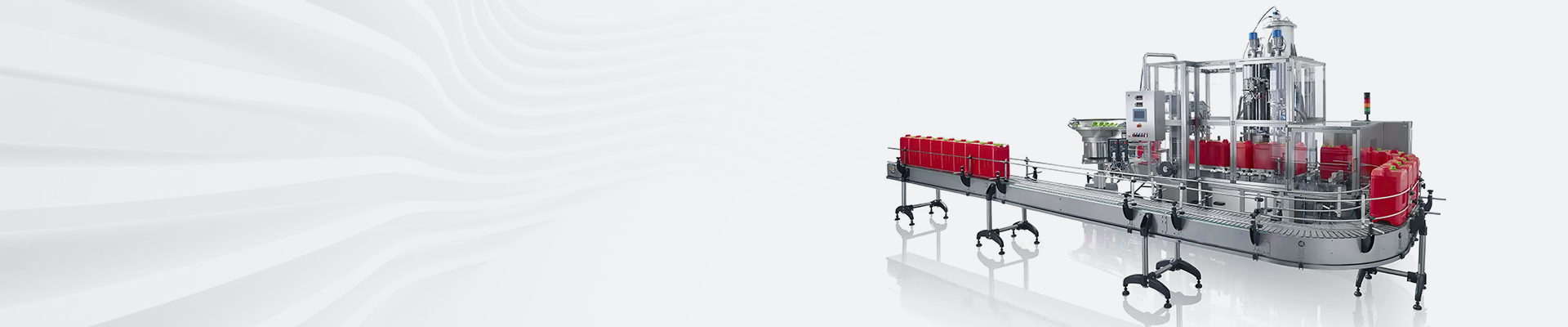
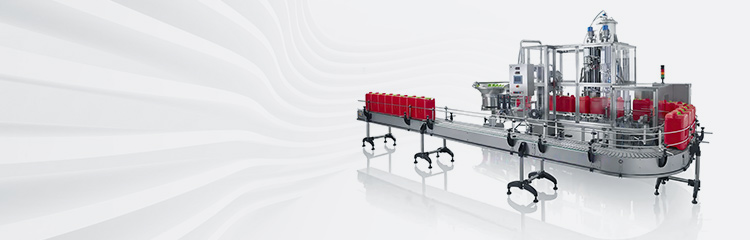

Summary:The automatic liquid filling machine is a set of filling equipment independently developed by the editor organization and used in production. It mainly includes a main control unit, a counting unit, a fast filling valve control unit, a slow filling valve control unit and a PLC controller connected to the liquid storage unit. Fast filling valve and slow filling valve of the tank.
As people's requirements for food hygiene continue to improve, the process of food filling package Pei is increasingly important. Automated indiscriminate way not only can reduce the labor intensity of the operator, and its ability to minimize the personnel and the contact of exposed food, food quality assurance plays a good role. Currently more widely used non-vapor liquid filling methods are mainly two: low vacuum filling and flow meter filling. Weighing filling belongs to an emerging filling method, with its wide range of adaptability, high filling accuracy, stable operation, simple maintenance and other advantages to get rapid development.
2 various filling method characteristics are summarized
(1) low vacuum filling
This filling method is in the bottle pressure is lower than the atmospheric pressure for filling, the use of vacuum, making the product in the tank into the bottle to go, and the bottle will be higher than the set level of liquid suction, to achieve the purpose of quantitative filling, this filling method of filling machine structure is relatively simple, high productivity, the early stage of the use of a fairly wide range of earlier automatic filling method.
However, because of its quantitative way is fixed filling level, but the container due to deviations in the manufacturing process, the capacity of each bottle varies greatly, the level of the same net content deviation is larger, especially similar to PET, PE cans, in the filling process, by the impact of negative pressure, the container volume change is larger 2. In addition, because of negative pressure filling requirements container in the filling process is airtight, so the filling equipment filling valve must be in contact with the bottle mouth, this is the filling equipment, the valve must be in contact with the bottle mouth, this is the filling machine. must be in contact with the mouth of the bottle, which can easily lead to contamination of some sensitive food products. At present, this filling method due to the relatively simple structure of the equipment, equipment cost is relatively inexpensive, in some low value-added beverage industry is very widely used.
(2) flowmeter type filling
Flowmeter type Huai installed in each filling valve to install a flowmeter to measure the flow of liquid volume through the broad door, when the liquid volume reaches the set value when the valve is closed, so as to achieve the purpose of quantitative filling. This filling method is relatively low vacuum indiscriminate filling method of high precision, and non-contact filling, to avoid the hidden danger of bottle contamination, the valve structure is simple, easy to clean, and is not affected by the degree of container hardness and softness, to maintain a constant filling capacity. The filling method has the disadvantage of relatively narrow adaptive surface, can not deal with easy to produce bubbles or low conductivity of the liquid, if the product has produced bubbles, such as soy sauce, milk, etc., the density of the liquid is not uniform, the volume of liquid and the weight can not correspond to, so the meter can not be correctly quantitative. And for low conductivity or non-conductive liquids, such as cooking oil, etc., the flow meter can not be volume measurement.
(3) weighing type beach filling
Weighing filling method is similar to the flow meter filling, each filling valve and a dynamic electronic scale corresponds to the bottle placed on the electronic scale, when the weight of the scale reaches the set value, the United States closed the valve, so as to achieve the purpose of quantitative. The filling method not only has the advantages of flowmeter filling method, but also overcome the flowmeter filling method to adapt to the narrow surface of the problem, not only for liquid filling, but also for low viscosity sauces, pastes and other materials indiscriminate filling.
From the above comparison can be seen, the weighing technology applied to liquid filling can be an effective solution to the conventional indiscriminate filling methods exist in some of the same problem. Therefore, some well-known domestic industry filling equipment manufacturing enterprises are vigorously develop weighing filling equipment.
3 a weighing filling system introduction
A weighing filling system introduced here is a set of filling equipment developed by the editorial organization and applied to the production of independent research and development, automatic filling machine mainly includes the main control unit, counting unit, fast filling valve control unit, slow filling valve control unit PLC controller, as well as connecting the liquid storage tanks of fast filling valve and slow filling valve.
The working principle of the liquid filling machine is that the main control unit is used to drive the crawler controller for transferring bottles to be filled, and after receiving the trigger from the counting unit, the push bottle controller is driven to transfer bottles waiting to be filled to the electronic scale, the fast valve and the slow valve are located on the top of the electronic scale, and the fast-filling valve control unit and the slow-filling valve control unit are used to open the fast-filling valve and the slow-filling valve for filling, respectively. When the electronic detects that the filling weight reaches the first - set value, the fast filling valve unit is triggered to close the fast filling valve, and when the electronic scale detects that the filling weight reaches the second set value, the slow filling valve unit is triggered to close the slow filling valve.
The following combines the basic principles to explain the specific working process of the automatic filling machine.
The bottle feeding conveyor sends the bottles to be filled into the machine and arranges them neatly. The counting sensor records the number of bottles entering the machine and transmits the signal to the PLC controller, when the set number is reached, the PLC controller controls the bottle stopping cylinder to block the back of the bottles from continuing to enter. This completes the first step of the bottle feeding process.
After the bottles enter the machine, the bottle cylinder pushes the bottles to be filled to the electronic scale, the number of electronic scales can be set according to the speed requirements of the production line, a number of sets. After the magnetic induction switch confirms that the bottle is pushed into place, the cylinder returns. At the same time, the electronic scale has completed the weighing of the empty bottle weight and zero, and complete the "tare" process. After completing the peeling process, PLC control filling valve open, start filling. Electronic scale real-time weight information transmitted to the PLC, PLC will be the value and set the filling target value for comparison, when the weight finally reached the set target value, PLC control filling valve closed. At this point the filling of the bottle is completed.
In the filling at the same time, the next into the bottle process has been completed simultaneously, under the action of the bottle cylinder, the empty bottle is once again pushed to the electronic scale, while the empty bottle has been filled to the end of the full bottle pushed to the bottle conveyor belt, bottle conveyor belt will be filled with bottles conveyorized out of the machine, so that the entire filling process is completed. One of the key requirements of the system is the configuration of fast-fill valves and slow-fill valves, in order to accurately control the net filling content. In the beginning of the filling, in order to reduce the impact of the material falling into the empty bottle, to prevent the material from splashing, filling the flow rate is not easy to be too large, so you can just open the slow filling valve, this state of the valve's flow rate is small, the impact of the material is small, when the filling of the material to reach a certain amount of time, you can open the valve to increase the flow rate of the fast filling to speed up the filling speed. As mentioned earlier, when the first set value of the electronic scale is reached, the fast filling valve will be closed, and then only the slow filling valve to continue filling. The purpose is to approach the target filling volume, in order to reduce the impact of the material and from the filling nozzle to the mouth of the bottle in this period did not fall into the bottle weight deviation of the material (called "flight error") caused by the final filling volume deviation, gentle slow filling is more conducive to reducing such deviations.
In addition to reasonable control of the filling valve flow rate, control of the liquid level of the tank is also very important to maintain a constant pressure and level in the tank, is the key to effective control of the "flight error". Therefore, the system is configured with a PID pressure regulation system and level sensors, used to control the pressure and level of the tank in a certain range.
4 filling system in the practical application of advantages
The weighing and filling machine through the electronic scale combined with PLC for automatic weighing of materials, liquid materials to achieve continuous automatic filling, can improve efficiency and reduce the labor intensity of workers. As each bottle is "tared" by the electronic scale before filling, the effect of container tare deviation on the filling result is eliminated, ensuring the filling accuracy. The filling volume can be easily adjusted by adjusting the setting value of the electronic scale without mechanical adjustment. The filling speed is greatly improved by pressurizing the liquid storage tank, and the pressure control of the liquid storage tank adopts the PID control principle, which effectively reduces the pressure fluctuation and ensures the stability of the pressure. Adopting two kinds of filling speed control methods, it not only improves the filling speed, but also ensures the filling precision. If used with the sorting system, one machine can simultaneously can different weights of products, improving the flexibility of the production line and equipment utilization.
For the filling of the net content deviation, according to a 5kg product specifications, compared to the fixed volume filling method, from the original average deviation of 15 grams to the present 6 grams, reducing the filling deviation loss, the annual reduction of filling deviation loss is a very substantial income, such a level of net content control is artificial or other filling methods can not be compared.
Due to the product type specification is more, a production line to produce a variety of specifications of the product is more often, and should change the system of equipment in the process of converting varieties almost do not need to replace any mechanical parts, only in the control system to modify the filling target value can be, greatly improving the utilization rate of the equipment, so such a filling equipment has been widely used. At present, this filling method also with its obvious advantages, at home and abroad in the beverage food industry has been the rapid development and application.
5 Conclusion
Weighing filling machine using high-precision dynamic weighing scale, combined with fast filling valve and slow filling valve, to achieve the precise quantitative filling of containers, can minimize the loss of products, its successful application, to ensure product quality, improve production efficiency and cost savings play a very important role.