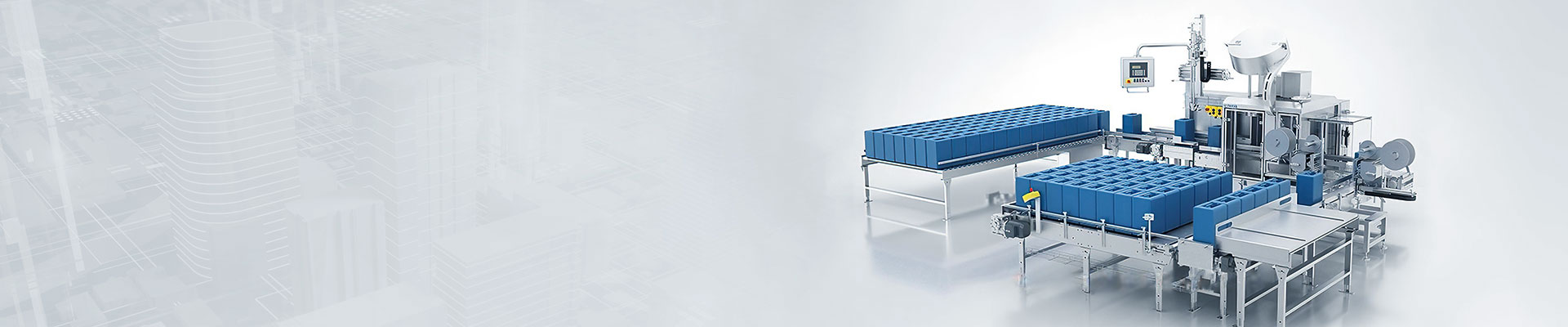
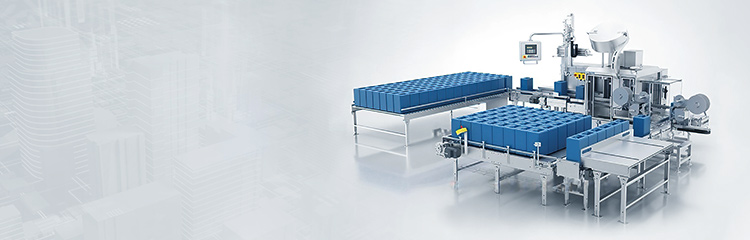
The batching production line has multi-level feed speed control in each screw ration feeder, the screw feed port is equipped with pneumatic valve to control the precise feed, and some feeding devices adopt multi-level vibration feeder and micro-scale. In order to control the influence of the change of bin pressure on the batching accuracy, the batching has corresponding interlock control relationship with the automatic feeding of the above bin. In addition to the FTA module itself integrated switching I/O points and a 4-20mA analog output function, you can easily achieve this more complex weighing ingredients application.

The feeding system is composed of Roots blower unit, meaning feed pipe and a number of branch feed pipes, pneumatic two-branch reversing valve (hereinafter referred to as branch valve) and a number of cyclone separators. There is a backup fan in the fan, and each Roots blower unit includes a Roots blower, a typhoon electromechanical machine and a fan control cabinet, whose task is to generate compressed air flow required for pneumatic conveying. The fan outlet is connected to one end of the mixing chamber, and the total material delivery pipe is connected to the other end of the mixing chamber. The feeding system and part of the fan unit and the total feed pipe can be installed in the raw material warehouse. The total feed pipe from the raw material warehouse is connected with an independent branch valve, which can form two branch feed pipes respectively to two workshops. Similarly, n+1 branch feed pipes can be formed with n branch valves, and these branch pipes are equipped with 1 branch valve at the location (hopper) of each extruder in the workshop. When selected to feed to a dosing machine, the relevant branch valve is played in the corresponding direction, so that the feed channel is unimpeded, the material can only lead to the dosing machine and can not go to other locations, so that the fan will mix the air mixture in the mixing chamber through all links of the feed channel to blow to the corresponding cyclone separator, after separation, the material reaches the corresponding dosing machine hopper.
Because the volume of the barrel mixing chamber is limited, and there is no agitator in it, the raw materials from each Feeder to the mixing chamber are blown away directly without stirring, and while feeding, they are transported. Although the raw materials are not stirred in the distribution process, the clever design method makes the raw materials go through the mixing, the mixing of turbulence in the blowing process, and the random mixing when the raw materials fall into the hopper of the dosing machine, the uniformity fully meets the requirements. When it is necessary to feed the material for a dosing machine, it is not necessary to determine the preparation amount in advance. In the process of matching and sending, the system depends on the specific situation. If the hopper is full or there is an urgent task, the distribution can be stopped at any time.
RS485 fieldbus is used in the physical layer, and the transmission medium is hung on the bus with five types of twisted pair cables. The sites that can communicate with each other include Advantech IPC and a number of self-developed intelligent measurement and control modules, which are connected together by fieldbus, mainly for the detection, control and network communication of local field equipment. The software of upper computer includes main control program, man-machine Put interface program, task scheduling program, network communication program and various subprograms. Limited by space, only the design idea of the master control program is introduced. The main control program is a real-time program with complex structure, and its overall control method is as follows: the main control computer obtains the level status of all the batchers collected by the measurement and control module of the batching machine through the network, and generates a dynamic task table that can reflect the requirements and priorities of each batching machine according to the level status and other related factors. According to this task table, the system further completes the feeding of each batching machine according to priority.
When the system decides to feed a extrusion dosing machine, the main control machine first issues an order to the fan measurement and control module to start the fan. At the same time, the corresponding valve opening and closing commands are issued to the measurement and control module of each batching machine and the branch valve measurement and control module, and the valve opening and closing are confirmed in place to ensure that the channel of the corresponding batching machine is smooth, and then the formula set by the operator for the extruder is removed in advance, and the feeding speed of each feeder is calculated according to the proportion of the formula, and sent to the measurement and control module of each feeder. Then issue the command to start the feeder and start the feeder. The measuring and control module of each feeder controls each feeder and simultaneously feeds the mixing chamber according to their respective feeding speed. During this period, the master computer counts the blanking time, and obtains the running status of the blanking device collected by the blanking device measurement and control module. When the dosage reaches the requirement, it sends commands to each blanking device measurement and control module to stop blanking, and then completes the batching task.