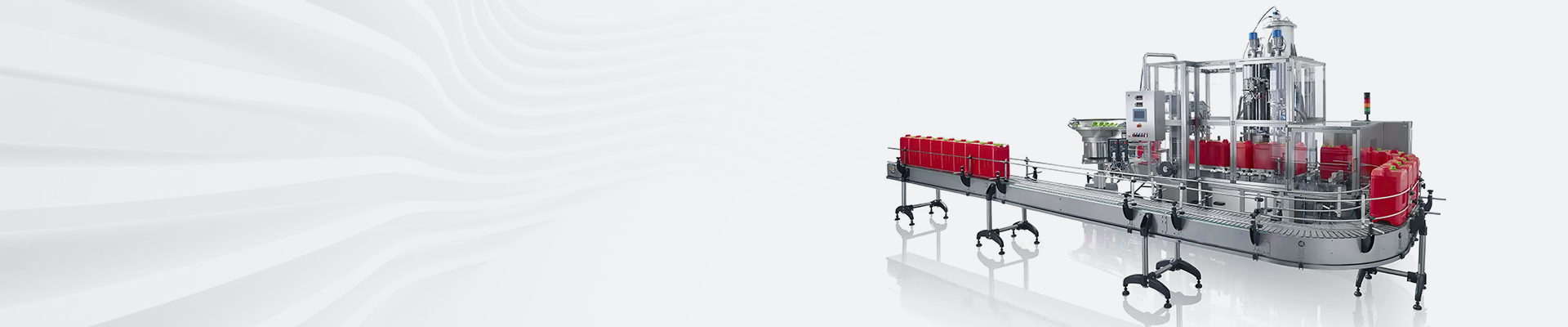
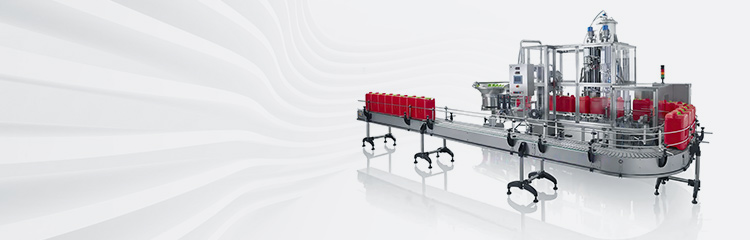

Summary:The batching system is based on the existing measurement and control equipment such as electronic belt scales, screw reamer pumps, nuclear scales, etc. The corresponding Lon Works nodes are connected to the inputs of these existing batching control equipment, and the non-LonWorks fieldbus equipment is integrated into the fieldbus to form a fieldbus-based control system. The nodes used here mainly include: PCLTA-10 adapter card and PC and connect to form the Lon Works network management and monitoring node; Lon Works/4-20mA conversion node will comply with the DDZ-Ⅲ standard analog signal 4-20mA control equipment integrated into the fieldbus; Lon Works/485/232 conversion node will be the digital interface control equipment integrated into the fieldbus; Lon Works/485/232 conversion node will be the digital interface control equipment integrated into the fieldbus; Lon Works/485/232 conversion node will be the digital interface control equipment integrated into the fieldbus. The Lon Works/485/232 converter node integrates digital interface control devices into the fieldbus; the monitoring and control of switching quantities is accomplished by the I/O modules of the Lon Works control node.
Dry powder batching control system is a kind of dry powdery construction aggregate, binder, and additives and other uniform mixing, with its scientific ratio, the use of modern advanced control equipment and technology, the establishment of diversified mortar proportioning library and online rapid response control unit is feasible and urgently needed. Take the electronic proportion library of dry powder as the input driving source, establish the rapid adaptive control center, which can quickly replace the production control process of dry powder products with different ratios and properties, and realize the production of dry powder. Through the analysis of the control volume and performance requirements for the powder flexible control center, the fieldbus technology-based networking scheme is determined. Fieldbus is used in industry between the field instrumentation and control room systems - a fully digital, two-way multi-station communication system. Is the process control technology, automation instrumentation technology, computer network technology, the three major technological development of the meeting point. The use of fieldbus to solve the following problems: measurement control unit, mixing control unit, the accuracy of the automatic error compensation unit, reliability, rapid response; equipment, a variety of parameters and state data acquisition and control information sent to a variety of state parameter expression and alarm processing; accident memory and trend analysis; high-performance, high-efficiency self-flowing storage device and mixing device.
1 Fieldbus system FCS
1.1 Overview of Fieldbus
In order to realize the information integration of the whole enterprise, realize comprehensive automation, and achieve the purpose of reliable, inexpensive and interoperable operation in the industrial field. Fieldbus control technology is considered an inevitable trend in the development of industrial control due to its great technical advantages, and will gradually replace the traditional PLC point-to-point wiring control method. Fieldbus technology is a set of bus technology, computer technology, communication technology, integrated circuit technology and intelligent sensing technology in a new control technology. Fieldbus is an application in the production site, field equipment, field equipment and control devices between the implementation of two-way, serial, multi-node communication communication network. It is a communication network suitable for industrial control requirements. Fieldbus puts the microprocessor into the on-site automatic control equipment, so that the equipment has the digital calculation and digital communication ability, which on the one hand improves the signal measurement, control and transmission precision, and at the same time creates the conditions for enriching the content of the control information and realizing the remote transmission. In the fieldbus environment, with the help of fieldbus network segments and other network segments with which there is a communication connection, it realizes off-site remote automatic control.
1.2 Classification and comparison of field buses
There are many types of fieldbus, according to the fieldbus application level will be divided into the following types: ① sensor bus the lowest level of the bus, only a small amount of data transmission. Such as ASI, Interbus-S and so on. ② device bus the most commonly used form of a bus, for intelligent devices to provide communication services, at this level, intelligent devices can perform a variety of functions to provide communication and diagnostic information services. This type of bus includes: CAN, DeviceNet, Lon Works, Profibus -DP and so on. ③ Workshop level bus equipment bus on the level, he supports the transmission of large amounts of data, but the transmission speed is slower, requiring higher performance of the device processor, some fieldbus technology has been able to directly support distributed control functions in the field equipment. This type of bus includes: FF, Profibus-PA, WorldFIP, Lon Works and so on. ④Control level bus is mainly oriented to the peer-to-peer communication of PLC, DCS controller and other high-level control devices, such as ControlNet. ⑤Enterprise level bus backbone network is for the service of enterprise affairs, and the main form is to run TCP/IP protocol on the basis of Ethernet.
1.3 LON WORKS
Lon Works is used to develop a complete technical platform for monitoring and control network system, and has all the characteristics of fieldbus technology. the Lon Words network system consists of intelligent nodes, each of which can have various types of I/O functions, and the nodes can communicate with each other through different transmission mediums, and comply with the 7-layer model of ISO/OSI, which is known as a universal control network.
Lon Works supports interconnection and interoperability with other protocols and networks; ECHELON provides software and hardware that can be embedded into the product so that Lon Works applications can be run on non-Neu-ron chipset hosts, and any micro-controller, PC, workstation, or computer can be used as a node in a Lon Works network to communicate with other nodes. Communication. The Neu-ron chip handles the full range of field interconnections, as well as field tasks such as field sensors, actuator actions, and digital logic operations.Lon Talk is a subset of the OSI reference model for field object-oriented applications. It covers a wider range of functions than fieldbus has traditionally recommended, supporting multiple media and large networks. This provides a global solution for the integration of measurement, control, and management in factory manufacturing automation, and all can be interconnected with the production management level through the neuron chip cured with Lon Talk protocol. In addition, Lon Works bus development system supports a variety of topologies, the choice of different transceivers can constitute a star, ring, tree or hybrid structure; and addressing is resolved by the protocol, so that the field interconnection is more flexible.
2 dry powder batching control system
2.1 Main controlled objects
1) Silo control valve: cement silo downstream port control valve, lime powder silo downstream port control valve, quartz sand downstream port control valve, fly ash downstream port control valve, additives downstream port control valve;
2) material level monitor: cement silo material level meter, lime silo material level meter, quartz sand material level meter, fly ash material level meter, additive material level meter; 3) feed valve: cement silo inlet control valve, lime silo inlet control valve, quartz sand inlet control valve, fly ash inlet control valve, additive inlet control valve;
4) Belt conveyor motor speed monitoring: quartz sand belt conveyor motor speed adjustment and control, fly ash belt conveyor motor speed adjustment and control;
5) Electronic belt scale weighing monitoring: quartz sand electronic belt scale weighing adjustment and control, fly ash electronic belt scale weighing adjustment and control;
6) Screw conveyor motor speed monitoring: cement screw conveyor motor speed adjustment and control, fly ash screw conveyor motor speed adjustment and control, lime powder screw conveyor motor speed adjustment and control;
7) Mixing bin monitoring;
8) dryer monitoring.
2.2 Composition of batching control system
The batching system is based on the existing metering control equipment such as electronic belt scales, screw reamer pumps, nucleus scales, etc. The corresponding Lon Works nodes are connected to the inputs of these existing batching control equipment, and the non-LonWorks fieldbus equipment is integrated into the fieldbus to constitute a fieldbus-based control system. The nodes used here mainly include: PCLTA-10 adapter card and PC and connect to form the Lon Works network management and monitoring node; Lon Works/4-20mA conversion node will comply with the DDZ-Ⅲ standard analog signal 4-20mA control equipment integrated into the fieldbus; Lon Works/485/232 conversion node will be the digital interface control equipment integrated into the fieldbus; Lon Works/485/232 conversion node will be the digital interface control equipment integrated into the fieldbus; Lon Works/485/232 conversion node will be the digital interface control equipment integrated into the fieldbus. The Lon Works/485/232 conversion node integrates digital interface control devices into the fieldbus; the monitoring and control of switching quantities is accomplished by the I/O modules of the Lon Works control node.
2.3 Dosing Flexibility Control
After the feeding and metering equipment of different types and components are integrated into the field bus through LONWORKS node, each equipment is no longer an information island, and they can coordinate their work under the control of the ingredient management software, so as to realize the flexible production of different parts of dry powder ingredients and quickly meet the needs of different users for products. Each equipment is no longer an information island, they can work in coordination under the control of ingredient management software, realize the flexible production of different components of dry powder ingredients, and quickly meet the needs of different users for products. The functions of dry powder batching production monitoring and management software include dry powder type matching expert database, dry powder matching setting, output setting, productivity setting, flow distribution of each component, tolerance setting of batching equipment, upper and lower limits of bunker material level setting, selection of independent and online control, switch between manual and automatic, switch between debugging and operation, indication of actual flow of batching equipment, indication of equipment operation, abnormal alarm, troubleshooting and historical tracking.
3 Conclusion
Dry powder flexible control system is a control device that realizes a variety of dry powder raw materials to be fed, weighed, mixed and packaged in a fully automated, real-time and high-precision manner in strict accordance with a certain scientific proportion. The control center adopts fieldbus based on Lon Works standard for monitoring and control, with simple structure and free wiring, and saves equipment investment by integrating non-LonWorks fieldbus equipment into the fieldbus through node controller. It utilizes the network technology and information technology of fieldbus to realize on-line monitoring and control process for quick replacement of different dry powder raw material ratios and dry powder material products of different natures.