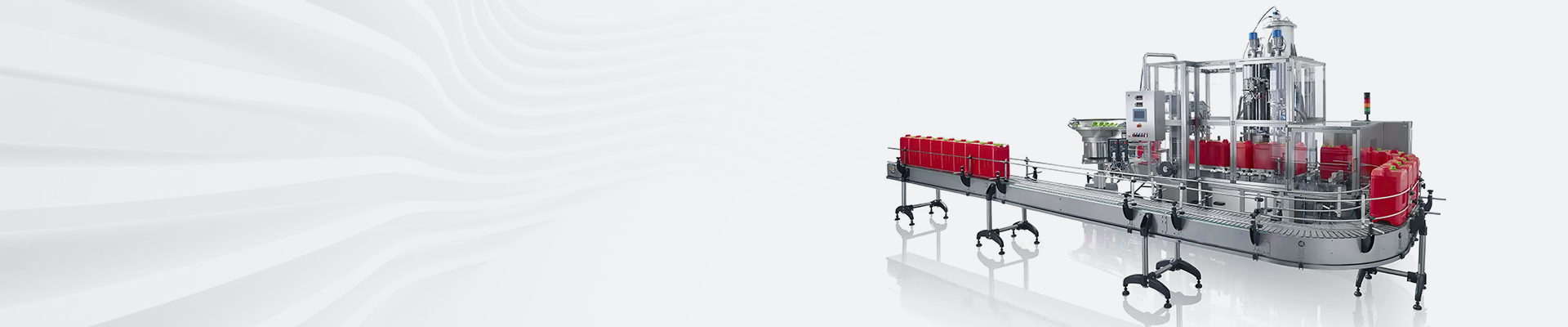
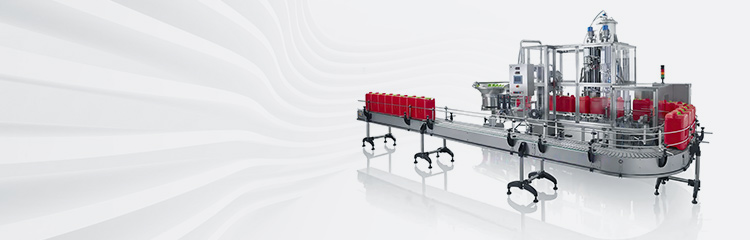

Summary:The batching system is a continuous weighing and measuring equipment used in various industrial fields.It combines the different advantages of dynamic weighing and static weighing, and gradually replaces continuous weighing equipment such as belt scales and spiral scales.
Dosing components and characteristics
Automatic batching systems are used in various industrial fields as a continuous weighing and measuring equipment. Combining the different advantages of dynamic and static weighing, it gradually replaces continuous weighing equipment such as belt scales and screw scales, and is used in more and more industrial fields.
Basic Principle and System Composition
The hopper scale and the feeding mechanism as the whole scale, through the weighing instrument or the upper computer constantly sampling the weight signal of the scale, calculating the weight of the measurement module in the unit of time as the ratio of the instantaneous flow rate, and then through a variety of hardware and software filtering technology, resulting in the "actual flow rate" can be used as the object of control.
The basic composition of the dosing system can be divided into two major parts: the equipment system and the control part.
The equipment part mainly consists of hopper scale, feeding feeder, unloading feeder, suspension device. The control part mainly consists of load cells, signal amplifiers, input and output interfaces, host (host computer) and so on.
The dosage process of the feeding system is divided into two stages: feeding and unloading. After the dosage starts, the feeding feeder is started firstly, and the controller detects and samples the weight of the material on the hopper scale, and stops feeding when the weight of the material on the hopper scale reaches the upper limit value set for dosage. At the same time, the controller detects and samples the material weight of the hopper scale, and stops feeding when the material weight of the hopper scale (feeding quantity) reaches the upper limit value set by the dosage. In the unloading stage, the controller starts the unloading feeder to unload the materials in the hopper scale to the next level of material transfer equipment to send away. When unloading, the controller detects and samples the weight of the material in the hopper scale, and when the weight of the material in the hopper scale reaches the lower limit value set by the dosage, it will re-feed the material to the hopper scale. However, after the second feeding phase begins, the unloading feeder continues to unload without stopping.
The feeding system continuously weighs the whole feeding system including the hopper scale and the feeding mechanism, which is equivalent to a static scale; meanwhile, the discharge flow of the feeding mechanism is controlled by frequency conversion speed regulation.
The reduction of material weight Δd/Δt per unit time in the hopper scale of the dosage control system corresponds to the feeding flow of the dosage. The dosage controller compares dv/dt with the preset feed flow rate and automatically corrects it by adjusting the feeder speed, thus maintaining an accurate feed flow rate.
When the weight of the material in the hopper scale falls below the preset value, the weighing module will lock the feeder speed and keep the downcomer mechanism feeding in a volumetric manner, while opening the fill valve for fast feeding. When the weight of material in the hopper scale reaches the high preset value, the charging valve will be closed automatically. At the same time, the dosage controller automatically switches the discharging mechanism to the weighing mode.
From the point of view of working principle and structure, the automatic dosage system has the characteristics of both static and dynamic weighing. For the traditional dynamic weighing and measuring methods, such as: belt scale, punch plate flow meter, spiral scale, etc., although with continuous weighing, realize the process of high efficiency, but there are system accuracy is not high (generally lower than in the 0.5 ~ 1%), the maintenance of large amount of problems; and static weighing methods, although greatly improve the system measurement accuracy (up to 0.1%, or even higher), but can only meet intermittent The static weighing method, although greatly improving the measurement accuracy of the system (up to 0.1%, or even higher), can only meet the intermittent batch feeding (batching) applications, and can not maximize to meet the high efficiency and high output requirements of the modern process industry, not to mention that some industrial applications themselves require continuous feeding (batching), do not allow the existence of intermittent. The emergence of the dosage system, just both the advantages of the two, to make up for their shortcomings. The main advantages are: high system accuracy
When the dosing system is in operation, the measurement of the silo is actually done in a static state and is done after loading and unloading each (one?) time. Measurements are made once and the flow rate is calculated from the difference between the two weights measured in the two operating states. The difference and the flow rate of the given value error can also be compensated in the next cycle, and these two weight measurement time in a few minutes to complete, there is no sensor zero drift and temperature drift and other effects. Therefore, it can obtain quite high measurement accuracy, the system measurement accuracy can reach 0.5%, even 0.2%,.
Fully enclosed stainless steel structure, suitable for a variety of harsh site.
The equipment system is all steel (dosage system generally uses stainless steel), suitable for poor environmental conditions, and has the characteristics of ruggedness, low maintenance, not afraid of high temperature materials.
Many industrial and mining enterprises are big consumers of electricity, so how to save energy is also a very important topic. As the batching system adopts fully closed structure, no dust is generated during the batching process, eliminating the dust removal device, simple structure, no need to match the belt scale and other supporting equipment, which not only saves equipment investment, but also saves electricity and improves the production efficiency.
Maintenance-free and simple calibration
As the dosage system is through the measurement of weight difference to calculate the flow of material measurement, there is no such as belt scales and other dynamic scales in the existence of zero drift (belt deflection, sensor displacement, material impact vibration belt slippage, belt sticking material caused by the impact of), material adhesion, deformation of the mechanical structure of the scale body and other factors to ensure long-term stability of the system measurement accuracy, basically do not need maintenance and a lot of calibration work. Calibration work.
According to its measuring principle, it can not only carry out physical calibration, but also online calibration in production operation. That is, the accuracy is calculated according to the difference between the upper and lower limit weights of the materials in the hopper scale and the dosage system flow rate display value comparison. This calibration method is characterized by simplicity and convenience, which saves money and effort.
Fully integrated automation technology is the core idea and leading concept of automated dosage system technology and products, TIA set a high degree of integration and unity and unprecedented openness in one, standardized network architecture, unified programming configuration environment and a high degree of unity of the data integration, so that the TIA for the enterprise to achieve the horizontal and vertical integration of information; leading communication standards, component-based automation technology ( CBA) and IT integration. CBA) and IT integration make TIA truly open to the global automation market with its range of products and services.