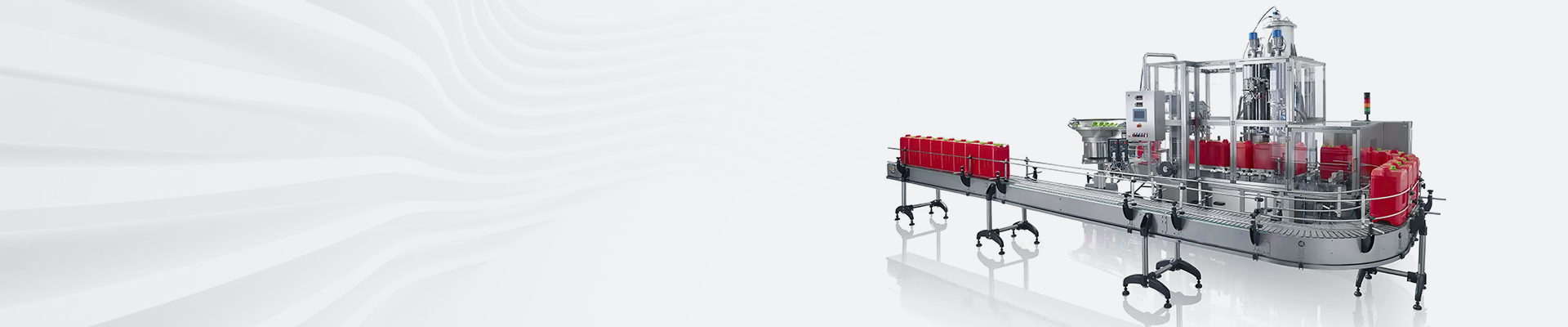
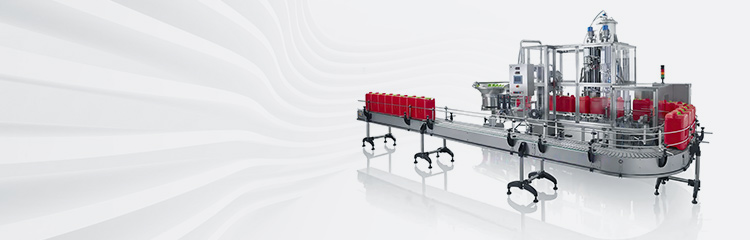

Summary:The weighing and filling system is an automatic quantitative metering equipment that automatically divides a large amount of bulk liquid materials into predetermined small loads through a weighing module for quantitative container packaging.
Electronic scale measurement is currently aseptic filling system commonly used measurement, how to fill the amount of accurate real-time read into the PLC can be used in a variety of ways. In this paper, the weighing module SIWAREXWP231 is used to replace the traditional weighing instrument, and the PLC internal bus is used to replace the analog signal transmission method. The traditional filling machine filling weight collection method, introduces the SIWAREXWP231 hardware lap method, PLC program design, weighing module parameter modification, the calibration method of electronic weighing, with an example to realize the weighing control system design based on SIWAREXWP231.
1 in the fruit and vegetable juice beverage aseptic filling industry, with the diversification of filling products, filling volume precision requirements, weighing and metering is increasingly becoming the main method of aseptic quantitative filling. Filling products that contain particles or the presence of uneven conductivity, flow rate instability and other factors will lead to a large error in flow meter metering. The use of electronic weighing measurement can effectively avoid the above shortcomings, can meet the aseptic quantitative filling of multiple varieties of products, greatly improving the filling accuracy.
Aseptic filling, usually used in the principle of automatic filling machine, filling containers pressurized in the dynamic worktable, the dynamic worktable through the load cell connected to the static worktable. As the filling volume increases, the load cell sensing principle is usually used in automatic filling machines, where the filling container is pressurized on a movable table and the movable table is connected to the static table via a load cell. The increase in filling volume deforms the load cell and transforms it into a resistance signal output. The resistance signal is detected and converted into a physical value of weight. The load cell is deformed and converted to a resistance signal output. The resistance signal is detected and converted to the physical value of the weight.
2 aseptic filling weight commonly used collection methods
Aseptic filling weighing measurement with resistance strain gauge load cell, commonly used hardware lap structure for the sensor resistance signal through the distributor matching and summing output to the weighing instrument, the weighing instrument will be transformed into a resistance signal weight value. At the same time, the weighing instrument will output the weight value through 4-20mA current signal to the analog input module of PLC, and PLC will use the collected weight value to carry out the logic control of the whole equipment. The weighing instrument has an IO control port for zeroing, tare and other operations.
This traditional model has the following disadvantages.
(1) More connection points in the electrical system.
(2) The analog signal collected by PLC can affect the accurate filling even if it is slightly disturbed;
(3) If a touch screen is integrated in the device, it is generally difficult to align the weight value displayed on the touch screen with the weight value displayed on the weighing instrument;
(4) The calibration and parameter setting of weight need to be carried out in the instrument, with a low degree of integration. Based on the above shortcomings of the traditional model, such as the use of Siemens weighing module WP231 can achieve more satisfactory results.
3 Siemens weighing module WP231 applications
3.1 Introduction of weighing module SIWAREXWP231
SIWAREXWP231 is a general-purpose weighing module suitable for most weighing measurement and force measurement applications. The compact module is designed for easy installation in S7-1200 PLC systems and can also operate independently from the CPU. The module can be connected to 4-wire and 6-wire load cells, with a measuring accuracy of 0.05%, a calibration scale of 3000, a resolution of 1 million, a sampling period of 10 ms, 4 digital inputs and 4 digital outputs, 1 analog output, Ethernet and RS485 communication interfaces, which allows easy modification of the touch screen, SIWATOOLV7 and third-party devices with MODBUSTCP. It can easily communicate with touch panel, SIWATOOLV7 software and third-party devices for MODBUSTCP/IP and MODBUSRTU.
3.2 Hardware connection of SIWAREXWP231 in weighing and filling system
The resistive signal output from the signal distributor is directly connected to the weighing module, and the weighing module WP231 is connected to the PLCCPU through an internal bus, avoiding the influence of interference during the transmission of the analog signal. the WP231 can be seamlessly integrated into the electrical system of the PLC and the touch screen, and can be used to perform calibrations, parameterizations, etc., for the weighing system, through the configuration in the touch screen.
3.3 Configuration of SIWAREX WP231 in Protherm Software
Take Siemens 1200 series PLC as an example to illustrate that WP231 is connected to CPU1214C through internal bus CPU is connected to touch screen through profnet protocol.
3.4 SIWAREXWP231 in the Botou software program design
Open the programming software and call the FB231 function block, which is the communication interface between the weighing module and the S7-1200. Pin ADDR: sets the starting address of the input address.68 The current weight of the weighing module WP231, the module status, the parameter settings, the status of the digital inputs and outputs and the analog outputs are stored in the background data block DB6.
3.5 SIWAREX WP231 parameter setting and calibration
The process values, status and parameters of the dosing module WP231 are stored in the background data block DB6 corresponding to the call to FB231. Among the parameters mainly applied in aseptic filling and weighing are the following.
PROCESSVAL1: current gross weight (net weight after tare); iCMDCODE: command code; boCMDTRIGGER: command trigger bit; DR3: calibration related parameter; DR10: load cell characteristic value.
The weight value of aseptic filling and weighing is stored in PROCESSVAL1, and the CPU only needs to address "left big bag weighing" SIODATA.PROCESSVAL1 to read the weight value for the metering control of the weighing and filling machine equipment.
PROCESSVAL1 can read the weight value for the weighing control of the weighing and filling machine equipment. Write the command code to the address "left big bag weighing" SCMD1iCMDCODE, and at the same time, trigger the command execution bit BOCMDTRIGGER to execute the calibration, clearing, tare and other weighing functions.
The electronic scale is calibrated by configuring the calibration interface in the touch screen. The buttons and I/O fields in the calibration interface correspond to the parameters and command codes. First write the necessary parameters DR3 and DR10. After entering the parameters of the electronic scale, click on Start Calibration to start the service mode of the WP231. With the scale empty, click Zero Calibration, place the calibration weight (or other known weight object) and click Weight Calibration. Click on End of Calibration to close the service mode of WP231 and the electronic scale completes the calibration easily.
During the working process of the liquid filling machine, the required filling volume can be set in the touch screen. After the filling volume reaches the set value, PLC carries out the control to stop filling.
4 Conclusion
Electronic scales with high metering accuracy, filling volume error does not depend on temperature, flow, product and other process parameters, is currently the main filling machine used in the measurement method. The use of Siemens weighing module SIWAREXWP231 instead of the traditional weighing instrumentation to reduce the susceptibility of analog signals to interference factors, the load cell signal more reliable collection to the PLC controller. At the same time, PLC, weighing unit and touch screen are seamlessly combined, which greatly improves the integration of the filling system, simplifies the electrical system and reduces the points of failure. Parameter modification, calibration and other operations of the weighing unit are integrated in the touch screen for easy operation. The fault information of the weighing module can be easily read into the control system, creating a hardware basis for remote diagnosis of the weighing system. The weighing module with powerful functions is widely used, which is conducive to the serialization and standardization of filling machine products. The cost of the weighing module is comparable to the cost of the mainstream weighing instruments in the market, which does not increase the overall cost of the weighing system.