as to precipitate aluminum hydroxide sufficiently, and the precipitated aluminum hydroxide slurry is graded and then the fine material is fed into the seed filtration to prepare crystal seeds, and the coarse material is sent to baking material. The coarse material is sent to baking and batching workshop for high temperature baking and batching after filtration, and finally the finished aluminum oxide is produced. The evaporation workshop is used to concentrate the circulating mother liquor to remove the excess water in the mother liquor in the process and achieve the concentration of mother liquor required by the process.
2.2 Requirements of alumina batching for frequency converter
The whole alumina batching control system transports materials by slurry pump, feed pump, discharge pump, mother liquor pump, lye pump, circulation pump and other pumps with different functions. In the process of dosing, the temperature, pressure, dosing flow and other indicators of the material and reaction vessel are very strictly controlled; at the same time, in order to ensure the continuous operation of the decomposition tank stirring and other requirements for uninterrupted operation of the equipment, as well as diaphragm pumps, pressure cooker and other high-temperature, high-pressure, high-alkali equipment, flammable and explosive equipment, the requirement of transporting the material of the pumps to run under the control of the DCS at variable speeds. Alumina batching system process is more complex, batching environment is poor, high temperature, dusty, the main requirements of the frequency converter are:
1) slurry pumps, feed pumps, discharge pumps, etc., the working medium is very viscous slurry, its load characteristics close to the constant torque load characteristics. Due to some reason to make the batching system stop for a short time, viscous slurry will produce settling, restoration of the start again, these pumps starting torque is very large, so the frequency converter is required to have a large enough starting torque and high overload capacity.
2) Alumina batching occupies a large area, its electrical control equipment and frequency converter are installed in the distribution room, most of the motors and frequency converter distance in 100-300 meters, the output of the frequency converter is required to connect 100-300 meters of cable can work normally.
3)The output of frequency converter contains high harmonic, the number of frequency converter used in the field is large, we must consider the harmonic interference to DCS control system and on-site weighing instrumentation, and we require the output of frequency converter to have low harmonic content, which is lower than the harmonic content required by the national standards GB12668-2.2002 and GB12668-3.2003.
4) Alumina batching has continuity, batching process due to a failure of a piece of equipment caused by the whole line stops production, will bring great losses, therefore, the reliability of the frequency converter requirements are extremely high.
Technical characteristics of batching inverter
1) Standard STO (Safe Torque Off) and SS1 (Safe Stop 1) functional safety programs comply with the latest EU Machinery Directive 2006/42/EC.
2) Support Profibus-DP/Can/Automatic dosage system/DeviceNet and other buses.
3) Modular design of inverter unit, high power density, small cabinet size.
4) Inverter unit up into the lower out into the line design, easy to parallel form a large system
5) The mobile wheel-sliding structure design of the inverter unit is convenient for system maintenance.
6) Rectifier inverter power unit is compatible with each other, reducing the late maintenance costs
7)The inverter unit is controlled by the control unit through fiber optic communication, and the control unit is independent modular design, which is convenient for the system to become a cabinet, and can be installed in a distributed manner, and the strong and weak power are isolated, with strong anti-interference ability.
8) Four-quadrant rectifier energy feedback net side harmonics ≤ 5%, small interference to the grid
9)Adjustable bus voltage, when the grid voltage fluctuates greatly, it can ensure the output voltage is stable.
10) Superior vector control performance, large starting torque, closed-loop vector starting torque up to 200% of rated torque.
4Introduction of ControlNet redundant network
ControlNet for weighing and batching system is a real-time fieldbus network introduced in recent years for the control layer. It provides time-critical I/O data and message data, including program upload/download, configuration data, and end-to-end message transfer on the same physical layer media link, and is a highly deterministic, repeatable, high-speed control and data acquisition network, with better I/O and end-to-end communication performance than traditional networks. It is a highly deterministic, repeatable, high-speed control and data acquisition network with improved I/O performance and end-to-end communication performance over traditional networks.
ControlNet for automatic feeding systems allows multiple controllers to coexist on the same link and supports input data or end-to-end multiple transmissions, which greatly reduces the amount of traffic on the network and improves network efficiency and network performance. The ability of an automated dosage system to anticipate when data can be reliably transmitted to a destination, as well as the ability for the transmission time of the data to remain constant independent of network node addition/removal situations or busy network conditions. In practice, these requirements are further ensured by the optional setting of scheduled I/O groups or interlock times during network configuration.
The weighing control system ControlNet has the advantages of optional media redundancy and intrinsic safety, simple installation and maintenance, peer-to-peer status of the nodes on the network, and network access from any node; the topology (bus, tree, star, etc.) and the choice of media (coaxial cable, fiber optic, and others) can be flexibly selected.
Frequency converter field application situation
5.1 Frequency converter selection
A domestic batching enterprise new annual output of 800,000 tons of alumina smelting project, after selection of the final selection of a new generation of high-performance, rotor magnetic field oriented Goodrive800 engineering-type vector control frequency converter, its weighing and batching system process for each process to provide frequency speed regulation (power from 15kW to 800kW), a total of 144 units installed and used.
5.2 Control layer and equipment layer network topology
The entire batching electrical part of the control layer using AB DCS system, configured with dual-network redundant communication network, Goodrive800 inverter-based equipment layer nodes for control, the system topology (partial) is as follows:
5.3 Inverter selection and configuration
1)Aiming at the requirements of alumina batching on the inverter, the torque of the selected inverter at 1Hz can reach 200% without closed-loop operation.
2)Considering the overload factor, the capacity of motor will be increased by one grade in actual application, and the capacity of frequency converter will be increased appropriately.
3) Considering that the whole use of frequency converter is more, input reactor and input filter are added to the input side of frequency converter to ensure that it will not cause interference to the calculation control system and digital instrumentation under any circumstances.
4) Considering that the length of the output cable increases, the distribution capacitance and distribution inductance also increase accordingly, which may cause oscillation or form standing wave for a certain harmonic, which will seriously affect the operation of the motor. Install output reactor or add output filter on the output side of the inverter to suppress the dU/dt sharp pulse output from the inverter.
5.4 Electrical schematic diagram and function setting of inverter
5.4.1 Inverter control box terminal function
5.4.2 Inverter function code setting table
The inverter control principle of each process is basically the same, different sections and processes, there are some differences in the function settings, the table only lists the frequency converter function setting parameters of the pump after dissolution and dilution, for reference only.
6 Conclusion
At present, the frequency converter has been successfully put into operation for more than one year in alumina batching, and the high reliability of INVERTEN frequency converter has been fully verified, compared with imported frequency converter. Frequency converter in alumina industry successfully replaced the imported brand frequency converter, and more cost-effective, deeply satisfied with the user.