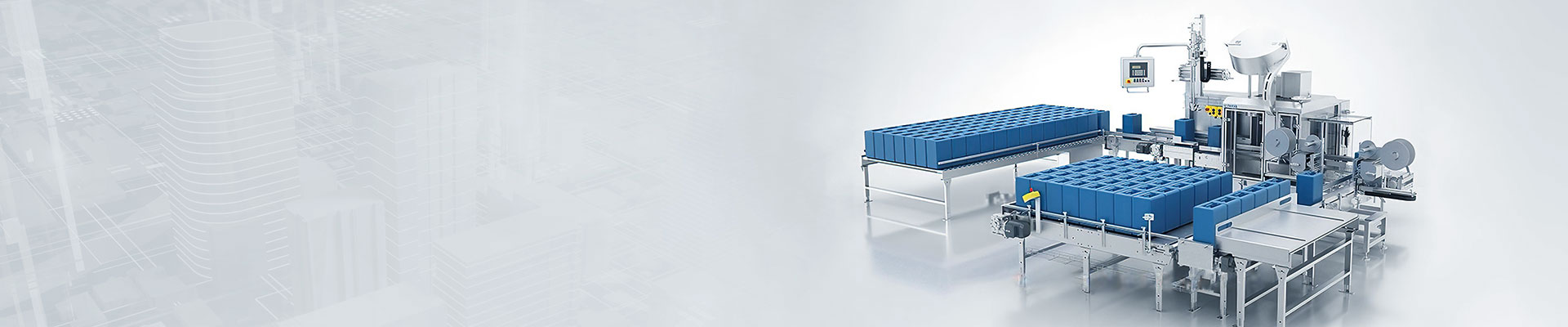
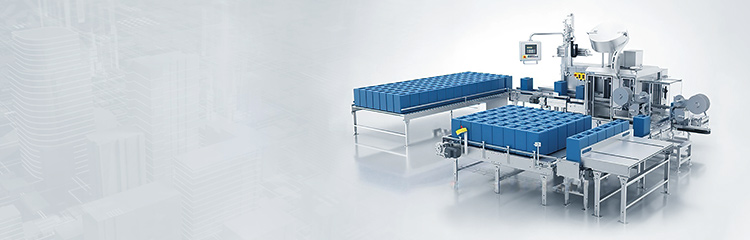
Sorting scales are composed of load cells, amplification circuits, AD converter circuits, microcontroller circuits, display circuits, keyboard circuits, communication interface circuits, and voltage stabilized power supply circuits. The weight signal is amplified and recognized, and when the weight of the product exceeds the pre-set upper and lower limits, the processor will output a rejection instruction to the rejection device on the rejection section, so as to remove the unqualified product from the rejection section. It is suitable for over and under weight detection, accessories missing detection and weight grading.

The inspected product of the checkweigher enters the Weighing system from the assembly line, and is transported to the weighing section through the accelerating section. During the movement of the inspected product in the weighing section, the weighing module undergoes deformation under the action of gravity, which prompts a change of its impedance and outputs an analog signal, which is then outputted by the amplifying circuit to the analog-to-digital converter of the weighing module and is quickly converted into a digital signal, which is transferred to the processor of the weighing module, and then operated by the weighing algorithm, and the weighing system is operated by the weighing algorithm. The weighing system processor amplifies and recognizes the weight signal. When the weight of the product exceeds the pre-set upper and lower limits, the processor outputs a rejection instruction to the rejection device on the rejection section, so that the unqualified product is removed from the rejection section. It is suitable for over and under weight detection, accessories missing detection and weight grading.
Sorting scale is a kind of assembly line equipment for automatic weight detection, mainly used for dynamic detection of whether the weight of the product is up to standard, so as to judge whether there is a lack of parts in the product package, product accessories or overloaded overweight and so on. Measuring the weight of the product during transmission and comparing the measured weight with the pre-set weight range, it automatically rejects the products whose weight is not up to the standard, or picks the products with different weight ranges into the designated weight class area. Measures the weight of products during the transfer process, compares the measured weight with a pre-set weight range, and automatically rejects products that do not meet the weight standard, or picks products with different weight ranges into a designated weight class area.
Can be quickly on the production line items for weight inspection or weighing, test standard weight can be set, real-time display of the test weight and quantity, and display the test results, automatic counting, automatic rejection of substandard products or meet the substandard products alarm, can be equipped with a computer touch-screen, Chinese windows, friendly man-machine interface, easy to operate, classification of daily and monthly reports query printing and other functions.
The structure of measuring and inspection machine mainly consists of incoming material speed matching section, weighing section platform, control main chassis and sorting reject section. Online Sorting machine work process:
Speed matching section: weighing products first into the speed matching section, its set speed, generally according to the spacing of the product and the required checkweighing speed to decide, so as to ensure that only a single product in the weighing platform.
Weighing section of the platform: the control system recognizes the product to be inspected and enters the weighing section according to external signals, such as photoelectric signals or internal level signals. The load cell transmits the weight signal of the product to the control system.
Sorting and Rejecting Section: When the control system gets the weight signal of the product, the system will compare it with the pre-set weight range and carry out rejecting or sorting operation on the product.
Detection speed: 50~80 pieces/minute, 20~40 pieces/minute;
Tolerance range: ±5~50g, ±20~500g;