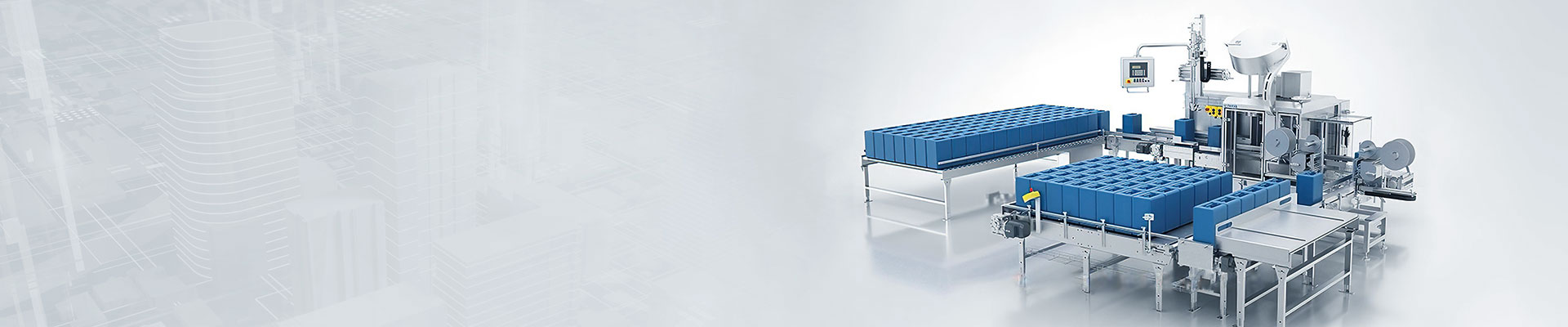
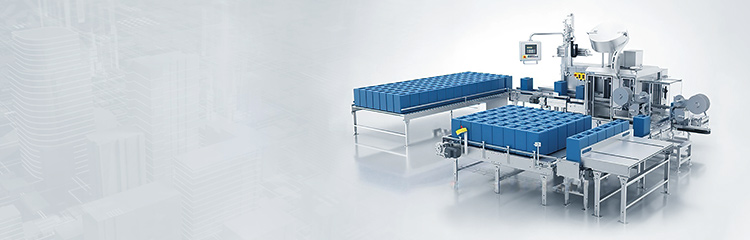
Temperature-insulated reaction kettle combines weighing sensor, load transfer device, installation connector and other components, and can be connected with various mechanical devices very conveniently. Automatic feeding control, automatic metering, PLC control, man-machine interface for data input and storage in the whole production process. Frequency converter is used to control the stirring speed, which can be set at will.

The Batching system of reaction kettle is suitable for petroleum, chemical industry and proportioning industry. The weighing control system is an integrated control system based on computer technology, control technology, communication technology and graphic display technology (that is, 4C technology), which connects the field control station, control management station, detection station, operation management station and engineer station distributed in the industrial site (nearby) through the communication network to jointly complete decentralized control and centralized operation and management.
Main functions of automatic feeding system:
1. The automatic feeding system can fully realize the management automation of all business links in chemical industry and other industries, and automatically monitor all work links of users, thus assisting user managers to conduct business processing more efficiently and accurately.
2. Based on the local area network environment, through the unified monitoring interface, the dynamic data of each monitoring environment are automatically collected, and based on these monitoring data, various reports and schedules are formed, which is convenient for business statistics and inquiry. The powerful query function can query user records, reports, etc. by ticket number, crane number, user code and car number. On this basis, the system will also form a complete business information feedback and supervision control mechanism, which will provide strong support for enterprises to carry out scientific management and decision-making.
3. Automatic distribution and centralized management function: it can realize automation of distribution process, ensure batching accuracy and improve production efficiency;
4, alarm protection function: can realize all kinds of fault alarm, as well as electrostatic spill protection, emergency stop protection;
5. Monitoring function: online monitoring the sending status of each crane position;
6. Ticket exchange and delivery: the filling bills can be customized and printed, and these bills can be stored. The methanol batching system has password recognition function;
7. Offline function: When the upper computer can't operate, it is convenient to switch to the on-site weighing instrument for manual batching;
8. Management function: accept the production data and production plans of superior management networks to arrange production, generate reports and purchase, sell and store systems;
9. Communication networking function: standard DDE and O interfaces are provided, and the adhesive batching system can communicate with DCS, ERP and other control and management systems conveniently.
Technical parameters:
Design volume: 50L-10000L (the volume can be designed as required).
Electric heating power: 6kw-700kw (depending on the volume of equipment and the technological requirements of materials).
Reaction temperature: normal temperature -300℃ or higher, depending on the working conditions.
Reaction pressure: -0.1-0.3Mpa.
Equipment material: SUS304 stainless steel, SUS321 stainless steel, SUS316L stainless steel or Q235-B carbon steel.
Mixing forms: paddle type, anchor paddle type, frame type, spiral belt type, turbine type, dispersed disc type, combined type, etc.
Heating methods: electric heating, steam heating and water bath heating.
Heat conducting medium: heat conducting oil, steam, hot water and electric heating.
Heat transfer structure: jacket type, outer semi-tube type and inner coil type.
Mixing speed: the selection of mixing speed depends on the need of mixing materials; Conventional liquid material polymerization reaction, rotating speed is 85r/min;; When the powder-containing material is mixed with liquid, it needs to achieve dispersion effect, and the rotation speed is 0-1500 r/min; The mixing of oil with liquid or two incompatible liquids needs to achieve emulsification effect, and the rotation speed is 0-2800 r/min.
Working principle: The reaction solvent can be put into the inner layer for stirring reaction, and the interlayer can be connected with different cold and heat sources (frozen liquid, hot water or hot oil) for circulating heating or cooling reaction. Through the interlayer of the reaction kettle, the constant temperature (high temperature or low temperature) hot-melt medium or cooling medium is injected to heat or cool the materials in the reaction kettle at constant temperature. At the same time, the stirring reaction can be carried out under normal pressure or negative pressure according to the use requirements. The materials react in the reaction kettle, and the evaporation and reflux of the reaction solution can be controlled. After the reaction, the materials can be discharged from the discharge port at the bottom of the kettle, which is very convenient to operate.