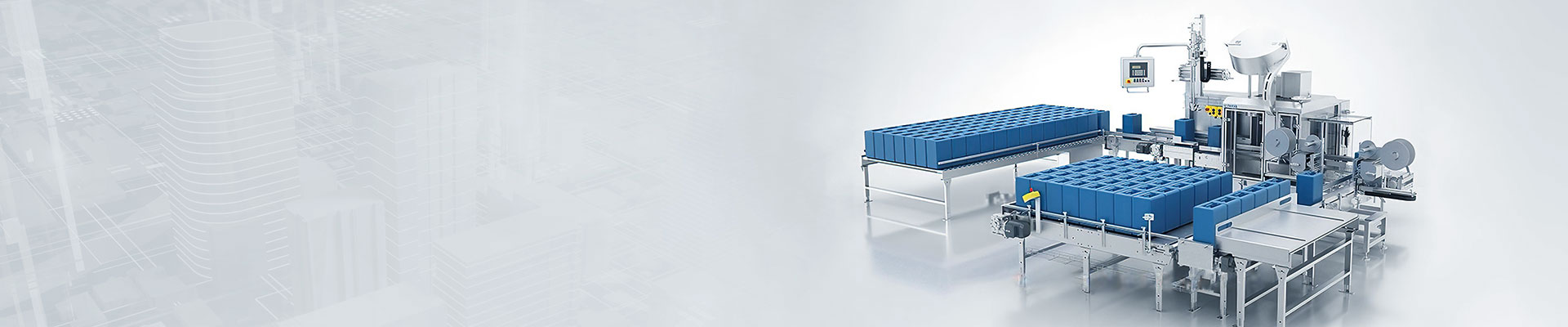
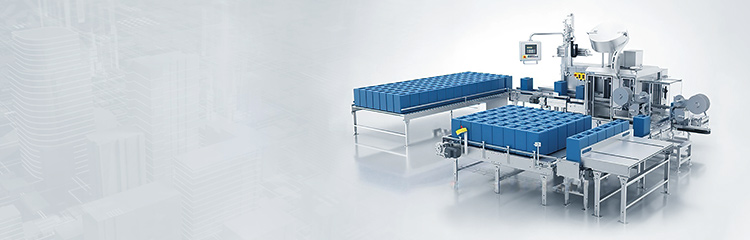
Pneumatic weighing system is a new generation of weighing control system, which is based on years of experience in developing control system and the affirmation of many customers. The reaction pot is characterized by simple control, applicable functions, high dosage precision and long trouble-free time.

Weighing and mixing machine is a kind of specialized batching equipment to realize automatic batching and mixing. This equipment can meet the batching and mixing process requirements of different granular and powder materials in various industries, and realize the automation, high efficiency and precise metering in the production process. The key principle to realize the automated metering and mixing process is the application of load cell. In the mixer equipment, the metering module is mainly used to detect the weight change of the material in the hopper, through the weight change to realize the automated measurement and the hopper material dosage barrel switching, and then ensure that the different particles, powder material dosage and mixing accuracy. The equipment realizes the automation and accurate measurement of the material formula through the automated continuous measurement process, and also ensures the consistency and uniformity of the mixing. In order to ensure the accuracy, effectiveness and stability of mixing, the equipment control system needs to develop relevant control strategies according to process parameters, equipment characteristics and material properties, so as to achieve the standardization and normalization of automated production.
Weighing mixer is mainly composed of pre-feeding feed screw (can also be used impeller Feeder and other pre-feeding equipment), weighing screw (or weighing spiral), weighing module, weighing controller, frequency converter and electrical control cabinet and other components. The feeding screw is the controlled actuator of the system, and the frequency converter governor adjusts the number of screw revolutions to regulate and control the feeding volume, so that the metering screw reaches the instantaneous flow rate set by the system. The metering screw runs at constant speed, measures the instantaneous material load in the spiral tube through the weighing module of the measuring key, and converts the material gravity into a proportional electrical signal input to the controller, which automatically adjusts and controls the material flow rate through signal processing, arithmetic, flow rate display and according to the set parameters.
The measured value of the instantaneous flow rate of the metering screw is compared with the set flow rate value required by the production. According to the size and direction of the deviation, the controller automatically adjusts the rotational speed of the feeding screw through the frequency converter to change the feeding rate and make it converge and reach the target value of the set flow rate, thus realizing the quantitative feeding control.
When the feeding of both axes are rotating, when the Electronic scale reading value will be close to a set value, the large diameter screw shaft stops working, by the diameter of the small screw shaft to rotate the feeding, and then to achieve the set value of the error within the range, and greatly improve the efficiency.
In the continuous delivery of materials (both screw shafts are working) at the same time weighing its weight, when it will reach the input weight value (large screw shaft pause), by the weighing module will signal to the control panel, and then the control panel will signal analysis will be suspended by the power failure of the large screw shaft. Then the flow of the small spiral shaft is used to approximate the required weighing value (within the specified error range).
Its working process mainly includes several steps of weighing, measuring, mixing and unloading.
First, the material enters the hopper through manual or automatic loading device. Then, according to the preset dosage and mixing ratio, the precise Measuring system measures the required raw material weight from different materials, and controls the switching and toggling of the raw material bucket through the change mechanism, thus controlling the adjustment of the formula ratio and the metering accuracy of the actual dosage. In the process of material feeding, since the density of materials is different, it is necessary to set the respective number of electronic scale blocks for different materials in the weighing process to realize accurate measurement. According to the recipe setting, the system automatically starts the motor, according to the established process parameters, using the mixer for mixing, mixing time and speed generally according to different material characteristics, specifications, adhesion and subsequent processing process requirements, to set different parameters. When the mixing time arrives, the system automatically discharges the mixed materials through the discharge port to continue the production process of the next batch of materials.
Workflow
1、Feeding stage: At the beginning of the equipment, the material enters the hopper through manual or automatic loading device.
2、Automatic measurement: accurate measurement is the core of the equipment, the basic idea is to use the weight sensor and accurate Measurement system, to realize automatic measurement and hopper material dosing barrels are switched to ensure the accuracy and effectiveness of the mixing.
3、Mixing stage: The mixing process mainly utilizes the mixing mixer and the motor to stir and mix according to the set parameters to ensure the consistency and uniformity of the mixing.
4、Discharge stage: the mixed materials are released through the discharge port to continue the production process of the next batch of materials.
Application Scenario
Weighing mixer has a wide range of applications, mainly used in food, medicine, chemical, mining, building materials, metallurgy, environmental protection and other industries. In these industries, the proportion of raw materials and mixing precision requirements are very high, long-term reliance on artificial large differences, large errors and other issues, can not meet the demand for accurate and efficient operation. The weighing and mixing machine measuring and batching machine was born to solve this problem. Its advantages are as follows:
1, high degree of automation, to avoid the error and impact of manual operation, greatly improving production efficiency and production quality.
2, high precision, can be material composition analysis, measurement accuracy, to ensure the accuracy and stability of the formula in the production process.
3、Batch production, according to the actual needs of different quality levels of production, to meet the demand for differentiation.
4、Simple operation, easy to manage and maintain.
In short, weighing and mixing machine as one of the important equipment for automated production, in the economic production efficiency and environmental protection to reduce pollution have an irreplaceable role. In the future, with the continuous improvement of technology and expanding market demand, the scope of application and market prospects of this equipment will be more broad.