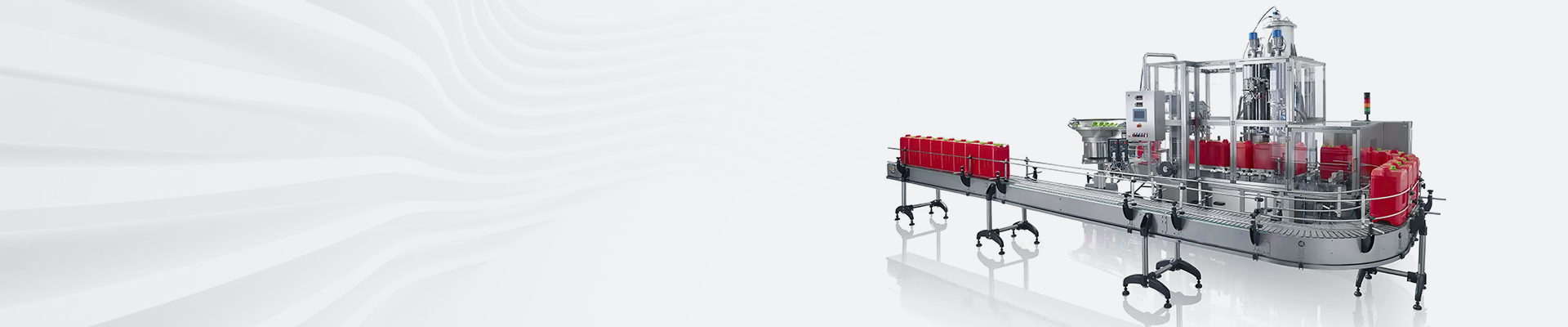
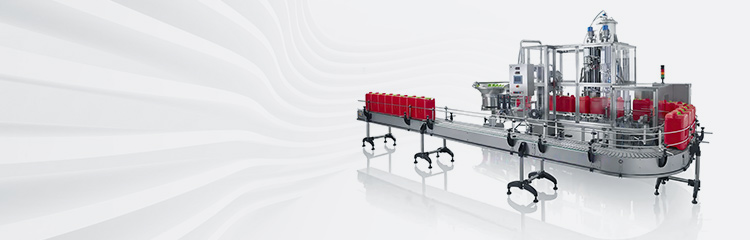

Summary:According to the characteristics of the blast furnace feeding system, a hopper scale is used for static measurement of bulk materials, and a fully suspended belt scale is used for dynamic measurement of wet powdery materials.The weighing module adopts S-type shear type that can resist lateral impact force, and a linear error compensation resistor is added.The belt scale adopts frequency conversion speed regulation, and the main and slave wheels are cold-glued with herringbone groove anti-slip rubber and other methods.Double-spiral blades are used for the hopper scale and feeder and are slightly raised, conical buffers are added to the hopper to prevent material collapse, fast and slow dual-speed feeding are used to reduce impact, and fieldbus is used as the control system.The actual project proves that the design greatly improves the accuracy, real-time and reliability of blast furnace loading.
Introduction
At present, one of the most common smelting methods in many large and medium-sized pyrometallurgical smelting enterprises in China is the closed blast furnace smelting method, referred to as blast furnace smelting method. It is widely used in the smelting of iron, copper, lead, copper, antimony and other metals. However, due to the harsh environment of the blast furnace smelting site, the feeding accuracy of the blast furnace feeding system has not been high, which seriously affects the accuracy of the feeding system automation, resulting in the production of blast furnace slag content is too high, the straight yield is low, the mouth of the furnace material surface is not even, the slag type is not stable, the dead furnace accidents, which seriously affects the enterprise's economic efficiency. As most smelting enterprises are often tens of thousands, hundreds of thousands of tons of production materials, and even millions, tens of millions of tons of theory. Charging accuracy of every 1%, will bring hundreds of thousands, millions and even tens of millions of dollars of economic benefits to the enterprise. Therefore, vigorously improve the feeding accuracy of the closed blast furnace, reduce the production cost of pyrometallurgical smelting, metallurgical and scientific and technological workers to chase the ideal.
In the blast furnace smelting, the most representative is the blast furnace sintering, all known as closed blast furnace sintering. The so-called blast furnace sintering is a kind of pyrometallurgical smelting technology that mixes raw materials such as metal ore, coke, quartzite, sulfurous iron ore, converter slag and so on, and adds them to the closed blast furnace for rough smelting. Among them, the metal ore is wet powder, and several others are 20~100mm lumps. Blast furnace sintering site is not only dusty, smoke, vibration, but also due to the variety of materials thrown into the dry and wet different types of materials, material type difference and so on, resulting in the feeding accuracy has been hovering between +3% to ± 6%, seriously restricting the economic and social benefits of enterprises.
2 dynamic + static feeding new model
2.1 dynamic + static feeding mode of the overall program
Examination of domestic and foreign copper smelting enterprises, large-scale enterprises mostly use belt weighing or nuclear scales and other dynamic weighing tools for batch feeding, tens of thousands of tons of production below the small and medium-sized enterprises mostly use hopper scales and other static feeding tools. The main advantage and disadvantage between dynamic and static is that the dynamic scale weighing capacity, measurement speed, very suitable for large-scale industrial production, but its measurement accuracy and feeding accuracy due to the "belt effect", in the daily production can only reach the error of +3% or so. The static measurement of the hopper scales, etc., weighing the material is at rest, measurement accuracy is very high, the same level of scale should be ten times higher than the dynamic scale of measurement accuracy, but its biggest problem is not high weighing capacity, and requires that the material can not have too much viscosity.
Analyze the five kinds of materials of the blast furnace, four kinds of lumps, a wet powder, which is used alone in the measurement of which there is a big problem. Through the experiments of field production, this design gives a new type of automatic feeding mode of the blast furnace: change to static feeding mode + dynamic feeding mode combined with a new feeding program, that is, four kinds of lumpy materials quartzite, coke, sulfurous iron ore, converter slag using static measurement, metal ore using dynamic measurement.
Static metering mode because of its weighing is in a static state, measurement accuracy is very high, the general operating error between +1 ~ 2%. Because of the intermittent nature of the measurement process, the interval and the requirements of the material particle size and humidity, the measurement capacity is not high. For this reason we chose a hopper scale with three hanging sensors. In view of the problem of low measuring capacity of the hopper scale, from the hopper structure, feeding mode, control equipment and other aspects of improvement, can make each hopper feeding capacity up to 60th, can fully meet the requirements of medium and large copper smelting enterprises. Blast furnace feeding site is narrow, the hopper scale occupies less lateral space, is indeed one of the most ideal measuring instruments.
For metal ore due to its high humidity, small particle size, poor fluidity with more material, so it is difficult to use static measurement of hopper scales, only to choose the dynamic measurement scale. Dynamic measurement of the biggest problem for the "belt effect", that is, with the material belt tension, deflection, vibration, impact, etc. on the measurement of the accuracy of the impact, for which people have thought of a lot of ways, but are not ideal. So what type of dynamic weighing scale to choose the best has become the key to the problem?3.
2.2 Selection of dynamic full suspension belt scale
Dynamic measurement of the main belt weighing measurement and nuclear scale measurement, etc., the two weighing principle is different, its advantages and disadvantages and applicability are not the same.
Nucleus scale dynamic measurement was produced in the late 1980s, but also popular at home and abroad. Its weighing according to the use of materials on the absorption of nuclear rays and the amount of material related to the principle of design. He compared to the belt weighing, can effectively overcome the "belt effect" and other environmental factors.
A copper plant six million tons of blast furnace sintering, initially all the use of nuclear scales on the material. However, because the nuclear scale is measured through the indirect way of mass flow, subject to the limitations of its measurement principle, the specific gravity of the material, shape, particle size, etc. has a greater impact on the measurement of accuracy, especially in the blast furnace smelting conditions, measurement accuracy is difficult to meet the requirements of the general error of +4 ~ 6%. Coupled with the nuclear scale with nuclear radiation, not suitable for installation in more personnel occasions. Therefore, the blast furnace sintering to abandon the original nuclear scale feeding method has become inevitable.
Blast furnace sintering dynamic feeding selection of belt scale is the only way. But what kind of belt weighing, in order to maximize the existing conditions to minimize the "belt effect" and other impact? Throughout the domestic and foreign belt weighing type, according to its mechanical (scale frame) structure form the main inertia type, cantilever type, the whole machine type and intermittent feeding type and so on. But at present, the practical feeding belt scale is still the whole machine type and cantilever type two mechanical structure form as the mainstream.
Cantilever feeding belt scale of the whole scale body by the ring transport belt main driving wheel, from the driving wheel, support frame, lever (scale frame) load cell and so on. The material is dropped near the supporting reed and the ring conveyor belt transports the material towards the weighing module. During transportation, the gravity of the material will act on the weighing module located under the scale frame. The load cell converts the gravitational force of the material into a signal that is sent to the subsequent instrumentation. Since the entire frame can be rotated in trace amounts around the pivot point of the supporting reed, while the load cell is supported on the same base. This is why it is called a cantilevered belt scale. The advantages of this form of mechanical structure are: only one sensor, simple structure, small size, the force on the sensor by the belt tension is less affected. But its disadvantages are: uneven thickness of the transport belt, the active wheel and other roller dynamic balance error, changes in the drop point, in the state of speed control changes in the material layer will have a non-negligible impact on the measurement and control accuracy of the system. Therefore, its also not our choice.
Finally, we will study the whole machine type feeding belt scale. In the whole machine type feeding belt scale and to full suspension belt scale performance is the best. He is mainly composed of four parts: full suspension weighing bridge, speed sensor, digital converter, totalizer. The structure of the scale body is four parallel weighing modules on two beams, and the weighing bridge provides full support. Since the weight on the measuring section is fully supported by the four suspended load cells, there are no problems with lever balancing in scales such as cantilever type, which has many advantages. Mainly: the change of the drop point has no effect on the weighing accuracy; no need to carry out frequent inspections of the main driving wheel, supporting rollers, from the driving wheel, the dynamic balancing error of the rollers, will not have too great an impact on the weighing accuracy; belt scales can be convenient to work in a constant-speed loading mode, but also can be convenient to work in the speed mode of work; reasonable structure, high accuracy, multi-torque weighing structure, accuracy is higher than that of the single- or double-torque weighing structure of the belt scales. Multi-roller weighing structure, the accuracy is higher than single or double roller weighing structure of the belt scale.
From the above analysis, it can be seen that the advantages of the full suspension machine type belt scale are very obvious, from the structure to the principle are very reasonable. And then by some enterprises of the actual measurement of the application, but also proved its superior performance. Therefore, in the large tonnage of the blast furnace sintering, metal ore dynamic feeding measurement, choose the full suspension belt weighing is currently the best program.
3 to ensure and improve the dynamic and static feeding new program feeding accuracy methods
Blast furnace feeding accuracy, depending on a number of links and factors, but at present the most critical and most difficult to overcome is: the problem of poor metering accuracy of the feeding scale. This design adopts the static measurement method + dynamic measurement method combined with the new feeding measurement program, so that four kinds of lumpy materials quartzite, coke, converter slag using static measurement of the hopper scales, two metal ore scales (a spare) using the full suspension of the belt weigher. In the overall program to solve this major problem, but in terms of specific details, there are many elements to be studied in order to ensure that the advantages of this new model is maximized to further improve the accuracy of the blast furnace feeding.
3.1 Improve the accuracy of static metering hopper feeding method hopper scale feeding mode, a variety of materials are stored in different silos, silo feeding is generally used in the form of electric vibration feeding, spiral feeding or star feeding. Measurement is generally used to measure the bin, and equipped with a pressure or pull-type gravity sensor for force conversion, the signal is amplified by the secondary instrumentation access to the PLC or FCS, etc. to complete the measurement. In some applications with wide time requirements, a measuring trolley can be used for uniform measurement, measuring trolley running along the track, positioned in turn to the bin under the proportion of material dosing. Hopper scale error sources are mainly static error and dynamic error, 3.1.1 hopper scale static error solution
Static error refers to the weighing accuracy of the weighing part of the feeding system in the non-production state. It depends on the design of the hopper, the accuracy and linearity of the sensor, the consistency of all the sensors on the same hopper and whether the installation of the sensor is reasonable and other factors.
(1) Selection of transducers
The more consistent the performance of several sensors on each hopper, the better. Selection of sensors may not be able to buy the performance of the same, it is necessary to compensate. Compensation method is as follows: in the weighing hopper (empty hopper) after installation, first carefully adjust the force of each sensor, try to make it uniform, and then measure the output of each load cell. If the output of a load cell is low, add a few hundred KΩ resistance between the input of the sensor, the resistance value should be carefully adjusted so that the output of the sensor and other sensors the same. On the contrary, if the output is too high, then add a resistor between the outputs, the same adjustment method as before. Linearity of the load cell on the static accuracy of the impact is also very large, in the procurement of sensors must be noted that the sensor linearity error should be smaller than the required static accuracy.
(2) sensor installation
Hopper scales using three load cells hanging hopper. Installation of the hopper should try to make each sensor force uniform. The sum of the load cell ratings should be greater than 50% of the maximum load of the system. Ideally, the best results are obtained when each load cell is evenly loaded. In practice, the material laid in the weighing hopper can not be completely uniform, the internal resistance of the sensor U is the output voltage after the force, Au is one of the sensors due to uneven force and the amount of change, "is the analog part of the analog input resistance of the instrument, the use of iterative calculation of instrumentation to obtain the signal voltage between the two points of the a, b is (U + Δw3). Therefore, when using transducers in parallel, as long as the sensitivity, internal resistance and linearity of the three transducers are the same, even if the transducers are slightly unevenly loaded, the weighing result is still accurate.
Tensile transducer in the installation, the upper and lower are connected by hook and loop, so that it is free to hang, not subject to any horizontal torsion and lateral force constraints, in particular, the use of universal hook is the most ideal.
3.1.2 Hopper scale dynamic error
This error, also called the working error of the feeding scale, refers to the error between the weighing value and the given value of the formula when the feeding scale is carrying material. The dynamic error of the hopper scale and the solution are mainly the following.
(1) Feeding error
Feeding error is mainly due to the feeder did not stop feeding at the right time and produce. On the one hand, you can use fast and slow double-speed feeding mode, the first fast feed, to 90% of the amount of material and then slow, in order to achieve the same amount of material each time. And each time after the material must be automatically cleared. On the other hand, the vertical distance between the feeder outlet and the weighing hopper is as small as possible, so as to reduce the height of the falling material, that is, to reduce the "air material column". At the same time, in the feeding process, try to make all the feeding ports near the center of the weighing hopper arrangement, try to use the first with a large amount of material, so as to quickly increase the height of the material surface in the scale, reduce the impact of feeding and material eccentricity error.
(2) Material collapse error
The collapse of the accidental nature of the microcomputer's adaptive function is sometimes difficult to make the correct judgment, will also bring this batch of error to the next batch. Control of this error, first of all, the feeder outlet near the use of double screw blades, to increase the blade constraint surface and binding force. Secondly, the stranded cage blade near the outlet is 60~80mm away from the outlet, so as to ensure that the material out of the outlet has a sloping surface and is not easy to collapse. Thirdly, you can make the feeder outlet slightly elevated, so that it has a 3°~5° elevation angle, using gravity to control the collapse of the material.
(3) Impact error
Feeder in the material into the hopper always has a certain speed, falling into the hopper there is always a certain impact, this impact and with different materials, feeding the different amounts of different feeding order and change, which will also cause a certain amount of error. In the actual control process, the first is to add a buffer in the weighing hopper, commonly used is a cone-type bulk feeder. First, it can reduce the impact, and secondly, it can make the material evenly distributed in the weighing bucket. The second is to increase the self-recognition ability of the computer software of the feeding scale to filter out the impact force and improve the stability of the feeding system.
3.2 Methods to improve the accuracy of the feeding measurement of the belt scale
3.2.1 Selection and connection of weighing module
Weighing module is likened to the heart of the electronic weigher, and its performance largely determines the accuracy and stability of the electronic weigher. The sensor of full suspension belt weigher should be selected according to the actual load, and the total load is more than 10~20% of the rated load.
When the choice is too large, it will cause the signal space is too narrow, the signal-to-noise ratio is small, resulting in poor measurement accuracy, fluctuations and other consequences. The design selects S-type shear stress sensor, which can well resist lateral impact. The connection between the sensor and the scale frame adopts universal joint bearing coupling, which can effectively eliminate the impact of bias load. Restricted by the site environment and installation means, it is very easy to cause the four sensors are not balanced, the choice of sensitivity mv/v consistent sensors or by adjusting the sensitivity potentiometer to make it consistent, in order to ensure that the measurement of partial load will not be affected.
3.2.2 Limit device
Limit device, also known as the top wire, in the dynamic measurement of limit device should be the main active limit. In this regard, the design of two pairs of lever-type limit devices with joint bearings, used in pairs, so that the scale frame will not run off and affect the accuracy of measurement.
3.2.3 The effect of belt sticking on the accuracy of the dosage system.
Transportation of materials with high humidity, the belt sticky material on the measurement of the impact is very large, especially in winter. Such as a metal mine belt scale to 0.60m / s speed no-load running two laps total 58S, due to belt sticking material, skipping 151 words, that is, 151kg. so the belt sticking material may sometimes become the largest source of error. Eliminate the method is, can be installed in front of the main wheel of the old belt made of adjustable scraping plate to remove the sticky material.
3.2.4 Frequency converter speed control system
The traditional slip motor speed control in the low-speed characteristics of poor, low efficiency; the use of the site of the external working environment is very poor, a lot of industrial dust, the dust is easy to enter the slip motor inside and wear and tear, jamming and other phenomena, maintenance, maintenance trouble, resulting in a lot of work failures, affecting normal production. According to the information and the use of site conditions, the design of programmable controllers to control the frequency converter speed control system to replace the old slip speed control with stepless variable frequency control.
At the same time, PLC-controlled frequency converter speed control device, the use of the whole machine type synchronous double speed frequency conversion method of feeding, so that the lower material layer to maintain the same thickness, the location of the falling material in the same part of the material when falling on the belt impact force is always equal, further reducing the impact of the belt effect.
3.2.5 Speed measuring device
The FMP (pulse waveform output) in the inverter replaces the speed sensor. In the absence of belt slippage, both values are identical. For this reason, the herringbone grooved rubber plate is cold glued on the master and follower pulleys and a drum roller is used to increase the friction coefficient between the roller and the tape, thus effectively preventing the belt from running out of alignment, and the test shows that the effect is good.
3.3 Control of Feeding System Error
Feeding system error mainly refers to the error caused by the computer's software can't completely actual correct response to the feeding situation.
3.3.1 Environmental error
Mainly mechanical vibration and electromagnetic interference. Due to mechanical vibration and electromagnetic interference, the feeding system is unstable, so that the sensor collects false data. When designing and installing, the feeding primary system should be as far away as possible from equipment with large vibration, such as granulators and fans. Stay away from strong electromagnetic field equipment, and do a good job of preventing electromagnetic field interference shielding measures and hardware and software filtering. For the site such as dust, smoke, humidity, high temperature and noise and other influences, should be configured according to the site-specific configuration of the relevant protective devices, and do a variety of daily regular maintenance work.
3.3.2 System law of error control
The above will be a variety of situations individually analyzed. However, in the actual production process, a variety of errors in the joint role, and is the influence of each other, the comprehensive manifestation. The most important point is that a variety of errors is only a link in the final error, the final error is a comprehensive response to a variety of errors, is often a link in the highest embodiment, just as the chain, its total capacity is always a weak link in the chain of embodiment. So in the pursuit of the minimum value of each error-producing factors as far as possible, more attention should be paid to the optimal combination of the system, all aspects of the system as far as possible to take into account at the same time, to find the optimal program, which is more important than any single work back.3.4 Feeding system of field bus control of a copper plant with an annual output of 60,000 tons of copper in the closed blast furnace sintering batching production line. It has three sets of blast furnace melting systems. Each system of measuring instruments selected mainly by two belt weighers and four hopper scales and other automatic control equipment. The total number of control points in the whole plant is about 1,500, accomplishing more than 300 motor start-stop and accident alarms; more than 120 thermal measurement points, recording more than 80 points and trending more than 50 points. In order to ensure the reliability and stability of the system, the blast furnace sintering system uses advanced fieldbus control technology.
4 Implementation Summary
This design program in March 2008 in an enterprise 60,000 tons of crude copper production line began construction and transformation, operation in 2008 so far, through the online debugging and the use of the user site to see the reliability of the system is good, easy to operate, easy to maintain, the system's accuracy is high, smooth operation, to meet the design requirements, the control function and performance are compared with the original system has improved greatly. Comparison of statistical analysis of the production data for many times: hopper scales stand-alone measurement accuracy of +0.5%, belt scales stand-alone measurement accuracy of +1.0%, feeding accuracy has reached +1.5%, the blast furnace furnace condition is stable, feeding process is smooth operation and maintenance is easy. It can be seen that the design program is advanced, is successful, and has reached the domestic advanced level. And the economic benefits are obvious, very popularization value.