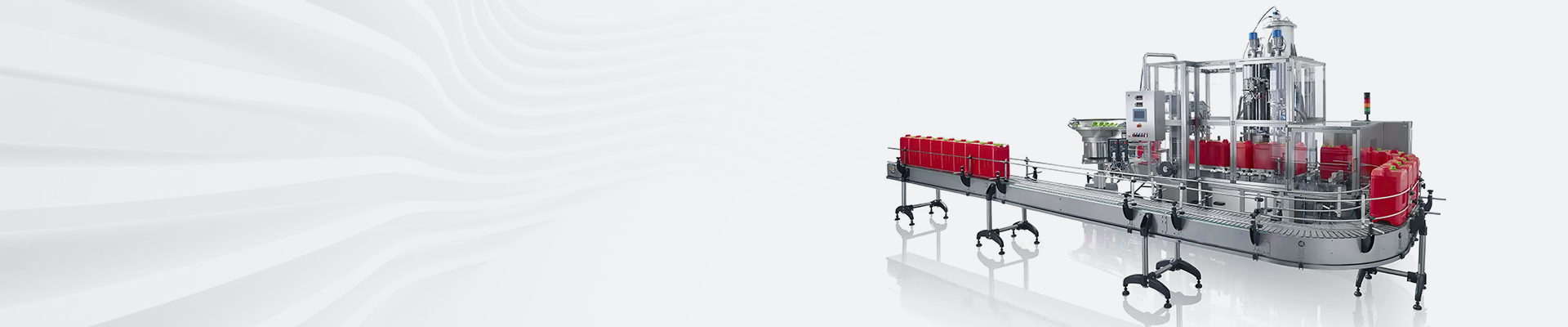
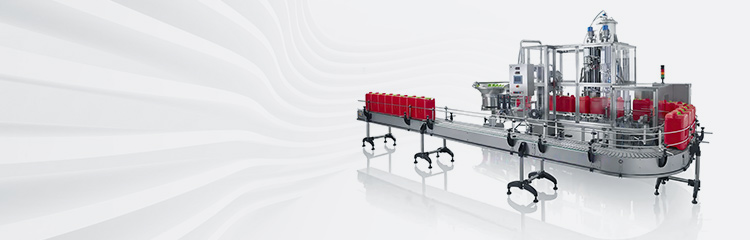

Summary:The dosing system utilizes the rate of material reduction per unit time to account for the material flow. The whole feeding machine includes raw material storage tank, raw material conveying device, hopper scale, unloading device and flow calculation system. Weighing instrumentation to control the actual feeding flow compared with the set value, the use of PI regulation method, the accuracy of the system can reach 0.5 ~ 1%. (Different raw materials have differences), the following through the powder system to illustrate the flow dosage system to realize the method.
Most of the current production of sealant is the use of batch method, generally the first use of kneading machine and other mixing equipment to the polysiloxane, fillers and additives for the initial mixing, and then move thou planetary mixer for further mixing, adding pigments, crosslinking agents, coupling agents, etc., through the vacuum foaming to get the product. The advantages of the batch method are convenient operation and simple production control. However, there are many shortcomings: the material is exposed to the air when transferring easy to produce crust, material transfer loss is large, poor production stability, limited production capacity, high labor intensity, and so on.
The new sealant continuous feeding system adopts twin-screw extruder as the main equipment for continuous production of glue dispensing process, auxiliary metering system, cooling system, filtration system, buffer system and dispensing equipment, etc., to realize the whole process of automated production monitoring, the production method has a high degree of automation, high production efficiency. The production method has the advantages of high degree of automation, high production efficiency, low labor intensity, large production capacity, low material and energy loss, stable product quality and so on.
Overview of the main process
In the process of continuous dosing machine production of sealant, polysiloxane and filler are continuously and accurately fed into a first twin-screw extruder by corresponding metering devices for premixing, degassed and cooled to obtain a base material, and then enter a second twin-screw extruder for further mixing and dispersion, and additives and catalysts are added in the process to obtain a finished product, and then enter a packaging process to obtain a final product. The process flow control of the feeding system and the control of the screw extruder are the key points of the process control, and the stability of its control has a great influence on the quality and output of products. Therefore, it is necessary to provide an advanced feeding system to ensure the normal production and improve the quality and efficiency of production. Therefore, DCS is selected to realize the automation of the whole production control.
Control system composition
DCS dosage system consists of an engineer station (also used as an operator station), an operator station, a control station, a gateway communication station, the engineer station is equipped with the corresponding configuration platform and system maintenance tools, the control station to complete the real-time control of the entire industrial process, by the main control card, data forwarding card, IVO cards, power supply units, etc., the control station's various cards can be configured in a redundant manner, the control station has a fault self-diagnostic function, control station With self-diagnostic function, the core cards of the control station are redundantly configured according to 1:1 hot standby, and can be automatically switched without disturbance in case of failure. The operation station is responsible for providing man-machine operation interface, receiving real-time data of the process from the control station, and transforming them into corresponding process variables to be displayed on the monitor for the operator to monitor and operate, and the gateway communication station is mainly responsible for accomplishing data linkage with other heterogeneous systems (PLC), in order to accomplish the real-time control function in the DAC system. The gateway communication station mainly accomplishes the data connection with other heterogeneous systems (PLC) to complete the monitoring of the whole production process on the DCS operation station.
Flow system control and realization of the flow system introduction of raw materials through the spiral feeding device from the raw material storage tanks to the hopper scale, the raw materials in the hopper through the weighing module weighing, the weight reaches the upper limit to stop feeding, the weight is lower than the lower limit of the start of the feed. Measuring hopper weight is continuously changing, in 0-t1 time by the discharge pump from the measuring hopper, this time not feeding, measuring the weight of the material in the hopper is a downward trend, t1 ~ t2 time, because the material in the measuring hopper has reached the lower limit need to feed, feed the weight of the measuring hopper to increase the weight of the measuring hopper, t2 after the measuring hopper has reached the upper limit of the material to stop feeding.
Control idea of flow system
Polysiloxane is a high viscosity (30,000-70,000 CP) liquid, filler (calcium carbonate, fumed silica, etc.) is a powder, the use of a general flowmeter can not be measured. We use the principle of loss-in-weight method to realize the flow calculation of two types of raw materials, the method is to use the rate of material reduction per unit time to account for the material flow. The whole feeding machine includes raw material storage tank, raw material conveying material device, hopper scale, unloading device and flow calculation system and other components. Weighing instrumentation to control the actual feeding flow compared with the set value, the use of PI regulation method, the accuracy of the system can reach 0.5 ~ 1%. (Different raw materials have differences), the following through the powder system to illustrate the realization of the flow dosage system.
Flow system realization method
The newly collected weight is expressed by W0, and the weight collected in the first 1 second is W1...... the weight collected in the first n seconds is Wn. When this second passes, W0 is re-collected, and the weight of the old n seconds W0~Wn-1 is automatically pushed all the way to the weight value of the new n+1 seconds, i.e., it is replaced by the present W1 a W0, and the weight value of the old first n seconds Wn is automatically lost, so that the weight value Wn is automatically lost. The weight value Wn is automatically lost, so that every second automatically refreshes the weight value of each second of the current n+1 seconds. Then through the formula FI201 = (Wn-W0) x 3600/n and then transform the range is equal to the flow calculated value.
Calculated using the above method of flow value fluctuations or larger, can not be flow control, the need for filtering calculations, the method is to collect x seconds of each second of the flow value, the next second of this x each flow value is automatically refreshed, the x flow value of all the sum and then divided by x to derive an average, that is, the filtered flow. In the t1~t2 time period, because the material in the hopper has reached the lower limit to be fed, feeding the weight of the hopper increased, can not use the above computer methods, we are using the 0~t1 time period of the calculation of the flow rate value, remove the largest and smallest flow rate, and then calculate the average of the remaining flow rate value as the flow rate in the t1~t2 time.
Control realization of flow rate
Because the powder and rubber ratio is fixed, so two flow single-loop control can be used. Normal control of powder flow control block diagram shown in Figure 4. Powder flow control: the input is filtered powder flow, by controlling the powder discharge pump speed; base rubber flow control and powder flow control is the same. In the weighing hopper powder and base glue to reach the low limit value, the need to re-feed, this system uses DCS control, loop 0 (powder flow control) after the power on, you can calculate the 0 ~ t1 section of the time, expressed as n1, and 11-t2 time period, expressed as n2, calculate the t1 before x seconds (x is greater than n2 is less than n1, different materials, different materials), the output value of the circuit 0 in x seconds per second The output value of loop 0 is accumulated per second in x seconds, and the accumulated number of seconds (x) is calculated at the same time. The average value of the output of loop 0 in the dosage system for the following 11-t2 time period is obtained by dividing the accumulated value of the output of loop 0 per second by the accumulated number of seconds (x). The same method to calculate the output average value of loop 1 (rubber flow control) dosage system later, with the above method of calculating the flow value fluctuations or larger, unable to flow control, need to filter the calculation, the specific filtering method is to collect a number of data (such as 9) for a group, remove a maximum value and a minimum value, the rest of the data to take the average, as a valid measurement, that is, the filtered flow.
This system has been put into operation on the silicone sealant device, running well, the control function fully meets the requirements of the process, mainly with the following characteristics:
1) Improved product quality and yield. Convenient production management mainly through the computer operator interface, you can optimize the production process parameters online, improve equipment utilization, and greatly reduce the labor intensity of the operator;
2) Stable and reliable operation of the system, uniform control of feed flow, narrowing the difference between product batches and stabilizing product quality.
3) Through the gateway communication station will PLC data into the DCS system, realize the unified monitoring, greatly improve the enterprise instrumentation and control maintenance personnel and production management personnel's technical level.