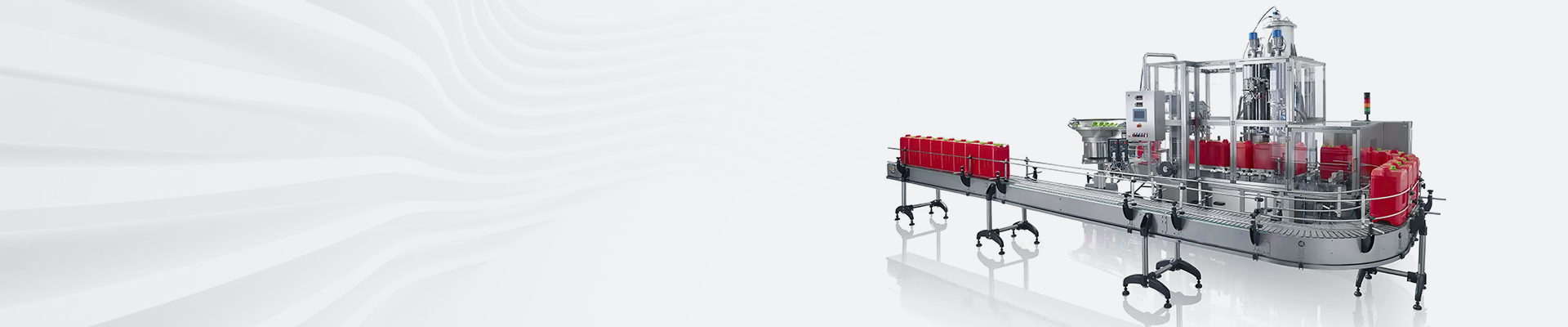
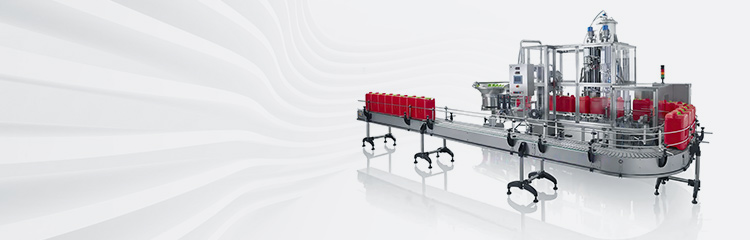

Summary:The baggage scale metering management system collects information such as airport ambient temperature and number of baggage through the weighing module, and transmits the information to the monitoring center to be processed into a time node and stored through the hybrid ZigBee-WLAN/Ethemet network, so as to realize the metering management.
With the vigorous development of China's aviation industry, the annual throughput of airports is getting bigger and bigger, and each flight needs a baggage scale, which leads to an increasing number of such vehicles. With the increase in the number of baggage scales, access to the vehicle service flights frame number, working time, mileage, baggage conveyance pieces of data information is also more and more, each baggage scale monitoring, management workload is also more and more large.
The existing domestic program is only for the airport special vehicle scheduling, and the monitoring of the working status of the airport vehicle is still in the blank stage. At present, the management mode of China's domestic airports for baggage scales is still through the ground staff's record results into the database, and then regularly settle the fees with the airlines. Such a management mode has great disadvantages, such as the inaccuracy of the personnel records and the inaccuracy of the data entered by the settlement center. Similarly, the existing foreign programs only monitor the location of the airport vehicles, but not the working status of the airport vehicles, so foreign airports are still in the exploratory stage of monitoring the service time and service volume of special vehicles.
In recent years, the application of Zigbee in airports mainly includes airport bird monitoring system, airport engine room environment collection data system and network perimeter alarm system, etc. 1. However, considering the narrow bandwidth of Zigbee gateway, short transmission distance and insufficient monitoring range, and there are both near-airplane and far-airplane positions in the airport apron, and the monitoring center has a large amount of data, which results in the bandwidth of the ZigBee network not being able to meet the requirements.
To this end, a ZigBee-WLAN/Ethernet-based airport baggage scale metering management system is proposed, which mainly realizes the precise positioning of the vehicle as well as the accurate metering and billing of the service time and service volume. Through the realization of this set of design solutions, can save manpower and material resources, improve the efficiency of the baggage scale, strengthen the airport on the baggage scale monitoring and management efforts, for the airport and airlines to provide a more accurate and convenient measurement management.
1 System overall design
The system is mainly composed of terminal nodes, coordinators, gateway nodes, airport production network and ground monitoring center. The terminal node data is managed and the vehicle is dispatched, i.e., the vehicle's running track is monitored and the collected data information is managed to provide data support for guaranteeing the flight normalization rate and statistical workload.
In order to realize the measurement of the baggage scale, it is necessary to monitor the start time and end time of its operation and the number of baggage transfer. This system defines the judgment method of starting work as follows: when the pressure weighing module monitors that the pressure value is greater than 9800N and the distance from the weighing module is greater than 3cm and less than 5cm, it determines that the baggage scale has contacted the cargo door of the aircraft and started to work, and takes the time that satisfies these two conditions as the starting time. When the pressure weighing module monitors that the pressure value is 0 and the value of the distance from the weighing module is greater than 5cm, it is determined that the baggage scale has ended its work, and the time that satisfies these two conditions at the same time is taken as the end time. The number of counters in the intermediate process is the number of passenger luggage. The service location judgment of the luggage scale mainly uses GPS positioning technology, through the GPS positioning information for comparison, to determine the vehicle for which flight service, and combined with the location information to determine the flight number of the service flight, so as to achieve the measurement of its operating time and the amount of work.
2.1 Hardware design of terminal node
The hardware design of the terminal node mainly consists of weighing module, ZigBee transceiver, identification module, positioning module and power module.
The function of the terminal node is to monitor and upload data on the location and working status of the baggage scale, and at the same time, receive the notification and scheduling information issued by the monitoring center called consists of the weighing module, the identity identifier, the positioning module, and the wireless communication module. The weighing module includes counting weighing module, pressure weighing module and distance weighing module. The counting sensor is installed at the top of the track to realize the counting of the number of passengers' luggage. The pressure weighing module is mounted on the four hydraulic cylinders' supporting angles, which is used to monitor the pressure of the cylinders' supporting angles to determine whether the vehicle starts to transfer the luggage. Distance sensors are mounted at the end of the track rubber hose to determine if the cushioning rubber hose at the top of the track is touching the aircraft cargo door.
The function of the coordinator is to realize the establishment, management, data command reception and forwarding of the ZigBee network. The role of the gateway node is to realize the mutual conversion of ZigBee protocol and airport production network protocol, which is distributed according to the transmission distance of the signal on the apron, parking space and other baggage weighing activities in the scope of the club to consider the special environment of the airport, the design of the Zigbee-WLAN/Ethernet hybrid network gateway, including the ZigBee to Ethernet module to achieve the airport near the aircraft position, terminal building The Zigbee-WLAN/Ethernet hybrid network gateway is designed, including ZigBee to Ethernet module to realize the network coverage in the near aircraft position and terminal building of the airport, and ZigBee to WLAN module to realize the network coverage in the distant aircraft position and the environment without wired network. Ground monitoring center for airport baggage scale operation
Combined with the actual situation of the baggage scale, it can be seen that the distance between the installation location of the distance weighing module and the pressure weighing module and the CC2531 processor installed in the driver's cab are far away from each other, so the 485 driver model MAX3082 is used to convert the distance information into serial data and transmit it via 485 twisted-pair cable over a long distance. The pressure weighing module comes with an internal AD converter, which converts analog to digital and transmits it to the serial port distributor over a long distance via the 485 driver. The serial port distributor synthesizes two serial data into one serial data and transmits it to CC253U via UART0.
The identification module is connected to the CC2531 via USB and is mainly responsible for the identification of the baggage scale staff. The positioning module is connected to the CC2531 via RS232 to determine the track of the luggage scale to ensure that the vehicle arrives at the service apron.
In order to determine the distance between the rubber tube at the top of the track and the cargo door of the aircraft, DLS-A15 laser distance measurement weighing module is installed at the top of the track. When the aircraft uses the "secondary docking" method to dock against the aircraft cargo door, the distance to the target can be determined by measuring the time it takes for the laser to travel to and from the target, and then converting the distance information into serial data and transmitting it remotely to the CC2531 processor. To determine the current operating environment of the baggage scale, a PT100 temperature weighing module is used to collect the temperature, and the analog signal is converted to a digital signal and transmitted to the CC2531 through the PO_1 port.
In order to count the number of baggage conveyed, the convective infrared metering module is installed in the middle of the track. When the passenger luggage passes through the infrared ray, the receiver can not receive the transmit signal, then the weighing module generates a pulse signal, which is transmitted to the CC2531 through the P0_0 port, and at the same time, the counter counts the number of transmissions. In order to determine whether the baggage scale starts to transmit baggage, it is necessary to use the NS-B type pressure weighing module to measure the information of the vehicle's cylinder bracing angle pressure. The 4 strain gauges of this pressure weighing module form a bridge, when the cylinder support angle produces pressure, the bridge forms a potential difference E, and after amplification by an amplifier, the analog signal is converted into a digital signal by the internal AD converter of the weighing module and the pressure information is sent to the CC2531 processor through the 485 driver.
2.2 Terminal node data acquisition software design
The terminal node data acquisition software design uses ZigBee network to network the terminal nodes.
After the device is powered on, the terminal node sends out a network request to join the ZigBee network. After successful network access, use timer T2 to collect position and weighing module information at 1s. The weighing module in the positioning module on the luggage scale collects coordinate information in real time and processes it into position information through the positioning algorithm, and it can determine whether the luggage scale arrives at the service apron through the position information comparison.
After arriving at the ramp, the terminal node sequentially collects pressure information, distance information, temperature information and the number of passenger luggage information. When the microprocessor receives the judgment that the pressure value of the cylinder bracing angle is greater than 9800N, the distance between the buffer rubber tube at the top of the track and the aircraft hatch is greater than 3cm and less than 5cm, and the counter value starts to increase, the terminal node collects data and sends it to the server. If no pressure change information, distance change information and counter number change information is received, the indicator light installed in the driver's cab will be on, and the staff will manually confirm whether to continue to collect the weighing module information through the buttons on the terminal.