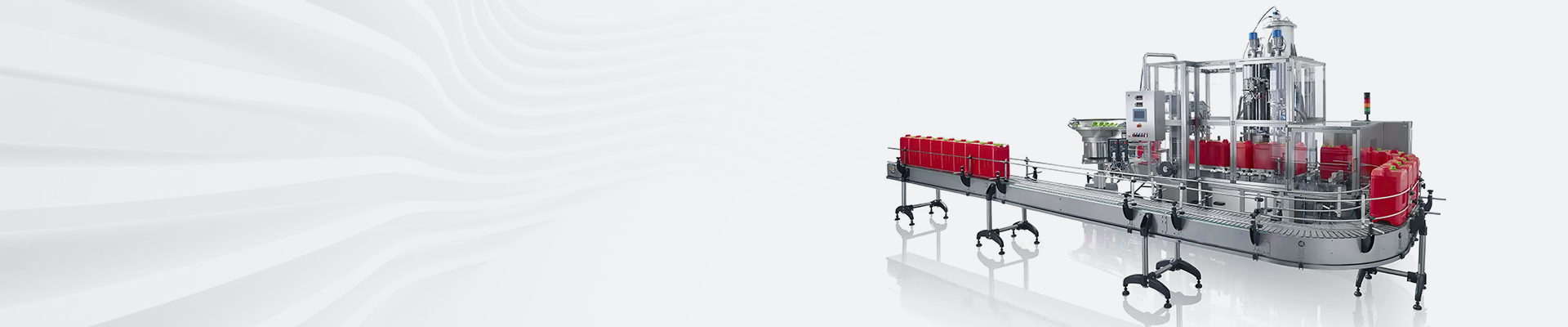
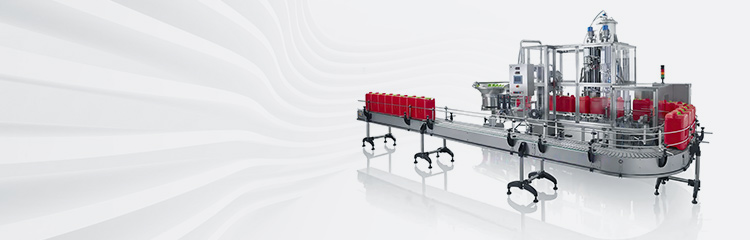

Summary:With the rapid development of electronic technology, weighing module technology, communication technology, computer and network technology, the automatic batching system uses real-time data collection and processing to avoid data falsification and unnecessary workload to obtain data and go to on-site evidence collection.
1 MODBUS bus dosage design
Automatic dosage system MODBUS adopts the ISO/OSI model of the physical layer, according to the link layer and application layer, MODBUS communication protocol, one of the most important features is the abolition of the traditional address coding, instead of coding the communication database. MODBUS bus data-oriented rather than node-oriented, the advantage of which is that it can be made within the network of nodes within the theoretically unlimited number of nodes, join and Reduce the equipment does not affect the work of the dosage. MODBUS bus communication maximum rate can reach 1Mb/s; transmission rate of 5kb/s when using twisted pair, the transmission distance up to 10km or so, and high reliability of data transmission. From the physical structure, MODBUS network belongs to the bus communication network, the system is different from the general network is:
(1) Unlike Ethernet and other networks for management and information processing, it is a network specialized in the field of automation;
(2) Its physical characteristics and network protocol characteristics more emphasis on industrial automation bottom detection and control;
(3) Using the latest technology and unique design, reliability and performance is much higher than the old field communication technology.
In the design should pay attention to the following points:
(1) In order to match the impedance, 120Ω terminating resistors should be added at both ends of the bus;
(2) MODBUS bus adapter card can make the PC easily connect with MODBUS bus, MODBUS bus adapter card is equipped with optoelectronic isolation, which can enhance the system to be used in harsh environments.
2 Process flow of dosing
Automatic feeding system is several kinds of raw coal from the reactor through the reactor feeder to the mixing tank frequency, when the material flows through the dosage mixing tank, by the dosage mixing tank for measurement. The whole weighing and batching system is mixed in a certain proportion under the control of computer and so on, and then weighed to get coke.
3 Overall structure of weighing and batching system
3.1 General structure
The weighing and batching system mainly consists of control room (computer monitoring unit) and metering control cabinet.
The control room of weighing and batching system is mainly responsible for parameter setting, data processing, information collection, working condition display, historical data query of each weighing monitor and frequency converter, and redundancy processing of preface equipment and programming of PLC according to the needs, and the control room is connected to the external MODBUS bus through the MODBUS bus adapter card, and the transmission medium is twisted pair, which is connected to the bus interface of each intelligent controller and frequency converter. The transmission medium is a twisted pair cable, which is connected to the bus interface of each intelligent controller and frequency converter. Each intelligent controller controls one dosage mixing tank.
3.2 Process control realization of dosage
There are usually two speed control methods for dosage: adjusting the reactor feeder to feed and adjusting the mixing tank inverter speed to feed. The coating agent weighing and dosage system adopts regulating reactor feeder to feed. The control process is mainly through the dosage mixing tank to the kettle feeder conveying materials for measurement. The weighing instrument receives the weighing signal sent by the weighing module and the speed signal sent by the speed module, which is converted into the totalized value and instantaneous flow rate after processing, and transmits the totalized value and the instantaneous flow rate signal to the industrial control machine (the upper computer), and the intelligent regulator, through the built-in PID regulator, automatically adjusts the PID value after comparing the operation and is used to regulate the frequency inverter, which then adjusts the rotational speed of the kettle feeder, and when the flow rate increases, it lowers the speed of the kettle feeder. When the flow rate increases, the speed of the reactor feeder will be reduced, and vice versa, the speed of the reactor feeder will be increased, so that the flow rate of several materials and the cumulative amount of phases will be kept in the set range, and then reliable product quality will be obtained.
The parameters and operation process of dosage can be set and monitored by the industrial control machine, and the value of PID can be modified manually, which is convenient to operate and reliable to control, and the whole dosage realizes a high degree of automation, forming a closed-loop control weighing and dosage system which is both relatively independent and interconnected.
3.3 Measuring control cabinet
Measuring control cabinet is mainly composed of programmable controller, intelligent controller and frequency converter. The system has monitoring parameters and alarm signals, configuration king basic I / O variables, for this selection of configuration king 256 points, its hardware configuration is as follows:
(1) PLC: OMRON CQM1H type, power supply unit model CQMl-PA203, CPU unit model CQMlH-CPU2l, input unit model CQMl-ID212, output unit model CQMl-QC212 and CPT programming software.
(2) Weighing controller: a company's intelligent weighing instrument, with fieldbus technology (MODBUS) interface, can be connected with the host computer, PLC or DCS, to conveniently realize multi-point control, data acquisition, interface expansion and communication with the host computer, to truly realize the digitization of the explosion-proof electronic scales for mixed tanks. Dual CPU hardware structure ensures the real-time performance of the instrument under any circumstances. Intelligent PID regulation, LCD display, Chinese character prompt information. Display information is rich, intuitive, and can simultaneously display the cumulative amount, instantaneous flow, etc..
(3) Frequency converter: FRNllCllS-4Cx produced by Fuji is used to regulate the speed of the reactor feeder, which has a very good on-site control effect, saves a lot of energy (about 70% of the working voltage) and reduces the pollution of the environment.
3.4 Control room
(1) Composition
Control room is actually an industrial control microcomputer, the basic configuration for the chassis IPC-610, 256M memory, 48x optical drive, 1.44M floppy drive, 43cm (17″) monitor, CPU interface card PCA-6179L, MODBUS bus adapter card and so on.
(2) Function
The control room is mainly used for centralized monitoring of the site conditions, data logging, parameter setting, timer storage, report printing and alarm prompting records, etc. The switch is placed in the control room, which allows start/stop operation of the site equipment; at the same time, the control room communicates with the dispatching room, transmitting the site conditions to the dispatching room, and the dispatching staff can intuitively observe the operating conditions of the equipment, real-time data and historical data, etc., during the production process, and transfer the data to the dispatching room, so that the dispatching staff can observe the operating conditions of the equipment, real-time data and historical data, etc., in a visual manner. The dispatchers can visually observe the operation status of the equipment, real-time data and historical data in the production process on the upper computer, and process, store and print these data. Through the collection and processing of these real-time data, it can fully improve the quality and production efficiency of the products of the paint factory, and realize the highly automated control by utilizing manpower and material resources.
4 dosage software design
Batching workstation software selection of the more popular "configuration software" as a development tool, making full use of WINDOWS features, graphical interface is better, can easily construct their own data acquisition system, in any case can be real-time transmission of information to the control room in real time, to facilitate the monitoring of the production situation. The dosage can communicate with intelligent controller and frequency converter: read data, send data; and communicate with PLC: read I/O status, send I/O commands; with alarm, fault query and print function; the configuration screen realistically reflects the real-time status; the engineering settings and formula input are diverse, and the ability to adapt to the working conditions is stronger; the software is equipped with different access privileges, which allows people with different privileges to operate different contents. The software is equipped with different access rights, which allows people with different rights to operate different contents. DDE technology is used to realize the data exchange between EXCEL and WINCC. Its software is mainly manifested in: dosage configuration, real-time database configuration, historical database configuration, loop configuration and report configuration.
4.1 Batching configuration
Batching configuration is carried out for the hardware structure of the whole weighing control system, which is the first step of the whole project configuration, selecting the type and number of on-site metering control cabinets to be put into operation, the respective station number and whether there is redundancy, etc., determining the station number of the operator station and setting the safety protection, and restricting the operator's operation authority and operation range.
4.2 Design of real-time database configuration
The real-time database is the source of information for centralized distribution and completes the configuration of all points to be monitored and controlled. According to the different types of point data, it is divided into analog input/output, switching input/output and calculation volume. Among them, the calculation quantity, i.e., the application program interface variables provided in the initialization acquisition program, is also analog quantity by nature. Different processing methods are adopted for different types of variables.
4.3 Design and Implementation of Loop Configuration Functions
Loop configuration can be carried out only after completing the database configuration, which is the key step of the centralized batching control system. It is mainly used for continuous process control, alarm detection and processing and determining input/output loops. Each record of the loop configuration database includes the necessary information of a complete loop, which is utilized to realize the control of batching. According to the different input/output of the loop configuration, it is divided into the mold-man-mold-out, mold-in-open-out and open-in-open-out circuits, and the reasonableness of its configuration directly affects the quality of control.
4.4 Historical database configuration design
The historical data is stored in the form of trend curve, and the data can be called up by inputting the time, which is used for accident analysis and report operation.
4.5 Realization of report configuration
The dosage report is divided into two types: periodic report and triggered list. The periodic report adopts the timer-driven method, which is used to print the operation records and statistical data in the production process, such as the Times, Shift Report, Daily Report and Monthly Report. Triggered lists are used to record the values of certain points before and after the occurrence of a specific time, and are used for accident or fault analysis.
4.6 Design of the Run Program
After dosage enters into running state, users should log in first and perform corresponding operation within their own authority, otherwise the monitoring interface will be locked in the dosage working state. Use the mouse to switch the screen, click "batching condition", "trend curve", "engineering parameters", "power control", "report" and "report". Clicking the buttons of "Batching Condition", "Trend Curve", "Engineering Parameters", "Power Control", "Report Management", etc., you can switch to different screens and carry out related operations.
5 Conclusion
Users through the weighing batching machine a few years after the use of the system to give a high evaluation: good operational reliability, simple operation, easy maintenance, high control accuracy, not only to ensure the quality of the product and yield, while overcoming the problem of environmental pollution, to create good economic benefits for the enterprise. The can be extended to a variety of bulk materials in accordance with the predetermined ratio of automatic continuous flow control of its batching occasions, such as petroleum, chemical industry, metallurgy, textiles, pharmaceuticals, tobacco, machining, building materials, municipal construction and so on.