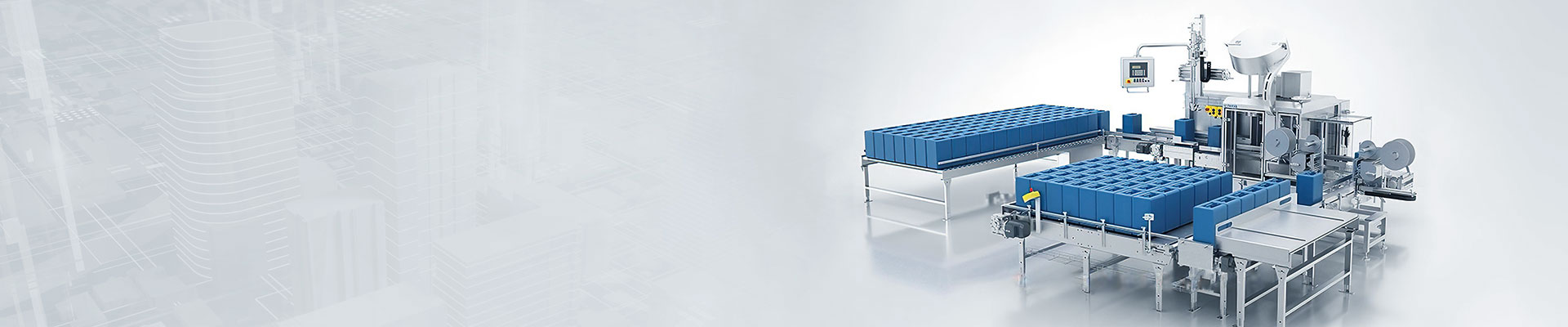
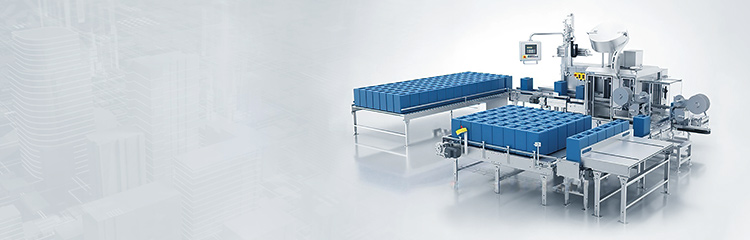
Pneumatic conveying system is divided into material storage, batching, metering system and electrical control system, which control system has automatic and manual operation mode, simple operation, flexible control, can meet the various needs of production, weighing system has high practicability. Can be adapted to powder, particles, liquid and other material ingredients, stirring control.

According to the site conditions and process requirements, the site is a dust explosion-proof environment, and the site weighing instrument is flameproof weighing instrument. The signal of the on-site weighing instrument is sent to PLC for status indication and interlock control. PLC performs interlock control according to the stored interlock control program, starts or closes the related valves on and off, sends out the switching signal to start and stop the bag dust collector, rotary feed valve (air shut-off)4X01 and Roots blower, etc. The switching signal is fed back to PLC. Interlocking control loops are introduced to ensure that various devices are in the correct state. Finally, the powder is transported to the bin outside the boundary area by compressed air along the closed pipe. Main on-site weighing instrument equipment; Fan outlet pressure pressure transmitter; Rotary feed valve (air shut-off) shaft seal valve; Y-type reversing valve; Y-type reversing valve valve position switch; Bin upper and lower level switch; The key to selection of on-site weighing instrument is the reasonable selection of Y-type reversing valve and the upper and lower limit level switch of bunker.
The pneumatic conveying system adopts the form of concentrated phase main and auxiliary pipe pneumatic conveying, and the equipment mainly includes the air source device, the pumping device, the conveying pipeline, the material gas separation device and the storage device. The conveying gas used by the conveyor is compressed air that has been dried and purified, and enters the conveying system from the upper part, cone and outlet of the fluidized bin pump in the form of fluidized gas and conveying gas respectively. The carbon black is fed to the disintegrator, and then enters the fluidized bin pump from the disintegrator. The fluidized gas pressurizes the bin pump to make it reach a certain pressure setting value. At the same time, the carbon black in the fluidized bin pump is fluidized under the action of the fluidized gas, and then the pneumatic butterfly valve at the bottom of the bin pump is opened, and the carbon black enters the conveying pipeline from the fluidized bin pump under the action of pressure to mix with the conveying gas and start conveying. The carbon black finally enters the day storage tank through the transmission pipeline, and the separator and induced draft fan installed on the top of the day storage tank separate the carbon black from the air, and the carbon black remains in the storage tank, and the gas is discharged to the outside. After the conveying process is completed, the carbon black enters the carbon black scale from the day storage tank for weighing. The volume flow rate of the gas in the conveying process is measured by the stress vortex flowmeter installed on the conveying pipe. In addition, 5 Weighing modules (3 on the horizontal pipe and 2 on the vertical pipe) were installed on the transmission pipe to obtain the change of pipeline pressure during the transmission of carbon black.