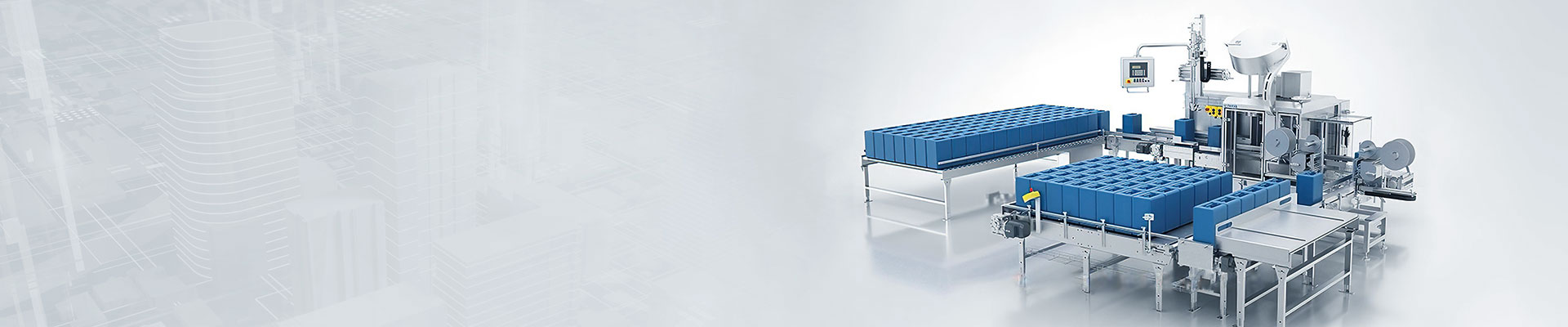
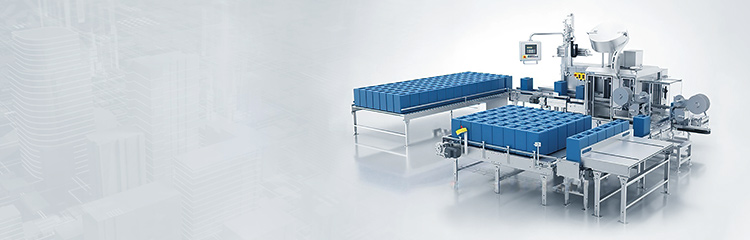
Pneumatic conveyor is mainly composed of weighing bin, weighing module, weighing instrument and calibration weight. The weighing module is uniformly installed around the middle and lower part of the weighing bin and directly supports the weighing bin. The load cell changes with the weight of the material in the load cell and outputs a signal that is linearly proportional to the weight of the material in the load cell.

The pneumatic conveying system uses the orifice jet of the conveyor to spray out high-speed air, which forms a negative pressure field relative to the positive pressure of the air in the pipe, generates suction, and sucks up different batches of catalyst and auxiliary powder to make it initially mixed. By using the multi-tube weighing mixing bin, through the air circulation, the final product is mixed several times to achieve different blending purposes and get the finished product to meet different needs.
Pneumatic conveying weighing mixing technology, its process flow is:
1) Product cooling conveying process
The high-temperature catalyst enters the cooling bin through the product discharge valve, and cools down after reverse indirect contact with the cooling water in the coil tube. At the same time, the positive pressure air generated by the product conveying fan flows through the conveyor, thus forming a negative pressure field in the throat part. The cooled catalyst is sucked into the conveyor through the product discharge valve with locking air work, accelerated by high-speed jet air, and enters the product pulse bag filter under the positive pressure pneumatic conveying, and the separated catalyst enters the product intermediate tank. The purified jet air is emptied.
The product pulse bag filter, the product intermediate tank, the product discharge valve and the conveyor can be operated in one rotation, or can be operated simultaneously in parallel.
(2) Product transportation and storage process
The catalyst entering the product intermediate tank enters the conveyor through the product discharge valve, while the positive pressure air generated by the product conveying fan flows through the conveyor, pumps the catalyst and sends it into the product pulse bag filter, the separated catalyst enters the product storage tank, and the purified jet air is emptied.
Product pulse bag filter, product storage tank and product discharge valve are alternate. Different batches of catalysts can be stored in different product storage tanks.
(3) auxiliary mixing transport process
Under the action of multi-tube weighing and mixing tube, the additives entering the auxiliary mixing bin reach the performance homogenization, enter the conveyor through the auxiliary unloading valve, while the positive pressure air generated by the auxiliary conveying fan flows through the conveyor, pumps the auxiliary agent and sends it into the auxiliary pulse bag filter, the separated auxiliary agent enters the auxiliary storage tank, and the purified jet air is emptied.
(4) The blending and conveying process of finished products
The catalyst entering the product storage tank enters the conveyor through the product discharge valve. The auxiliary into the auxiliary storage tank enters the conveyor through the auxiliary discharge valve; At the same time, the ambient air is pressurized by the product conveying fan and enters the conveyor and conveyor respectively. The catalyst and auxiliary are pumped and fed into the finished product pulse bag filter, the initial mixed "catalyst + auxiliary" finished powder enters the finished product mixing bin, and the purified jet air is emptied.
Different batches of catalysts stored separately in product tanks can be transported individually, in pairs, or simultaneously to the finished product blending bin for blending, depending on the desired finished product specifications.
The "catalyst + auxiliary" powder entering the finished product mixing bin can be mixed in a single warehouse, multiple mixing in a single warehouse, and multiple mixing in a double warehouse. Among them, single warehouse single mixing does not open the finished product conveying fan, under the action of multi-tube weighing mixing tube, the "catalyst + auxiliary" powder is only mixed once in the finished product mixing bin, that is, through the finished product discharge valve and the reversing valve; For multiple mixing in a single bin, the finished product conveying fan needs to be opened. Under the action of multi-tube weighing mixing pipe, the powder of "catalyst + auxiliary agent" is mixed in the finished product mixing bin respectively, and enters the corresponding conveyor through the corresponding finished product discharge valve. At the same time, the ambient air is pressurized by the finished product conveying fan and enters the conveyor respectively. The pumped "catalyst + auxiliary" powder is respectively sent into the finished product pulse bag filter, and the separated powder is mixed again into the finished product mixing bin, which can be cycled several times until the performance uniformity is achieved. The finished product mixing bin can be operated in rotation, or simultaneously in parallel; Double-bin multiple mixing needs to open the finished product conveying fan. Under the action of multi-tube weighing mixing pipe, the powder of "catalyst + auxiliary agent" is mixed in the finished product mixing bin and enters the conveyor through the finished product discharge valve. Meanwhile, the ambient air is pressurized by the finished product conveying fan and enters the conveyor. The separated powder goes into the finished product mixing bin for mixing again. So that the finished product mixing bin and series, the powder can be recycled several times between the two bins.