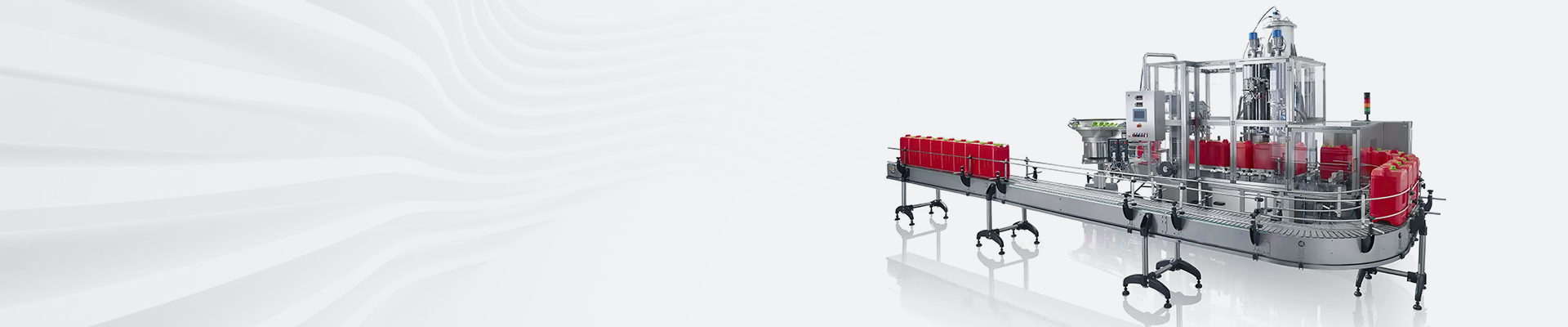
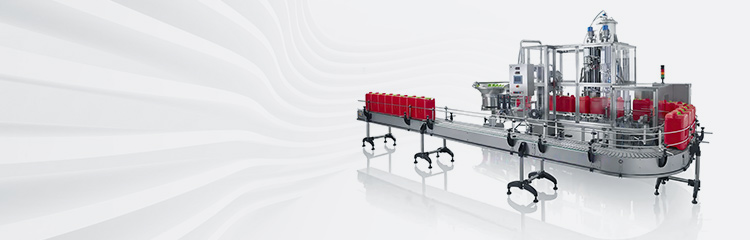

Summary:The weighing module generates analog electrical signals that are proportional to the weight of the reaction kettle, and connects them to the junction box through parallel connection. The output is adjusted according to their respective stress conditions, and then the summarized signals are sent to the weighing display terminal for display. Output weight data.
Selection of dynamic or static load
Weighing modules are classified as static or dynamic load. The way of feeding determines the type of weighing module, when the material is fed vertically with conveyor or pump to the bucket, tank, kettle and tank, static load module can be selected; when the material is conveyed horizontally to the weighing platform or container or when the tank is with agitation, horizontal impact force will be generated, then the dynamic load module should be selected.
Quantity selection
Cylindrical containers generally use three-point support, three modules as a group (fixed, semi-floating and floating each one), rectangular containers to four-point support is appropriate, four modules as a group (fixed and semi-floating each one, floating two), in special circumstances, in order to improve the rigidity of the container, you can increase the support point. On the basis of four modules configuration, increase the module, all choose floating structure.
Capacity selection
The capacity of a single weighing module W ≥ 1.5k (W0 + WS)/n
Where: W0 ---- the weight of the empty tank, i.e. the weight of the scale unloaded
WS ---- large load that may be loaded into the tank
n---- number of weighing modules
f----standard safety factor, generally taken as 1.5
k---- additional safety factor (wind, shock, vibration, etc. on site)
Example: if the weight of the empty tank is W0=1200 kg, the load in full capacity is WS=2300 kg, the standard safety factor F=1.5, the additional safety factor k=1 (assuming little influence of wind, shocks, vibrations, etc.), and the number of weighing modules n=3.
Then the capacity of a single weighing module W≥1.5k(W0+WS)/n
W≥1.5×1(1200+2300)/3=1750kg.
Therefore, it is enough to choose 2000kg capacity for each weighing module.
Material and selection
Two kinds of materials are used for the module, the static load module is made of carbon steel except for the pressurized head, which is used in general occasions, and the stainless steel weighing module is used in occasions such as contact with corrosive substances and humidity.
Selection of suitable weighing instruments, junction boxes and cables.
Different models of weighing instruments will have different display speed and accuracy, so pay attention to choose suitable weighing instruments, junction boxes and cables which are compatible with the weighing module.
Precautions for use
Some issues to consider when installing a static load weighing module
Requirements of the support structure
In the tank scale (bucket scale) system, the skewing of the bracket structure will affect the accuracy and repeatability of the scale, so the design of the bracket structure of the weighing module has the following requirements:
(1) The angle with the horizontal line caused by the skewing of the bracket cannot be greater than 0.5°;
(2) The angle with the horizontal line caused by twisting or skewing of the base support structure cannot be greater than 0.5°;
(3) Base bracket structure deflection (deflection) consistent.
Influence of bracket deflection on weighing modules. Where the bracket on the weighing module is not horizontal, there is a lateral force applied to the sensor; the upper bracket and base bracket structure is adjusted to a straight line without lateral force;, the base bracket structure of the weighing module is not horizontal, there is a lateral force applied to the sensor.
The deflection of the support structure of a tank scale should be as small as possible, and the deflection of all pivot points should be consistent. Excessive deflection can cause deflection variations in the tank inlet and outlet tubes, resulting in linearity errors. When the deflection is not consistent at all points, repeatability errors may occur as well as return-to-zero errors due to creep.
In some cases, the tank scale in the weighing state, the tank column will be deflection, if the deflection is too large, it will affect the accuracy of the weighing and the phenomenon of unstable readings. In this case, the column needs to be reinforced with sufficient stiffness.
Uniform adjustment of weighing module and support beam
The centerline of the load applied to the load cell should coincide with the centerline of the support beam of the weighing module. In order to prevent the support beam from torsion during loading, reinforcement webs can be added.
Reinforcement of the support structure
When the load applied to the metal support increases, the supporting part will easily bend and increase the deflection, which will affect the accuracy of the tank scale. When the weighing module is installed in the middle of the support beam, the resulting deflection is large. If this type of installation is unavoidable, it is necessary to reinforce the support beam so that the deflection is reduced to small. Weighing equipment is a common method of reinforcement.
A better way to reduce deflection is to install the weighing module close to the column, ensuring that the module is installed on a structural beam of the same dimensions, so as to avoid repeatability errors and return-to-zero errors caused by different deflections. Close to the column, the mounting position is more suitable. In the center of a horizontal beam, the mounting position is less suitable.
Interaction between cans
When two tank scales are mounted next to each other, their weighing will interfere with each other if a common mounting base is used. There are four types of mounting methods, the weighing module mounting method, which has a small effect on each other, and the mounting method, which has a large effect on each other.
A good option for weighing equipment, mounted on a concrete foundation, has little effect between the two tanks due to the small deflection of the concrete. Mounting the weighing modules near the columns, where each tank has its own independent support structure, limits the deflection and can reduce the mutual influence. The weighing module is mounted in the middle of the horizontal beam, the deflection is higher, but each tank has its own independent support structure, which reduces the mutual influence. The weighing module is installed in the middle of the horizontal beam and the two tanks are placed on the same common support beam, which results in high deflection and high mutual influence.
Safety considerations
In order to ensure the safety of the tank scale and prevent the tank from tipping back due to wind, impact, vibration and other influences, safety measures should be considered. The usual method is to add limit brake rods or anti-tipping bolts, which can be used at the same time if necessary.